India's industrial landscape has witnessed a substantial transformation over the years, marked by significant advancements in machinery manufacturing. Among these advancements stands a monumental testament to Indian engineering: the largest machine made in the country. This machine, an industrial giant, is not only a symbol of technological prowess but also a critical piece of infrastructure that fuels various sectors.
In this article, we'll journey through the fascinating world of machinery manufacturing in India, uncovering the story of this colossal creation. We delve into the specifics of the largest machine ever made in the nation, explore intriguing facts about its construction and operation, and assess its influence on the Indian industry. Through understanding this marvel, we gain insight into the future trajectory of India's manufacturing sector.
- India's Rise in Machinery Manufacturing
- The Largest Machine Made in India
- Interesting Facts About the Machine
- Impact on Indian Industry
India's Rise in Machinery Manufacturing
India's journey in the world of machinery manufacturing is nothing short of fascinating. Over the past few decades, the country has emerged as a leading player on the global manufacturing stage, driven by a combination of technological advancement, skilled labor, and governmental support. This transformation can be attributed to the early adopters of industrialization post-independence, who saw the potential in developing a robust machinery sector. The growth of this industry is evident in the numerous industrial complexes now scattered across the country.
Significant infrastructure development in the automotive and engineering sectors has propelled India to become one of the world's top machinery producers. With companies like Larsen & Toubro and Tata Motors at the helm, India has harnessed its rich pool of talent and resources to build everything from simple tools to mammoth manufacturing equipment. These industry giants, along with a myriad of new entrepreneurial ventures, have laid the groundwork for a thriving manufacturing ecosystem that contributes considerably to the national GDP.
According to a report by India Brand Equity Foundation, India's engineering sector is set to grow, with an expected CAGR of 24.2% by 2025, reinforcing its significant role in the global market.
The growth in this sector is also fueled by innovation and adaptation of new technologies. Companies have embraced advancements such as computer-aided design (CAD) and 3D printing, to streamline production and minimize errors. These technologies have brought about unprecedented accuracy and efficiency, aligning the Indian machinery manufacturing sector with global standards. The shift towards sustainable development and green engineering has seen companies investing in environmentally friendly technologies, such as energy-efficient machinery and waste reduction solutions, recognizing the international trend towards sustainability.
Government Initiatives and Policy Support
The Indian government has played a crucial role in bolstering this sector through policy initiatives and financial incentives. Programs like 'Make in India' and the 'National Manufacturing Policy' aim to increase the share of manufacturing in the country's GDP to 25% and create millions of jobs in the coming years. Tax breaks, ease of business reforms, and subsidies for technology adoption have significantly lowered entry barriers and encouraged small to medium enterprises (SMEs) to enter the market. This has not only increased competition but has also spurred innovation and improved quality standards across the board.
Machinery manufacturers in India have tremendously benefited from improved infrastructure and logistic networks, reducing the previously daunting supply chain challenges. The advancement of a skilled workforce through vocational training programs and partnerships with academic institutions ensures a continuous supply of adept professionals ready to meet industry demands. Such a comprehensive approach assures India's sustained rise as a dominant force in machinery manufacturing, ultimately contributing to its reputation as a manufacturing hub of the future.
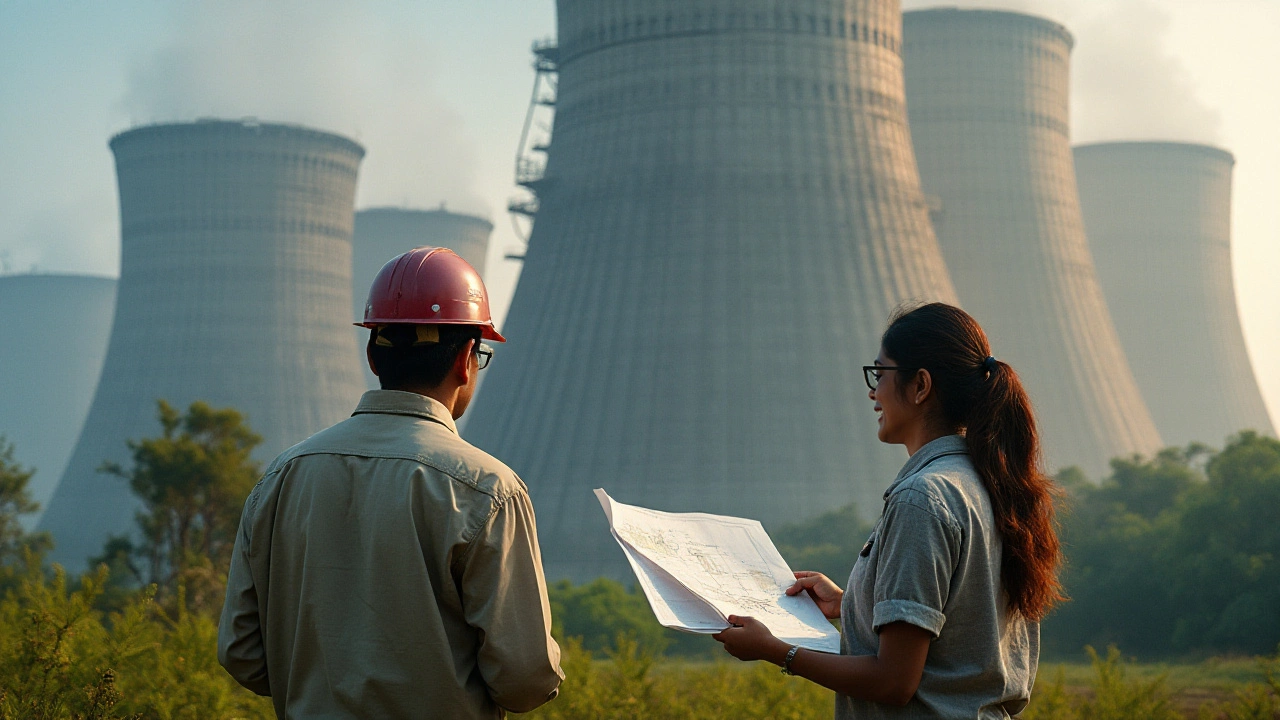
The Largest Machine Made in India
In the vast landscape of Indian engineering marvels, one machine stands out due to its sheer size and complexity - the BHEL 800 MW Supercritical Boiler. Created by Bharat Heavy Electricals Limited (BHEL), one of the top machinery manufacturers in the country, this boiler is a remarkable achievement in terms of both design and functionality. Supercritical technology is not your everyday boiler tech; it’s a cutting-edge advancement aimed at enhancing efficiency. Installed at coal-fired power plants across India, these boilers are crucial in meeting the country's ever-growing energy demands. They operate at pressures and temperatures so high that water is converted directly into steam without boiling, optimizing efficiency and reducing emissions.
The BHEL 800 MW Supercritical Boiler weighs several thousand tons and stretches over a height equivalent to a 20-storey building. Its vast network of steel tubes circulates high-pressure steam, making it a crucial component of a power plant's operation. The challenges in designing and manufacturing such a massive and complex machine are immense, requiring precision engineering and high-grade materials to withstand extreme conditions. According to BHEL’s chief engineer, "Manufacturing such substantial machinery requires innovation and the utmost care. It’s a testament to India’s capability to produce world-class equipment right here."
Let’s delve into some technical specifications: the boiler operates at a pressure of around 250 bar and at a temperature exceeding 560°C. Such specifications ensure that the power plants running with these machines are efficient in terms of fuel usage and produce fewer greenhouse gases, aligning with global environmental standards. Indian engineering prowess is exemplified in the meticulous planning and execution involved in the creation of this industrial behemoth. Projects utilizing this technology comprise more than a fifth of India’s thermal power generation capacity today. They're a testament to the blend of traditional expertise and modern technology that marks India's industrial landscape.
Beyond statistics and sheer size, the true measure of this supercritical boiler’s success is its impact on local manufacturing and related industrial sectors. Manufacturing such machines domestically reduces dependency on foreign imports and spurs the growth of related industries, providing jobs and boosting economic development. BHEL’s achievement proves that with dedication and investment in research and development, India can not only meet its domestic needs but also position itself as a significant player on the global stage. The story of the BHEL 800 MW Supercritical Boiler inspires growth for other sectors of the machinery manufacturers in India, showcasing the country’s commitment to sustainable and efficient industrial innovation.
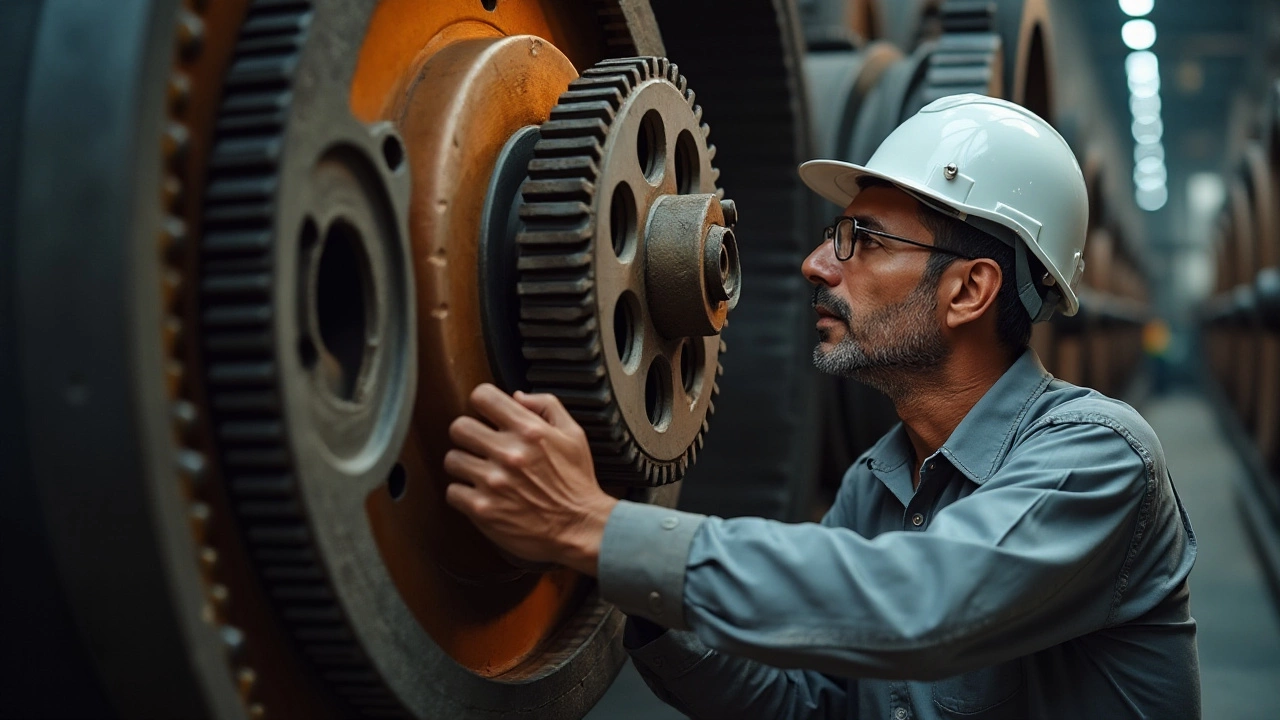
Interesting Facts About the Machine
When it comes to the topic of the largest machine made in India, it's important to start by acknowledging the sheer scale and complexity involved in its construction. This behemoth isn't just another piece of machinery, it's a testament to the engineering brilliance found within the country. Imagine the collaborative efforts of thousands of engineers and workers over several years, each contributing their expertise to ensure that every bolt was perfectly tightened, every piece of metal was seamlessly welded, and every circuit was precisely connected. The making of such a colossal machine speaks volumes of India's dedication to pushing the boundaries of industrial machinery capabilities.
A particularly notable aspect of this machine is its sheer size, which dwarfs even the largest of structures in many parts of the world. Standing tall and stretching wide, this incredible feat of engineering consists of millions of individual components, each serving a specific purpose in the larger scheme. This meticulous attention to detail is what makes the machine not only a functional masterpiece but an artistic one as well. As part of the construction process, several different modern technologies were employed, ranging from computer-simulated stress testing to ensure its stability to advanced material combinations that reduce weight while maintaining strength. The result is a machine that performs its duties with unrivaled efficiency and precision.
Equally fascinating is the machine's versatility. While one might expect such a large structure to be limited in function, this industrial marvel is anything but. It's designed to support myriad operations, from facilitating mass production in factories to assisting with precise construction projects. The adaptability of the largest machine in India ensures that it plays a vital role across various sectors, bolstering the nation’s economy and providing numerous employment opportunities. One could say that its influence extends far beyond engineering, reaching into the heart of societal progress.
Engineering Innovations and Challenges
The path to creating this largest machine in India was not devoid of challenges. Engineers were tasked with innovating around a variety of technological and practical hurdles. For instance, the machine required a custom-built transportation protocol due to its enormity, ensuring components were safely delivered to the build site. To address energy consumption, engineers incorporated state-of-the-art energy-efficient technologies that balance operational power needs with environmental concerns.
"The real achievement lies not only in its construction but in how it reshaped our approach to problem-solving and project management at such a grand scale," noted a senior project leader involved in its development.Each of these innovations highlights India’s growing capacity for technological advancement, setting the stage for future projects of even greater magnitude.
Moreover, the quest for optimal performance and durability led to the development of new engineering standards. These standards, refined and perfected during the machine’s construction, are now influencing emerging industrial machinery designs across India. And let's not forget the sustainability measures adopted in its ongoing operation. Recycling and upcycling components where feasible, along with minimizing waste generated during manufacturing processes, underscores a commitment to responsible industrial practices.
Statistics and Data
To provide some perspective, consider the volume of materials used and the scale of operations involved. Here's an overview in simpler terms that might resonate:
Element | Data |
---|---|
Total Weight | Over 30,000 tons |
Construction Duration | Approximately 5 years |
Man-hours | Million-plus |
Height | Similar to a 40-story building |
These figures help in visualizing just how substantial the project was. It also captures the commitment required to bring this monumental piece of architecture to life. Thus, as one delves into its journey, the stories of triumphs, perseverance, and innovations stand out, painting an inspiring narrative of India's path to becoming a global leader in machinery manufacturing.
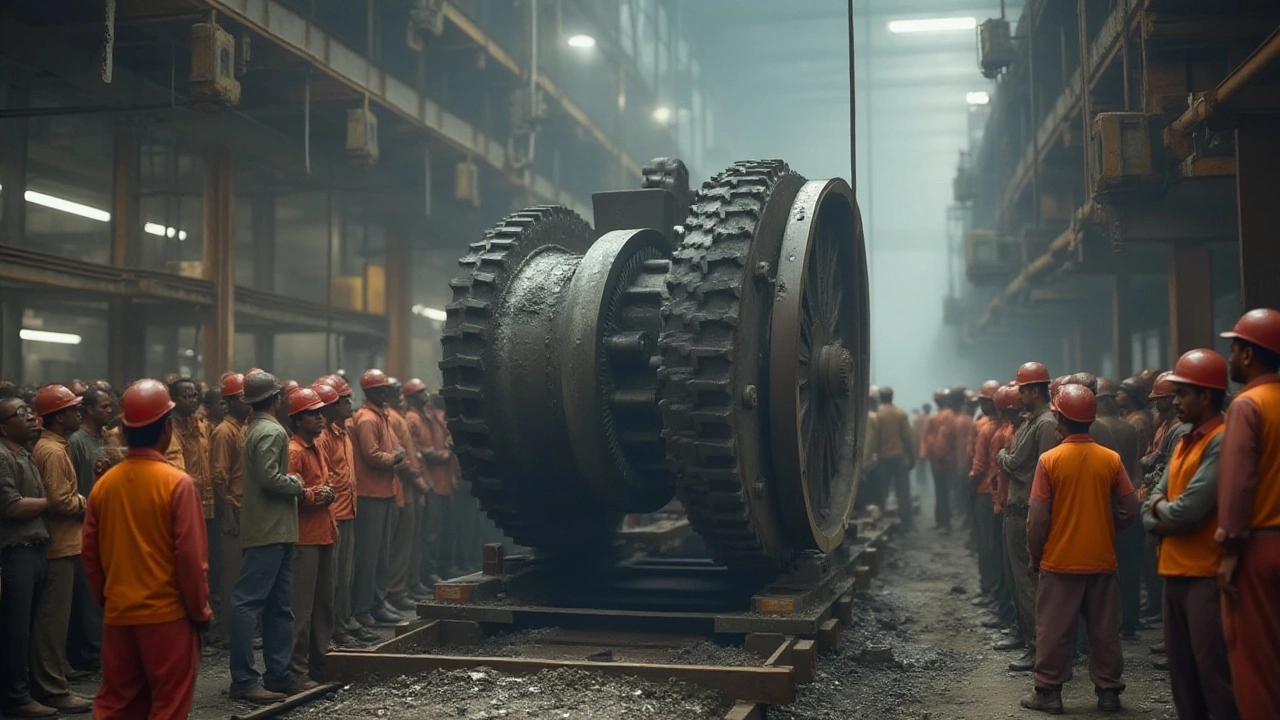
Impact on Indian Industry
The creation of the largest machine made in India has had a profound effect on multiple facets of the Indian industry. This giant of engineering is not just an achievement; it stands as a catalyst for growth across several sectors. One of the direct impacts is observed in the improvement of industrial productivity. The machine supports large-scale production, enabling factories to meet the increasing demands of both domestic and international markets. This substantial boost in production capacity allows Indian manufacturers to compete more effectively on a global scale, leading to enhanced export opportunities and strengthening the economy.
Moreover, this machinery has been pivotal in creating thousands of jobs, from the initial stages of its design and construction to its ongoing operation and maintenance. Skilled engineers, technicians, and support staff are consistently needed, which drives educational institutions to adapt their curriculums to reflect these growing industry demands. Training programs and vocational courses are expanding to cultivate a workforce capable of managing such complex machinery. This ripple effect enhances the skill set of the Indian workforce, significantly contributing to the nation's development.
Environmental considerations form another crucial impact aspect. As industries strive for greener technologies, the machinery has integrated more sustainable practices, reducing energy consumption and minimizing emissions. While the machinery itself is a beacon of innovation, it also sets the standard for sustainable manufacturing processes in India. Companies now are increasingly investing in research and development to innovate eco-friendly methods and technologies, driven by both regulatory pressures and corporate responsibility.
Notably, the machine's success has positioned India as a hub for technological innovation. Many international companies now look to India not just as a market for their products, but also as a fertile ground for collaboration and investment in high-tech, large-scale manufacturing projects. This attention fosters a dynamic environment where Indian companies can forge strategic partnerships, acquire cutting-edge technologies, and exchange invaluable expertise with global leaders.
The overall significance of this machine extends beyond immediate industrial gains. It has inspired a shift in the mindset of the Indian industry, elevating standards, efficiencies, and ambitions across the board. As stated by renowned industry expert Rahul Mukherjee, "This machine is not just engineering marvel; it's a statement of India's intent on the world stage."
The integration of such advanced technology underscores a pivotal moment in India's journey towards becoming an industrial powerhouse.The resultant effects of this development lay the groundwork for future innovations that promise to further bolster India's robust industrial landscape.