We all use plastic every day, but have you ever wondered about the actual cost of making it? Spoiler alert: it's not as straightforward as you might think. Making plastic involves several cost factors that go beyond just the raw materials. It's a mix of ingredients, machinery, and processes that determine the final price tag.
First off, let's talk materials. The basic building block for plastic is crude oil or natural gas, both of which have prices that fluctuate with global markets. When oil prices spike, it ripples right through to plastic production, making the final product more expensive.
But hold up, it's not just about oil. Energy costs are another biggie. Think about the energy it takes to run those massive machines that mold and shape plastic. That electricity bill isn't small, especially when green energy policies come into play.
Then there's the environmental side. As folks get more eco-conscious, they're not just looking at price but also at the footprint of plastic products. Companies are now investing in biodegradable options and recycling processes, which can save the planet but also alter the cost dynamics.
Whether you're in the business or just curious, understanding how these factors tug at the purse strings is key. As tech advances, we're seeing some cool changes that could make plastic production not just cheaper, but also smarter and greener. Let's dive deeper into how all this shakes out in the real world of plastic manufacturing.
- The Basics of Plastic Production
- Raw Material Costs
- Energy and Equipment Expenses
- Environmental Costs and Innovations
- The Future of Plastic Manufacturing
The Basics of Plastic Production
Alright, let's break down how plastic comes to be. The whole process kicks off with raw materials, mainly crude oil and natural gas. These are rich in carbon, which is a key building block for plastics. Think of them like the flour in a cake recipe—nothing happens without them.
The first major step is called polymerization, a fancy term for a chemical reaction that turns small molecules into long chains, or polymers. These polymers are the base for all plastics. There are two common types of polymerization: addition and condensation.
Addition polymerization involves the chain reaction of smaller molecules called monomers, creating polymers without any byproducts. An example is polyethylene, found in plastic bags. Condensation polymerization, on the other hand, involves combining monomers to form polymers with a small molecule byproduct like water. This is how some Nylon types are created.
Once polymers are formed, they need to be shaped and solidified into products. This happens through processes like extrusion, injection molding, and blow molding. Each method serves different purposes, from making pipes to forming solid plastic parts.
And here's a techy bit: the machinery involved in plastic production isn't cheap. Extruders, molds, and other equipment can come with a hefty price tag, playing a big role in the overall manufacturing cost.
Plastic production is a massive industry, and understanding this basic overview gives a peek into how involved it really is. Still, it's this intricate dance of chemistry and machinery that keeps the plastic world spinning and our modern lives running smoothly.
Raw Material Costs
Alright, let's dive into what makes up a big chunk of your plastic bill: raw materials. At the heart of most plastics is crude oil or natural gas, acting as the primary feedstock. Because these materials are extracted from the earth, their prices are highly dependent on global economic conditions. When oil prices shoot up because of geopolitical tensions or supply shortages, expect the cost of plastic production to follow suit.
For instance, about 4% of the world's oil production goes directly into making plastics, and another 4% is used to fuel the manufacturing process. The price of Brent crude, a major trading classification, can fluctuate greatly. As of early 2025, oil has seen prices ranging from $60 to $90 per barrel. This variability directly impacts what companies pay for their plastic base materials.
Furthermore, not all plastics are created equal in their raw material needs. Different types of plastics, like polyethylene (PE), polyvinyl chloride (PVC), and polystyrene (PS), come with their own specific recipes. For example, PE, one of the most common plastics, is pretty dependent on ethylene derived from oil or natural gas. When these base materials get pricey, so does PE.
Here’s another fun fact: the shift towards bioplastics is changing the raw material game. Instead of oil, bioplastics use renewable sources like corn starch or sugarcane. Though an environmentally friendly choice, these alternatives tend to come at a higher cost due to shorter supply chains and less established production processes.
It's not just about what materials you use, but also how stable their supply is. Prices can fluctuate based on regional production bottlenecks or trade policies. Imagine the chaos when key suppliers suddenly can't export because of new tariffs or embargoes. Suppliers are constantly juggling these factors, trying to secure stable and cost-effective sources to stay competitive in the plastic industry.
When planning production budgets, companies often consider both immediate raw material costs and long-term trends. This includes watching forecasts on oil prices, geopolitical stability, and advances in alternative materials research. By understanding these trends, companies can better navigate the complex waters of plastic manufacturing costs.
Year | Average Oil Price (USD/barrel) | Impact on Plastic Cost |
---|---|---|
2022 | $79 | High |
2023 | $68 | Moderate |
2024 | $75 | High |
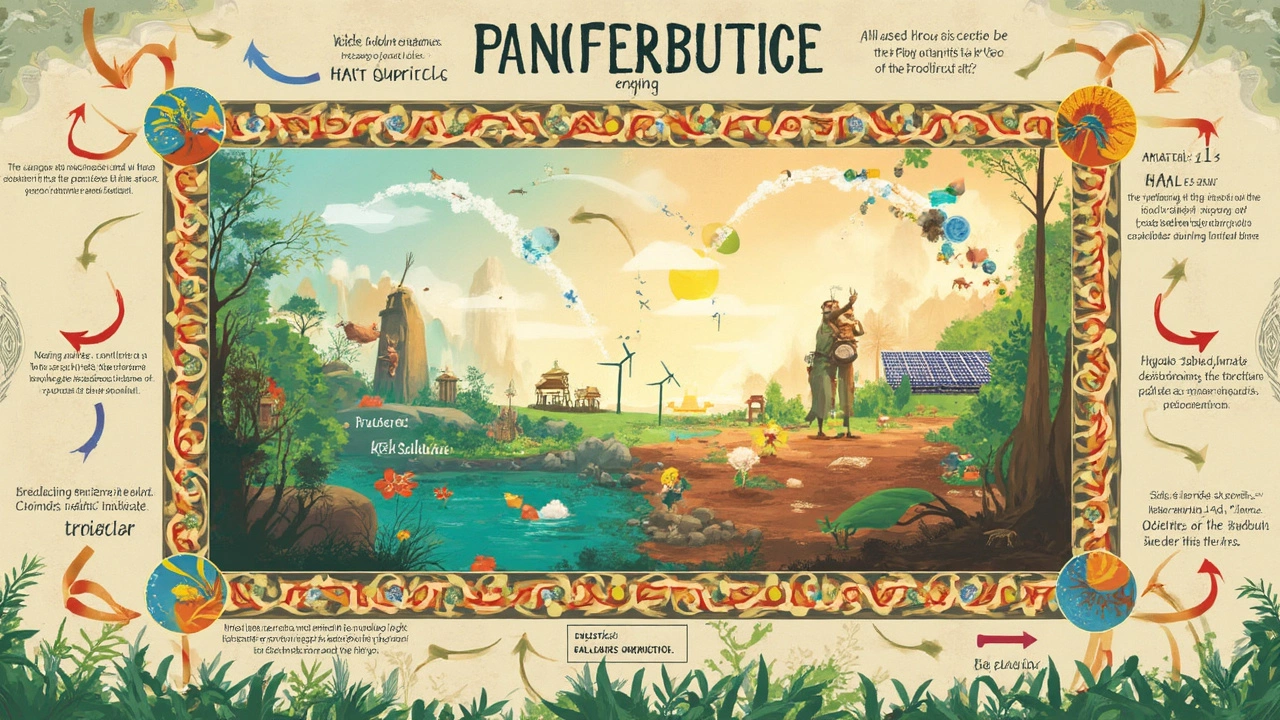
Energy and Equipment Expenses
Diving into the nitty-gritty of plastic production, energy and equipment costs are like the hidden gears of a complex machine. These elements play a crucial role in determining the overall expense of turning raw materials into the plastic products we use daily.
First up, let’s talk about energy. Manufacturing plastic requires substantial heat and power. The process involves heating raw materials to very high temperatures, which takes a lot of electricity. As you might guess, this isn't cheap. If a plastic manufacturing company is in a region where energy prices are on the rise, these costs can quickly add up, impacting the final price of plastic products.
Then there’s the equipment. Those giant machines that mold and fabricate the plastics are not only expensive to buy but also to maintain. We're talking about injection molding machines, extruders, blow molders, and more. Keeping these smoothly humming along requires regular upkeep and sometimes, expensive parts. Plus, newer, more efficient models come with hefty price tags, so companies must balance between operational costs now and potential savings down the line.
Technology is a big factor here. Innovative equipment designed to save energy can reduce costs significantly in the long run. For example, using electric rather than hydraulic machines can cut down energy consumption, which in turn reduces the carbon footprint—a big win in today’s eco-conscious market.
Some forward-thinking companies even leverage renewable energy sources. Imagine a solar-powered factory. While the initial setup can be costly, over time, it could save heaps on energy bills while also appealing to environmentally-minded consumers.
Expense Type | Impact on Cost |
---|---|
Electricity | High |
Equipment Maintenance | Medium to High |
New Technology Investment | High Initially |
Renewable Energy Use | Low Over Time |
Savvy businesses optimize these expenses by investing in energy-efficient technologies and prioritizing regular maintenance to extend equipment life. This not only keeps costs manageable but also enhances production efficiency, setting a solid foundation for competing in the tough world of plastic manufacturing.
Environmental Costs and Innovations
The environmental impact of plastic has become a hot topic, and rightly so. Everyone's buzzing about sustainability, and this buzz is affecting how plastics are made. When people think of plastic production, they often consider the pollution it causes, both during production and once the products are discarded. This pollution isn't just bad for the planet; it's becoming costly for manufacturers facing pressure to clean up their act.
So, how are companies adapting? Let's break it down. Many are investing in greener technologies and materials to reduce that environmental footprint. This includes developing biodegradable plastics, which, unlike the traditional stuff, breaks down more easily and is less harmful to ecosystems.
And that's not all. Recycling is getting a major upgrade. Advanced sorting technologies and chemical recycling methods are being used to turn used plastics into virtually brand-new materials. It costs less energy, and crucially, it keeps more plastic out of landfills. But this isn't quite as cheap as using virgin materials, which is why innovation is key.
- Biodegradable Plastics: Materials that break down faster and more safely, potentially reducing disposal costs and environmental penalties.
- Advanced Recycling: Ideas like chemical recycling or improved sorting that reclaim more plastic and lower waste.
- Carbon Footprint Reduction: Initiatives to minimize greenhouse gas emissions during manufacturing.
Some companies are even introducing energy-efficient processes, like using renewable energy sources to power production facilities. This not only cuts emissions but also can reduce energy costs over time, making the production process more sustainable and potentially cheaper.
For those of you numbers folks, consider this fun fact: using recycled plastics can cut energy usage by about 66% compared to the process of making new plastic from raw materials. Imagine the savings across tons of plastic production. It's these kinds of innovations that are steering the ship toward a more sustainable future, showing that what's good for the planet can be good for business too.
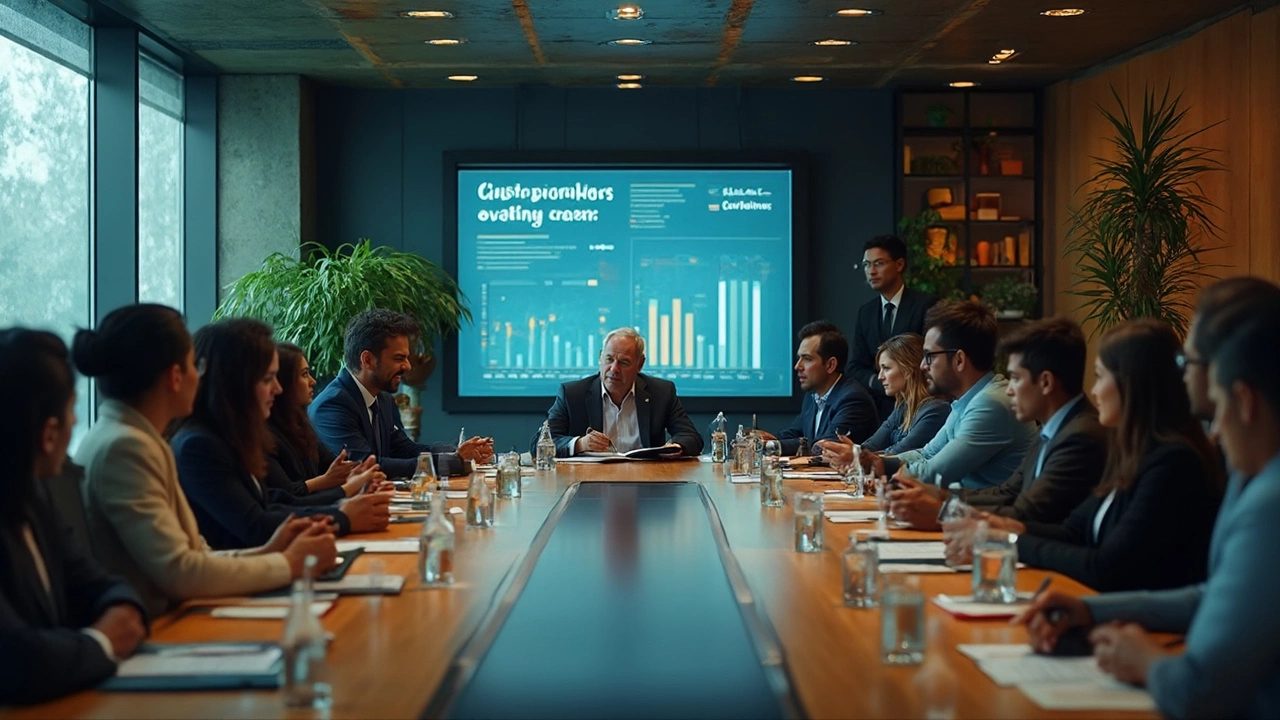
The Future of Plastic Manufacturing
So, what's next for plastic? We're stepping into an era where cutting-edge tech and sustainability are reshaping how plastic is made. It's not just about churning out more plastic; it's about making it smarter and greener. That means using tech like AI to optimize production processes, reduce waste, and even lower costs.
A big trend is the move towards more sustainable materials. Companies are exploring alternatives to traditional oil-based plastics. Bio-based plastics, made from corn or sugarcane, are gaining traction. Not only are these better for the environment, but they can also attract eco-conscious consumers, which might be a win-win.
But here's the kicker: recycling is getting a major upgrade, thanks to tech advances. New chemical recycling methods can break down plastics into their fundamental components, making them like new again. According to a report by the World Economic Forum, "By 2030, we could see plastic recycling rates double, thanks to these innovations."
"Our ability to innovate in recycling technology is crucial to meeting sustainability goals," says Dr. Laura Thompson, a leading researcher in plastic technology.
There's also a shift in how the industry addresses energy use. Solar energy and other renewable sources are increasingly being used to power production facilities. This shift not only cuts down on carbon emissions but also helps keep energy costs in check, making the production process more resilient to market changes.
Overall, the future of plastic production looks like a balancing act between cost, efficiency, and environmental impact. Expect more breakthroughs in recycling tech, an increase in sustainable practices, and a push towards minimizing the environmental footprint. In the long run, these changes could make plastic a more sustainable choice, without breaking the bank.