Manufacturing is an essential engine that drives the global economy. With methods ranging from age-old traditional techniques to cutting-edge technologies, manufacturing processes continue to evolve and adapt to modern demands. Each method comes with its own unique efficiencies, challenges, and environmental impacts that define the quality and sustainability of the products we rely on.
In this article, we’ll take a closer look at three major manufacturing methods that are shaping industries today. We’ll also explore how government schemes are playing a vital role in supporting and modernizing these methods to meet future challenges and goals. The interplay of innovation and regulation creates a dynamic landscape where both established companies and startups can thrive.
- Traditional Manufacturing Techniques
- Additive Manufacturing Revolution
- Advanced Manufacturing Technologies
- Government Schemes Supporting Manufacturing
- Future Prospects in Manufacturing
Traditional Manufacturing Techniques
Traditional manufacturing methods have been the cornerstone of production processes long before modern technologies reshaped the industrial landscape. At its core are processes like casting, forming, machining, and joining, each integral to the production of a vast array of goods. These methods date back hundreds, if not thousands, of years, with casting alone tracing back to the Bronze Age. Despite the influx of modern alternatives, these techniques continue to demonstrate resilience and significance in industries worldwide. Several factors contribute to their longevity, including reliability, well-understood mechanisms, and the ability to produce high-quality products. They are often employed in sectors where precision and durability are paramount, such as in aerospace or automotive industries.
The artistry and skill required in traditional methods cannot be overstated. Workers with decades of experience can produce items of remarkable craftsmanship. For example, machining remains essential for creating parts with tight tolerances, a critical requirement in sectors demanding precision engineering. While high-tech machinery supports these processes today, the foundational skills remain rooted in practices honed over generations. These methods also emphasize the importance of material usage and waste minimization, often seeking the most out of every piece of raw material, which aligns with sustainable manufacturing goals.
A fascinating aspect of traditional manufacturing is its adaptability. Despite the emergence of digital manufacturing avenues, these techniques have not only persisted but also evolved. Historically, they relied heavily on manual labor; however, the incorporation of technology has allowed for greater precision and efficiency. Take the automotive industry, which still employs stamping and welding processes, albeit enhanced by robotics and advanced control systems. This blend of old and new highlights the adaptability of traditional methods to modern demands, fulfilling roles where newer, untested techniques might hesitate. Indeed, according to a report by Deloitte, a significant percentage of manufacturers stated that balancing traditional with modern methods allows them to meet increasingly diverse consumer demands effectively.
Traditional techniques have been instrumental in shaping modern-day economies. Countries like Germany, known for their engineering prowess, have long championed high-quality craftsmanship rooted in traditional manufacturing. This has not only propelled their industries but also positioned them as leaders on the global stage. Skilled labor here is considered an asset, with continuous training ensuring that these age-old practices do not fade into obscurity. Manufacturing process methodologies are continually refined, blending tradition with high-tech innovations to maintain competitiveness. This synthesis exemplifies how foundational methods and government initiatives can lead to sustainable growth.
The sustainability aspect of traditional manufacturing cannot be overlooked either. These practices have always been about making the most of available resources, reducing waste wherever possible. With the growing emphasis on environmental conservation, industries worldwide revisit traditional methods with a fresh perspective on sustainability. Casting and forging, for example, often use recyclable materials, contributing to a circular economy where waste is minimal, and production efficiency is high. Industries recognize that the reduced energy consumption and lower carbon footprint associated with traditional methods can provide a competitive edge in a market increasingly concerned with environmental impact.
Additive Manufacturing Revolution
Additive Manufacturing, often referred to synonymously with 3D printing, marks a transformative phase in the *manufacturing process*. Unlike traditional methods that typically involve cutting away material to create a product, additive manufacturing builds items from the bottom up, layer by layer. This revolutionary technique has sparked excitement across industries, bringing about significant changes in how products are designed, manufactured, and distributed. It enables unparalleled design flexibility, allowing for the creation of complex geometries and structures that were once impossible to achieve through conventional methods. This approach not only accelerates development cycles but also dramatically reduces the waste associated with subtractive manufacturing techniques, aligning well with modern sustainability goals.
The impact of additive manufacturing is profound in various sectors, from aerospace to healthcare. In the aerospace industry, for example, components are crafted with precision, resulting in parts that are lighter yet stronger, enhancing fuel efficiency and performance. Meanwhile, in healthcare, the creation of custom prosthetics and implants tailored to individual patients’ anatomies is revolutionizing treatment outcomes. The ability to produce small to medium batches on-demand without necessitating expensive tooling changes is a game-changer, especially for startups and smaller firms, leveling the playing field against established giants.
A notable aspect of the additive manufacturing boom is its democratization of production. Accessible machines, open-source software, and diverse material choices mean that even small businesses or individual designers can translate ideas into tangible products without restrictive barriers. As Dr. Jennifer Lewis from Harvard University poignantly observed,
"The promise of additive manufacturing lies in its power to dissolve traditional boundaries. It allows anyone, anywhere, the ability to invent and innovate."This accessibility nurtures innovation ecosystems, fostering collaborations across the globe as shared knowledge becomes a currency of industrial advancement.
While additive manufacturing is burgeoning with promise, it’s not without its challenges. Material limitations remain a significant hurdle, as not every material, especially metals, can be easily adapted to 3D printing. The quality and durability of printed parts, particularly under stress or high temperatures, continue to be scrutinized. Moreover, the standardization of processes and the establishment of regulatory frameworks are vital for ensuring uniform safety and performance benchmarks across industries.
Governments worldwide recognize these challenges and are stepping up with support. Various government schemes aim to fuel the development and adoption of additive manufacturing technologies. From funding research and development to offering tax incentives for companies that invest in these technologies, the support structure is robust and growing. Notably, Australia has been proactive, launching initiatives to integrate additive manufacturing into its broader industrial strategy, ensuring economic resilience and technological competitiveness in the global arena.
As technology progresses and more industries harness its potential, additive manufacturing stands poised to redefine what is possible within production methods. The shift from mass production to mass customization represents the dawn of a new industrial era, promising a future where personalization and efficiency walk hand in hand. The journey of additive manufacturing is still unfolding, and its potential impact on both industry and society is as boundless as the creativity it inspires.
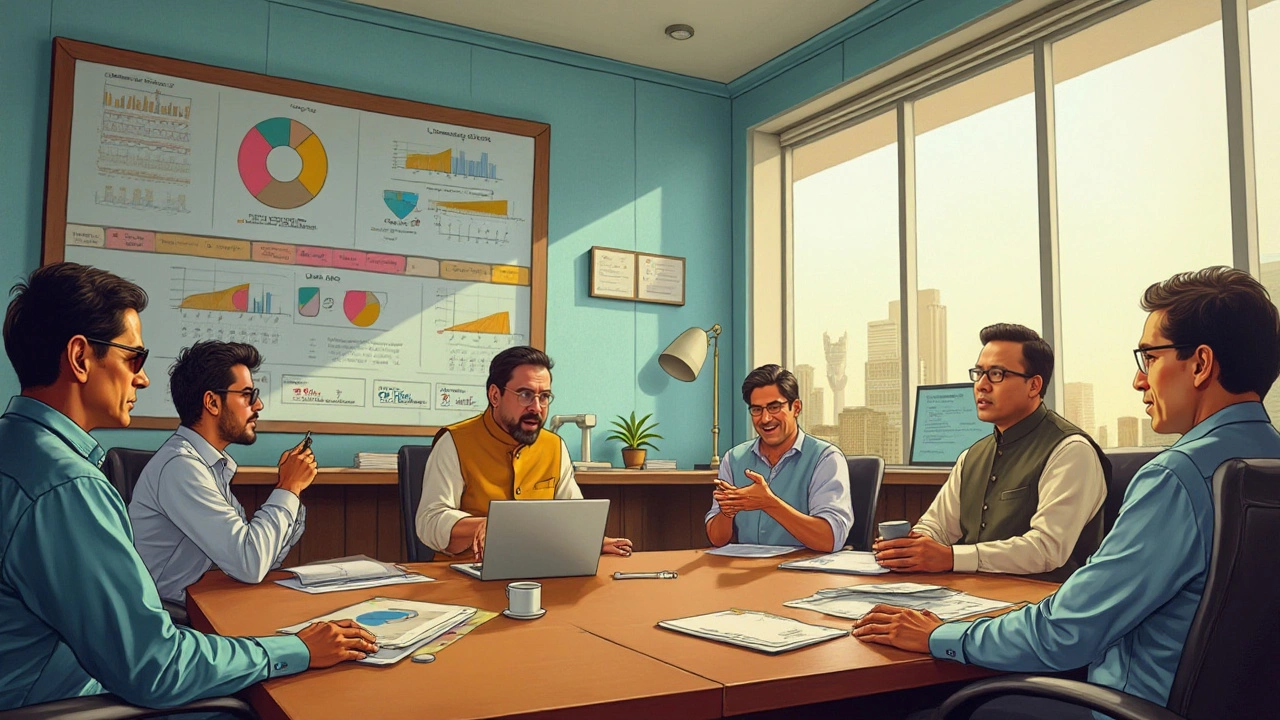
Advanced Manufacturing Technologies
Advanced Manufacturing Technologies have transformed the landscape of the manufacturing process as we know it, bridging the gap between traditional craftsmanship and modern innovation. These technologies represent a series of ground-breaking developments that have fundamentally redefined efficiency and productivity. At the heart of these advancements lies automation, robotics, and smart technologies, often referred to as Industry 4.0, which prioritize connectivity, decision-making, and minimal human intervention. Traditionally, a production line depended heavily on human labor; however, with the rise of automation, there's been a seismic shift towards precise, repeatable processes that can run indefinitely without fatigue.
Manufacturers are increasingly adopting cyber-physical systems that seamlessly integrate computing, networking, and physical processes. This integration means that machines can communicate with each other autonomously, optimizing production schedules and reducing waste. An impressive illustration of this is predictive maintenance, where machines flag potential failures before they occur, thus preventing downtime and extra costs. Industrial techniques are now being revolutionized by these smart technologies, as AI and machine learning algorithms help manufacturers make data-driven decisions.
Another fascinating facet of advanced manufacturing is its role in enhancing sustainability. As governments worldwide set stringent regulations to mitigate environmental impacts, advanced manufacturing technologies offer viable solutions. Digital twins, a concept where virtual replicas of physical systems are used for simulations, help in optimizing energy usage and reducing emission footprints. For instance, a study by the World Economic Forum highlighted that factories employing digital twin technology saw a 10% to 30% reduction in energy consumption.
"As we integrate smart manufacturing, we're not just enhancing productivity; we're also ensuring our practices are aligned with sustainable development goals," said Klaus Schwab, Founder of the World Economic Forum.
The advancements do not stop at predictive technologies and sustainability features. Add to this list, customization and flexibility. Modern-day demands lean heavily towards customized products tailored to individual tastes. Advanced manufacturing technologies cater to this need with high agility, allowing for quick tweaks and changes in production without major overhauls. This flexibility creates a competitive edge, allowing products to hit the market faster and in line with current trends. Small to medium enterprises especially benefit because these technologies democratize the landscape, leveling the playing field on which they compete with giants.
When discussing advanced manufacturing, it is important to mention the role of collaborative robots, known as cobots. Unlike traditional robots that operate within cages away from humans, cobots work collaboratively alongside human workers, enhancing safety and efficiency. Operating with sophisticated sensors and AI capabilities, cobots are efficient in performing repetitive tasks with precision, while human workers can focus on more complex aspects of production. This synergy between man and machine is a progressive step towards increasing throughput while maintaining high quality. Through this collaboration, the production methods are being pushed to their new evolutionary stages.
The infinite possibilities offered by advanced manufacturing technologies have ignited a new era of customization, enhanced efficiency, and unwavering sustainability. The path forward is one where continued collaboration between human intelligence and machine precision charts a course toward ineffable innovations, ultimately benefiting global industries. As these technologies continue to advance at a rapid pace, staying informed and adaptable will ensure businesses keep up with the dynamic shifts shaping the manufacturing landscape of tomorrow.
Government Schemes Supporting Manufacturing
The realm of manufacturing isn't just about ingenious techniques or revolutionary technologies; it’s also bolstered by an array of government schemes designed to support this critical sector. These initiatives can be seen as the unseen hands that provide the necessary infrastructure, financial backing, and policy frameworks to ensure manufacturing thrives and keeps pace with evolving global standards. Whether aiding traditional industries or nurturing high-tech startups, government bodies play a key role in shaping a sustainable and productive future.
One of the prime examples of government-led interventions is the much-praised 'Made in India' campaign launched by the Indian government. It aims to transform India into a global hub of manufacturing by encouraging both multinational and national companies to manufacture their products within India. This scheme not only boosts domestic manufacturing processes but also significantly enhances employment rates and technological development. The key driver of this initiative lies in improving the business environment through ease of doing business, tax relaxations, and dedicated sectors for streamlined production.
In Australia, similar efforts are underway with initiatives like the Modern Manufacturing Strategy, which provides funding and support to bolster local industries. This scheme is tailored to help manufacturers upgrade capabilities, invest in new technologies, and diversify their operations to ensure long-term sustainability. A significant focus is placed on sectors such as minerals, food, and beverage processing, which are crucial to the Australian economy. This strategy not only strengthens infrastructure but also aligns with broader environmental goals, leveraging sustainable methods in the production methods.
To encourage the adaptation of emerging technologies, grants and tax incentives are frequently offered. The Research and Development Tax Incentive in countries like Canada allows manufacturers to recover up to 60% of their R&D costs, encouraging them to innovate continually. According to a report from the Department of Innovation, 80% of Canadian manufacturers that utilize this incentive saw measurable improvements in operational efficiency and product quality, emphasizing its impact.
"Innovation and creativity are the foundations of manufacturing," says a leading industry expert. "Government support is crucial in turning conceptual ideas into market realities."
Coupled with these, there are also international collaborative efforts aimed at supporting industrial techniques globally. Programs like Horizon Europe provide funding to collaborative projects involving multiple countries, encouraging standardization across borders and the sharing of cutting-edge practices. By nurturing cross-border collaboration, these programmes not only enhance innovation but also help in addressing global challenges by integrating diverse technological solutions.
For manufacturers eager to engage with these schemes, it's key to stay informed about the application processes, requirements, and timelines that each scheme involves. Governments often offer informational sessions, workshops, and consultancy services to guide businesses through these processes smoothly. This structured guidance helps companies not just to avail themselves of immediate benefits but also to align their long-term goals with national and international manufacturing standards.
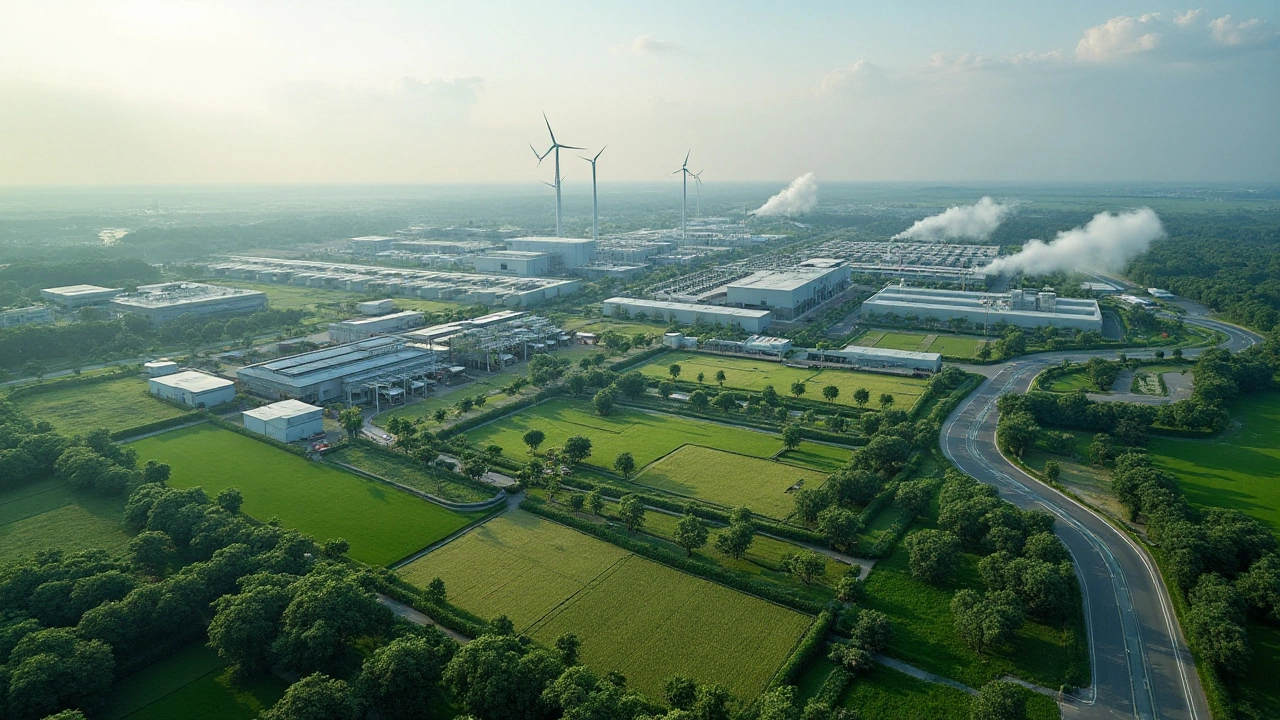
Future Prospects in Manufacturing
As we step into an era laden with technological innovation, the future of manufacturing seems positioned for a radical shift. This transformation is characterized by a seamless blend of traditional techniques with avant-garde technologies, creating hybrid models that enhance efficiency without sacrificing quality. One exciting prospect is the increased integration of additive manufacturing into mainstream production processes. With capabilities expanding beyond prototyping, this method is set to revolutionize how industries produce complex and customizable components at scale, reducing waste and cost dramatically. As the technology matures, its adoption across sectors such as automotive, aerospace, and healthcare promises to redefine supply chains and reduce environmental footprints.
Looking ahead, data-driven manufacturing—sometimes referred to as smart manufacturing—is also gaining traction. With IoT devices and AI becoming ubiquitous, manufacturing processes are becoming more intelligent. Machines are now equipped with sensors that facilitate real-time monitoring and predictive maintenance, reducing downtime significantly. These systems utilize vast amounts of data to enhance decision-making processes, thus optimizing production and improving product quality. As we advance, the integration of machine learning into manufacturing processes will only deepen, empowering industries to operate with unmatched efficiency and precision.
"The factory of the future will be a place where innovation is not just enabled but expanded," states John Doe, a noted industrial technology analyst. "We will see a scenario where human skill and technological superiority collaborate for unprecedented breakthroughs."
Environmental sustainability is another focal point for future manufacturing. Governments worldwide are increasingly implementing stringent policies and offering incentives to reduce industrial carbon footprints. This shift is fostering advancements in green manufacturing practices, including the use of renewable energy sources and biodegradable materials, aligning industrial growth with ecological responsibility. The adoption of circular economy principles aims at extending product lifecycle and recycling materials, which is something industries are gearing up to embrace fully.
Lastly, it's essential to note how government initiatives are supporting these transformative changes. Many governments are rolling out initiatives and grants to foster innovation in manufacturing processes. These schemes are aimed at encouraging industries to adopt high-tech manufacturing methods while ensuring jobs and economic activities aren't adversely affected. Through funds and partnerships, there's notable momentum in developing industrial hubs that focus on the synergy between traditional and modern manufacturing techniques.
Potential Challenges and Opportunities
Despite being on the brink of a manufacturing renaissance, challenges persist. Skill gaps in the workforce, as new technologies emerge, threaten the smooth adoption of advanced manufacturing processes. Bridging these skill gaps requires targeted education and training programs to equip workers with necessary skills. On the flip side, this also presents an opportunity for job creation in areas like technology maintenance and system integration, essential for supporting modern manufacturing infrastructures.
In conclusion, the future of manufacturing holds significant promise. With continuous technological advances, a commitment to sustainability, and strong government support, the possibilities for innovation and efficiency are limitless. As industries embrace these changes, they inch closer to not only fulfilling the demands of today but also preparing for the unforeseen needs of tomorrow.