Think about America’s biggest, boldest projects: the Golden Gate Bridge, the Empire State Building, and fleets of warships that sailed in two world wars. There’s one ingredient behind all these icons—steel. But have you ever wondered which American steel company came first, and how it managed to shape the nation? The answer says a lot about grit, ingenuity, and the ups and downs of creating something meant to last for centuries.
The Birth of American Steel Giants
The oldest continuously operating steel company in the U.S. wasn’t founded in the skyscraper age or by men in tailored suits. It started all the way back in the mid-1800s, an era of steam engines and horse-drawn wagons. That company is Bethlehem Steel—a name once as famous in industry circles as Ford or Rockefeller.
Bethlehem Steel began its journey in 1857, though back then, it wasn’t making huge steel beams or warships. It was called the Saucona Iron Company, set up in Bethlehem, Pennsylvania. The founders eyed the booming demand for railway rails in a growing America as their ticket. But things didn’t go smoothly. The Panic of 1857 wrecked their finances right at launch, and the company was reorganized and renamed the Bethlehem Iron Company in 1861. They didn’t ship out their first rail until 1863, an anxious, slow start for what would become an industrial powerhouse.
During the late 1800s, Bethlehem’s engineers brought a true American spirit to steelmaking. One of the star players was John Fritz—a legend in engineering. He designed what’s known as the "three-high" rolling mill, completely changing how steel and iron were made. Suddenly, it was easier and faster to turn raw ore into the sturdy rails that connected the continent. The company’s fate was sealed: it would become a trailblazer.
Competitors like Carnegie Steel (which became part of U.S. Steel in 1901) came later and grew massive, but they didn’t have the continuous line stretching all the way back to the Civil War. That legacy gave Bethlehem an edge. Soon, it shifted from just making rails to supplying steel for bridges, ships, and even skylines. Their innovative steps led to advances in steel armor plate for warships, which became crucial in both World Wars. Legends like Schwab and later Grace pumped up expansion, capitalizing on America’s growing appetite for everything steel—autos, appliances, skyscrapers. By 1918, Bethlehem was the second-largest steel producer in the country, trailing only U.S. Steel, but still the oldest with an unbroken operating history.
Want to see just how massive Bethlehem Steel’s reach was? Here’s a taste, straight from the historical numbers:
Year | Annual Steel Production (Million Tons) | Number of Employees |
---|---|---|
1900 | 0.1 | 1,500 |
1929 | 8.6 | 57,000 |
1943 (WWII) | 23 | 300,000 |
1970 (peak) | 23.4 | 150,000 |
Bethlehem lived through booms, busts, and wars. The company’s legacy isn’t just about size. It’s about pioneering, adapting, and finding a way through adversity—right from the shaky beginnings in the 1850s.
Bethlehem Steel: The Company That Built America
Ask Americans today which company built the nation’s backbone, and you’ll get a scatter of guesses. But in the late 19th and through the 20th centuries, Bethlehem Steel was everywhere. Its name popped up on everything from shipyards to bridges—and always in the thick of history.
One of Bethlehem’s first claims to fame was its armor plate—toughened steel fitted onto US Navy warships. When the Spanish-American War and then World War I rolled around, the country leaned hard on Bethlehem for its military might. The company didn’t just build battleship hulls. It rolled thick armor, cannons, and gun barrels at a scale nobody had ever seen. Workers—many immigrants—ran the foundries day and night, helping the US emerge as a global superpower.
The Golden Gate Bridge? That iconic orange span in San Francisco owes its life to Bethlehem steel. The same goes for most of New York’s skyline: the Chrysler Building, Rockefeller Center, even the Empire State Building’s beams rolled out of this company’s mills. Bethlehem also braced the George Washington Bridge and hundreds of others. Walk through any major American city, and you’re probably seeing Bethlehem’s fingerprints everywhere.
World War II was the company’s wildest stretch. Bethlehem’s shipyards turned out nearly 1,100 ships for the war effort, producing a new vessel every two weeks on average. During its prime, Bethlehem Steel was the nation’s second-largest steelmaker and one of its largest private employers. Its Bethlehem and Sparrows Point plants ran practically nonstop, setting massive production records year after year.
Bethlehem didn’t just mass-produce steel. It drove innovations that made work easier, safer, and cheaper for everyone: rolling mills, new alloys, safer methods for welding, and ways of preventing corrosion (which meant those bridges and ships lasted much longer against the elements). Thanks to its efforts, steel became affordable for everyday Americans—showing up in cars, fridges, even toasters. The country’s leap into widespread home construction after WWII? It was possible thanks in large part to readily available, strong, and reliable Bethlehem steel.
The culture forged in Bethlehem’s mills radiated nationwide. The company was famous for its tight-knit labor force and communities of workers in Pennsylvania, Maryland, and California. Kids and grandkids of steelworkers kept the tradition alive, priding themselves on being the backbone of America’s growth.
This company’s story isn’t just about metal. It’s tied tightly to American spirit—the sense that anything can be built if you have the right tools and stubborn will. For a good chunk of US industrial history, Bethlehem Steel was that tool.
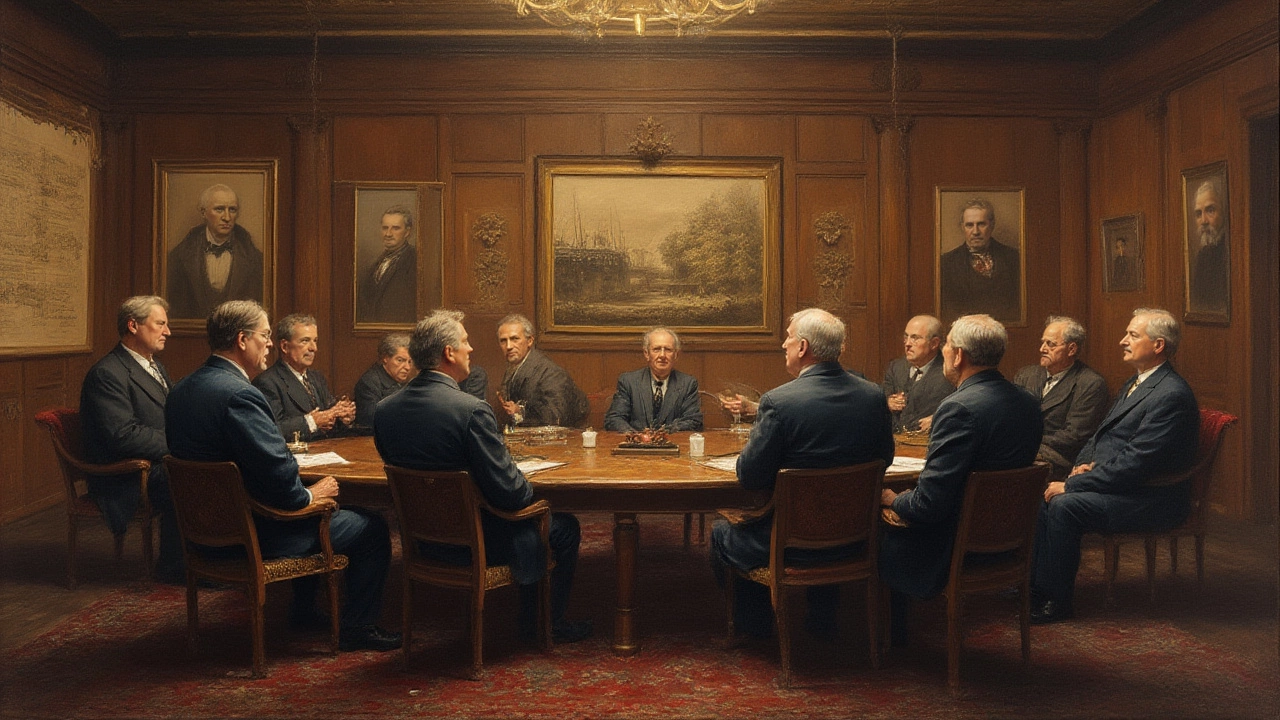
The Enduring Impact of America’s Oldest Steel Company
Steel isn’t just an industrial material—it’s a symbol for strength and progress. And Bethlehem Steel’s impact didn’t fade with the factories. Even after the mills cooled and the furnaces went cold, the company’s legacy stuck around. Whether you’re driving across the Verrazzano-Narrows Bridge, walking under the St. Louis Gateway Arch, or checking out massive ships in San Francisco Bay, you’re seeing the bones of America as Bethlehem helped build them.
Bethlehem’s approach to working with architects, engineers, and city planners changed how the country grew. Instead of making just “one size fits all” beams, Bethlehem became famous for custom steel solutions. A new skyscraper going up? The company would design special girders and trusses to fit. This attitude turned boring ironworks into creative partners—helping the skyline of Chicago, New York, and LA take shape in ways people hadn’t imagined possible a generation earlier.
Steel also pushed innovation outside just city buildings. Farmers depended on steel ploughs and storage silos. The auto industry boomed thanks to lighter, tougher steel parts. Even everyday gadgets like file cabinets drew from Bethlehem’s advances in cold-rolled sheet steel. Companies across the country copied or sourced from Bethlehem’s manufacturing process—it rippled out everywhere, setting new standards for quality and efficiency.
Let’s not pretend it was all shiny. The decline started in the 1970s and ‘80s. Pressure from cheaper imported steel, changing environmental laws, and new technology made it hard to keep up. Workers at facilities from Pennsylvania to Baltimore watched as thousands lost their jobs. The hit was sharp—the town of Bethlehem, once lively and prosperous, faded as the company announced bankruptcy in 2001. But the old steel stacks are still standing, now part of a revitalized arts and entertainment district, showing how old industry can find a new role while remembering its roots.
Bethlehem’s story is a reminder that industry shapes more than just economies—it defines regions, cultures, and even the look of a nation. As environmental movements and green tech take center stage, the ghost of Bethlehem Steel is still here, pushing today’s companies to innovate with the same bold, creative energy that marked its earliest days.
Interesting Facts and Little-Known Trivia About Early US Steelmaking
Curious about those wild early days of American steel? Here’s a look at what made Bethlehem and its rivals stand out—and some under-the-radar ideas that changed the whole game.
- Bethlehem Steel was the first US company to roll wide-flange structural shapes—critical for making skyscrapers a reality in the early 20th century. Before this, tall buildings were much harder (and riskier) to build.
- The company paid Thomas Edison to invent better lighting for their plants—so workers could pour molten steel 24/7, no matter the hour or weather.
- Bethlehem’s Blast Furnace “C” is one of the oldest still-standing in the U.S., a relic you can see if you visit SteelStacks (the arts complex built on the old site).
- The phrase "The Steel" became shorthand for the company—not just in Pennsylvania but among shipbuilders, architects, and politicians nationwide.
- During WWII, Bethlehem produced more ships than any other company—helping turn the tide, especially in the Atlantic.
- Steelworker families in Bethlehem and Sparrows Point, Maryland, often passed jobs down for generations—a sort of steel “royalty” in industrial towns.
- Bethlehem’s foundry poured the original castings for the mighty Hoover Dam’s intake towers—literally holding back the Colorado River.
Love quirky tips? If you’re fascinated by industrial history, the National Museum of Industrial History in Bethlehem (built on an old Bethlehem Steel site) is the place. You’ll see not only photos and blueprints but the massive tools and machinery that made modern America possible. It’s surprisingly interactive—think giant gears you can actually crank. Bring kids, or just your own inner science geek.
Want to know if steel you’re looking at in an old building or rail is from Bethlehem? Check for markings: "Bethlehem PA" or a distinctive "BETH." Many beams were stamped to show proud American craftsmanship—an unexpected kind of graffiti that survived hundreds of years.
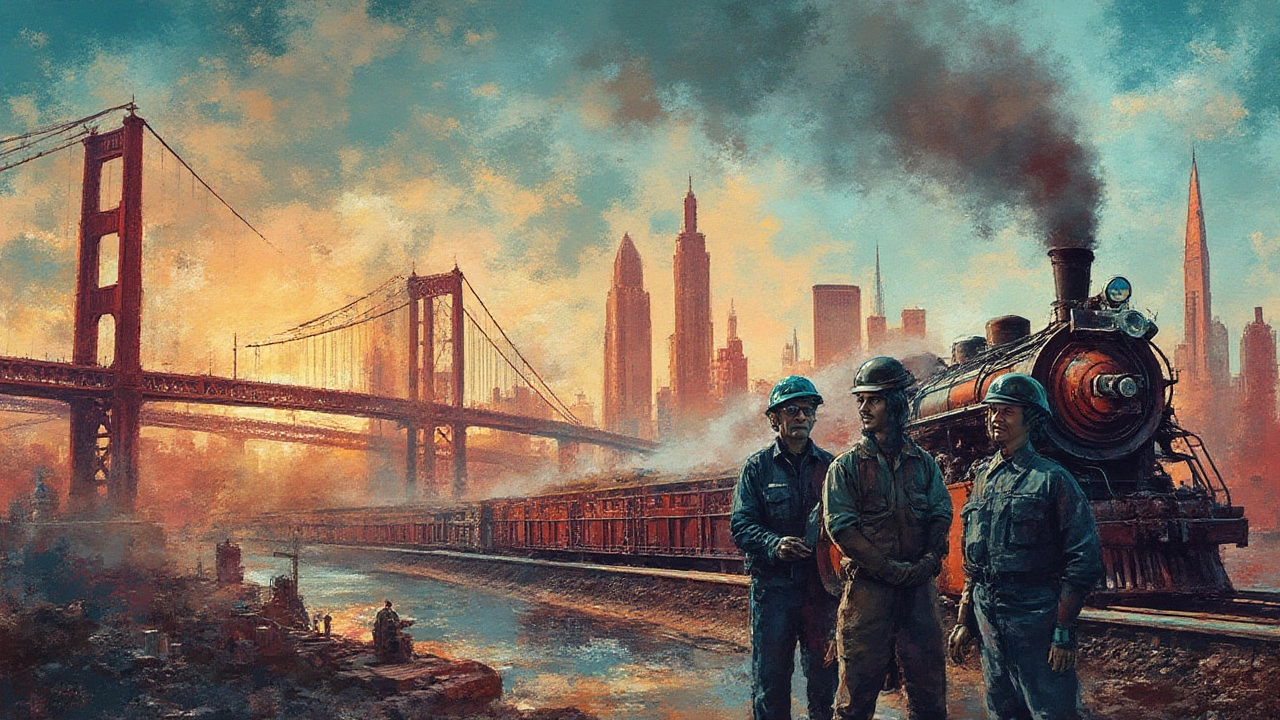
The Legacy and Lessons of Bethlehem Steel for New Generations
So what does Bethlehem Steel’s story mean now, when the world is turning to renewable energy, digital everything, and automation? The lessons go way beyond nostalgia.
First—innovation outlasts tough times. Bethlehem managed over a century of business because it stayed ahead. They didn’t settle for old methods; if there was a new, smarter way to turn ore into products, they made or borrowed it. Even as new steelmakers entered the game—many with better equipment or lower costs—Bethlehem’s willingness to adapt helped it ride out storms you’d think would wash out any business.
Second, people matter. The communities built around the mills are proof that local economies live and die by industry. When the jobs were good, neighborhoods thrived. When the plant closed, it took real effort—and creativity—to recover. That’s true in Bethlehem, PA as much as Detroit or Pittsburgh. The value of these big plants isn’t just economic, it’s cultural. You see it in local festivals, school team names, and even local slang built around the steel life.
Third—American steel still has a story to tell. Today, smaller specialty steelmakers, innovators in recycled “green” steel, and even art installations in repurposed steel mills all trace a line back to the traditions Bethlehem started. Companies take hints from Bethlehem’s relentless focus on quality, durability, and custom work. And those old gigantic beams, sometimes repurposed for sculpture, housing, or even retro furniture, give modern builders a reason to look to the past for hard-won wisdom.
Craving a career connected to this legacy? Don’t rule out steel. The field needs people who love technology, design, and sustainability as much as they love fire and metal. Visit a plant if you ever get the chance. The smell, the sounds—nothing else feels quite so stubbornly epic and American.
The story of Bethlehem Steel is bigger than a single company. It’s about dreaming big, failing, getting back up, and never quite letting go of that wild hope that you can build something that lasts. That’s an American idea worth keeping alive.