Ever heard someone in a factory shout, “Check the 6Ms!” and wondered what on earth they meant? That’s not just manufacturing jargon—it’s a framework that can make or break a production line. In the world of making things, the 6M method digs into every factor that could go wrong (or right) in your process: Man, Machine, Material, Method, Measurement, and Mother Nature.
This isn’t just theory from some dusty textbook. Ask anyone running a plant—one slip on any M and you’re either losing money or getting calls about defective products. A surprising fact: Many government-backed improvement schemes in India use the 6M check when auditing factories for support or grants. So if you’re aiming to nail quality or unlock funding, understanding these six factors is more important than ever.
Plenty of manufacturers skip this step, thinking it’s only for big brands. Big mistake. Even small shops can get hit, like that auto parts maker who ignored the right material and ended up halting production for days. If you want to keep things running smoothly and not waste cash, you’ll want to get familiar with how the 6Ms come together on the shop floor.
- What Are the 6Ms: Quick Breakdown
- History: Where Did 6M Come From?
- How 6M Shapes Quality in Manufacturing
- Common Mistakes and Real-World Examples
- Tips to Apply 6M in Your Plant
- 6M and Government Schemes: Why It Matters
What Are the 6Ms: Quick Breakdown
When people talk about the 6M in manufacturing, they're talking about six core factors that basically drive every part of your production process. Ignore any one of these, and things can spiral out of control pretty quick. Here’s what each 'M' stands for, and why it actually matters on the ground:
- Man: This is all about your people—operators, supervisors, engineers. Are they trained? Do they follow the right steps? Poor skills or lack of training often leads straight to errors and accidents.
- Machine: Think everything from an old lathe to a high-tech CNC. Machines need regular maintenance. Skipping this step is a top reason for downtime and can tank your productivity.
- Material: You can’t build great stuff with bad stuff. If your raw materials are off, expect quality issues—and returns from customers.
- Method: These are your work instructions. Is everyone on the same page about the process? If methods are unclear, you get inconsistencies at best, and disasters at worst.
- Measurement: How do you know things are working? From micrometers to software, the tools you use to measure must be accurate. Wrong measurements can mean out-of-spec products slipping out the door.
- Mother Nature (Environment): It’s not just heat, dust, or humidity—things like power fluctuations or even local pollution counts. The environment can quietly mess with results.
Here’s a quick cheat-sheet for the 6M in manufacturing:
M | Main Focus | Common Issue |
---|---|---|
Man | People, skills & training | Operator error |
Machine | Tools & equipment | Breakdowns, wear |
Material | Raw inputs | Defects, wrong specs |
Method | Process steps | Wrong/unclear process |
Measurement | Inspection, data | Faulty readings |
Mother Nature | Environment | Heat, humidity, power |
An engineer from Toyota famously said,
"When something goes wrong on the shop floor, it’s almost always one of the six Ms.”
So if you ever get stuck troubleshooting a problem, this simple checklist is a lifesaver. Most lean manufacturing process systems and quality checks today can be traced back to this classic framework. And with the latest government schemes pushing for higher standards, knowing your 6Ms isn’t just helpful—it’s a must.
History: Where Did 6M Come From?
The roots of the 6M in manufacturing go all the way back to Japan in the 1950s. Companies like Toyota needed a system to spot what was messing up their production lines. Out of that came the ‘Ishikawa Diagram’ (or the fishbone), thanks to Kaoru Ishikawa. Ishikawa put together a simple tool for teams to find root causes when things went south. Instead of running in circles, managers just checked the main categories—those became the six Ms: Man, Machine, Material, Method, Measurement, and Mother Nature.
Originally, people started with only four: Man, Machine, Material, and Method. Over the years, factories got more complex, and Measurement plus Mother Nature joined the mix. By the 1970s, the full 6M in manufacturing lineup was in play in Japan and quickly spread worldwide—especially with lean manufacturing gaining steam in the 1980s. Big names like Toyota and Honda plugged 6M into their production, and suddenly, it wasn’t just a Japanese thing. American and European factories picked it up, especially as quality standards like ISO 9001 became the norm.
Nowadays, you’ll spot the 6M model in not just auto plants but electronics, food processing, textile, and even government-backed schemes. For example, when India rolled out the Make in India campaign, many guidelines for small and medium factories referenced the 6M idea for audits and root cause analysis.
- It started as a tool in Japan after WWII.
- Popularized by Toyota and other manufacturers in the 1950s and ‘60s.
- Originally four Ms, expanded to six as factories grew more advanced.
- Now a global standard for process checks and quality control, even showing up in government manufacturing process audits.
Most people don’t realize every time a government team comes to audit or offer grants, they pull out a 6M checklist. Ignore these, and you risk tripping up on something preventable—usually costing you time and money. So, anyone running a shop or applying for government schemes should have a good grip on where the 6Ms came from and why they matter now.
How 6M Shapes Quality in Manufacturing
If you’re serious about top-notch products, ignoring the 6M in manufacturing is like shooting yourself in the foot. Each ‘M’ plays a real part in the smooth flow—from hiring your team to checking the final measurements on your line. Here’s how each factor ties into quality:
- Man: The right people with solid training keep mistakes down. In India, factories following skill upgrade programs funded by government schemes saw up to a 20% drop in rework because workers actually understood the process.
- Machine: Old or poorly-maintained machines sneak in defects. One survey by the Quality Council of India found that plants with regular machine checks reported 98% uptime compared to just 85% for those skipping maintenance.
- Material: Cheap or inconsistent raw materials always turn up in the finished product. Tons of recalls have happened just because suppliers cut corners—think textiles with the wrong dye batch, causing faded clothing and returns.
- Method: A messy SOP guarantees chaos. Good written processes let you repeat quality every time, while confusion doubles your chances of defect rates going up.
- Measurement: If your tools are off, your entire batch could be wasted. Calibration is not a fancy step for perfectionists—it’s the only way to make measurements trustworthy. Poor measurement tools cause up to 15% of defects, according to a 2022 industry report.
- Mother Nature: Don’t laugh—humidity and temperature swings are real saboteurs. Pharmaceutical plants in Hyderabad spend crores on climate control for a reason. Even small changes in weather can mess with paints, chemicals, and electronics.
Want a quick look at common issues seen in plants not using the 6M method? Check out these numbers:
6M Factor | Common Problem | Lost Quality (%) |
---|---|---|
Man | Poor training | 12 |
Machine | No maintenance | 14 |
Material | Low-grade suppliers | 10 |
Method | Unclear SOP | 8 |
Measurement | Uncalibrated tools | 15 |
Mother Nature | No climate control | 6 |
The punchline: anytime you’re stuck with quality complaints or scrap piling up, backtrack and check each of the 6M in manufacturing variables. Most headaches start from ignoring one—or more—of these basics. Think of the 6M approach as your safety net for quality and fewer surprises.
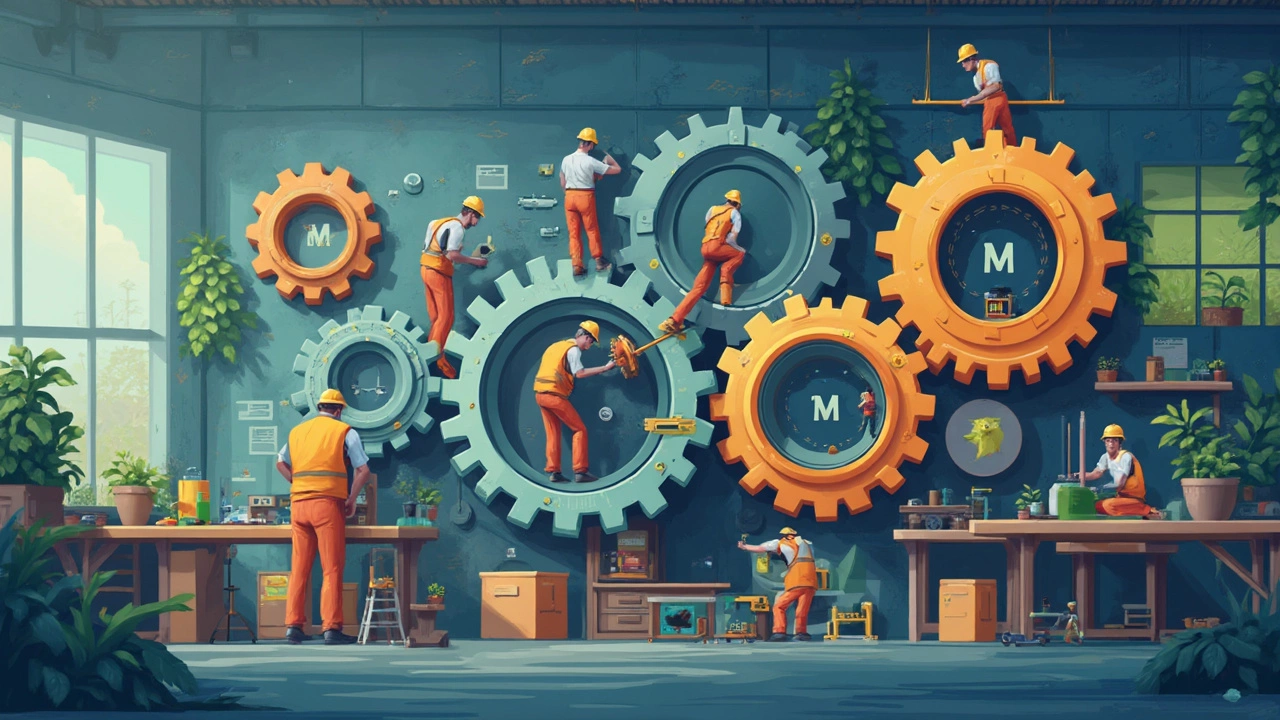
Common Mistakes and Real-World Examples
The whole point of the 6M in manufacturing idea is to catch problems before they cause a mess. But let’s be real—errors happen, and they usually come from teams thinking “We’ve got this” instead of double-checking. Here’s how it plays out on real factory floors.
First up, let’s talk about Materials. In 2023, a popular auto parts factory in Pune got stuck with hundreds of rejected batches. Why? They switched suppliers for cheaper steel but didn’t test it properly. That one oversight ran up losses over ₹20 lakh before anyone realized the steel wasn’t up to spec.
Next, Machine errors are classic. Remember that textile unit in Tamil Nadu? Their main loom was overdue for maintenance. Because nobody updated the maintenance method or checked the machinery, they faced a seven-day breakdown. Production halted, and they lost two major contracts. Avoiding this is simple—follow the calendar, and never skip service reminders.
- Man (People): A surprising number of rejects stem from poorly trained workers. One electronics assembly shop found their defect rate shot up when they hired new staff but skipped proper orientation. Turns out, if the crew doesn’t know the process, the line suffers. In fact, a 2022 survey by India Manufacturing News showed training issues caused 23% of all QA problems that year.
- Method: Shortcuts are tempting. There was a food packaging company that started skipping steps to save time. They ended up with food safety recalls, leading to inspection from the FSSAI, and penalties that cost them their reputation and cash.
- Measurement: A small switchgear company in Gujarat switched out their old gauges for a new model. They didn’t check the calibration, and shipments went out with the wrong tolerance levels. Clients sent everything back, and the company spent weeks fixing the mess.
- Mother Nature (Environment): In 2021, heavy monsoons knocked out the cooling system in a pharma plant. Nobody planned for that. Temperature-sensitive products spoiled, resulting in a product recall and fines under government quality schemes.
Here’s a quick look at how big these issues can get:
Mistake | Estimated Loss (INR) | Duration of Impact |
---|---|---|
Poor Material Quality | 20,00,000 | 2 weeks |
Machine Breakdown | 5,00,000 | 7 days |
Training Skipped | 3,00,000 | 1 month |
Environmental Damage | 8,00,000 | 10 days |
Bottom line? Every skipped step chips away at your profits or opens you up to regulatory headaches. Keeping an eye on the 6M in manufacturing isn’t just some paperwork exercise—it’s about stopping disaster before it starts.
Tips to Apply 6M in Your Plant
Getting 6M in manufacturing working for you isn’t rocket science, but you do need a clear plan. Here’s how to actually put each “M” to use—no buzzwords, just what works on real shop floors.
- Man: Skills matter, so map out who’s doing what. Set up quick training sessions for your operators even if they’ve been around for years. In many Indian clusters, factories that spent just two hours a month on skill refreshers saw a 15% drop in avoidable mistakes.
- Machine: Keep a logbook for every major piece of equipment. If you see repeat breakdowns, it’s probably time for preventive maintenance, not just another repair. Several auto suppliers use simple QR code checklists for daily checks—it’s fast, and workers actually use it.
- Material: Don’t just rely on your gut—test batches matter. Around Pune, fast-growing plants keep a database of approved suppliers, and they actually test materials on arrival. Just one rejected shipment caught at the gate saves days of wasted work down the line.
- Method: Standard Operating Procedures (SOPs) should fit your shop and be real, not just files in a drawer. Smart plants print them and tape them at workstations. The best ones ask workers to suggest tweaks, so everyone’s actually following what works.
- Measurement: Tracking numbers isn’t about showing off to bosses. Tag scrap, downtime, and rework—don’t blend the data or you’ll never spot trends. Plants that track every rejected part save up to 8% in production costs by pinning down and fixing repeat issues.
- Mother Nature: This one sounds odd, but temperature and humidity can ruin certain processes. Electronics and pharma lines install basic humidity sensors. If you’re running plastics, keep those coolers or dryers maintained. Seasonal changes in India throw off quality more often than folks admit.
Here’s a quick look at how tracking some basic 6M issues saved money for mid-sized plants:
6M Factor | Simple Fix | Monthly Savings (INR) |
---|---|---|
Man | Quick skill sessions | 7000 |
Machine | Preventive maintenance | 9000 |
Material | Supplier testing | 12000 |
Method | Easy-access SOPs | 8000 |
Measurement | Track rejects | 6000 |
Mother Nature | Monitor humidity | 4000 |
If you want to unlock benefits from government schemes, document what you change using the 6M in manufacturing method. Auditors love it, and you’ll spot issues early—way before they blow up your schedules or budget.
6M and Government Schemes: Why It Matters
If you run a factory or want to start one, understanding the 6M in manufacturing isn't just about better products—it's key for tapping into government support. Most new government schemes, like the Ministry of MSME’s Zero Defect Zero Effect (ZED), push for strict control over every single M. This isn’t just paperwork—auditors actually walk through plants and ask to see proof that you're keeping tabs on all six factors before handing out subsidies or certifications.
Here’s the deal: If you want that bank loan under the government schemes manufacturing banner, or access to markets via Make in India, they’ll often expect you to show a risk assessment report or an action plan—both built around the 6M model. And it really pays off. Factories that follow 6M in manufacturing can cut defect rates by up to 40%, according to a 2023 survey from CII.
Scheme Name | Requires 6M Analysis? | Main Benefit |
---|---|---|
ZED (Zero Defect Zero Effect) | Yes | Subsidies, faster approvals |
MSME Lean Scheme | Yes | Consulting, up to 90% reimbursement |
PLI (Production Linked Incentive) | Indirectly | Cash paybacks for hitting targets |
This focus isn’t just red tape—it’s about fixing common weak spots. Instead of waiting for a big breakdown, a shop using the 6M approach might catch machine issues early, spot funky raw materials, or adjust how a product is checked before it ships out.
“Without a system to monitor all the 6Ms, most small businesses can’t maintain consistent quality or pass audits for government programs,” says Dr. Ajay Kumar, former advisor to India’s National Manufacturing Competitiveness Council.
If you’re looking to land a new contract, tap into incentives, or just stop money leaks on your line, linking 6M in manufacturing with government schemes is a logical step. Start keeping a simple log for each M—you’ll save hours during audits and avoid last-minute scrambles when grants open up.