Those mile-long trains packed with shimmering new cars didn’t appear out of magic. Somewhere, there’s a behemoth plant that spits out vehicles at a speed that would even make Henry Ford dizzy. India’s appetite for cars isn’t slowing down, and behind it stands a factory on such a massive scale—it regularly beats international competitors. Yet, most people have never stepped inside, let alone wrapped their heads around what really goes on there.
If you guessed Gurugram, you’re stuck in the past. The largest car plant in India is in Gujarat, operated by Suzuki Motor Gujarat Private Limited (often abbreviated as SMG). This isn’t just a big shed with assembly lines; it’s a powerhouse churning out almost a million cars every year, dwarfing everything else on the subcontinent. SMG isn’t a flashy brand in itself—it builds cars for Maruti Suzuki, the familiar household name. The plant’s story reads like a blueprint for the modern Indian auto industry. It feeds not just India, but markets from Africa to Latin America, sending out carloads every single day.
The Birth and Juggernaut Scale of Suzuki Motor Gujarat
Gujarat’s automobile adventure wasn’t always a sure bet. When Suzuki Motor Corporation announced its plans back in 2014, plenty of experts doubted whether anyone could manage such scale all the way in Hansalpur, a quiet region near Ahmedabad. But when the first car—a Baleno hatchback—rolled off the line in February 2017, things moved fast. Fast forward to today: Suzuki Motor Gujarat has three massive production lines, an engine plant, and a sprawling supplier park.
The numbers tell the real story. Current annual production hovers close to 750,000 vehicles, and if you include every nut and bolt, workers, and robots, it’s barely controlled chaos. Each line is a marvel, making both cars and powertrains for Maruti Suzuki models like the Baleno, Swift, Dzire, and Fronx. Forget about tiring, repetitive assembly—the plant is flooded with automation, high-tech robots sculpting car bodies, and AI-based systems checking each weld and bolt.
There’s a saying among insiders that SMG is India’s most “forward-looking” factory. Why? Because it’s the first wholly owned Suzuki plant outside Japan—meaning, Suzuki called all the shots. This control has let them push boundaries on efficiency and sustainability. Roughly 3,500 robots ventilate the body shops, paint units recycle their own water, and solar power panels cover the roof. Every two minutes, a new car roars to life on the end of the line, destined for a congested Indian street or the open roads of Africa.
What really stuns industry visitors are the logistics—literally, it’s a city in itself. The supply chain weaves into the factory like lifeblood, and the scale is huge: metal presses the size of apartments, conveyors threading through the ceiling, and endless fleets of little yellow AGVs (Automated Guided Vehicles) skittering like ants. SMG didn’t just make a giant plant; they designed an ecosystem that keeps it humming 24/7.
And there’s one more stunning fact: the plant achieved this scale without the strikes and slowdowns that have hit other industry hubs. Part of that magic is a tight-knit workforce—locals who’ve found new careers, engineers posted from Japan, management willing to tinker and experiment.
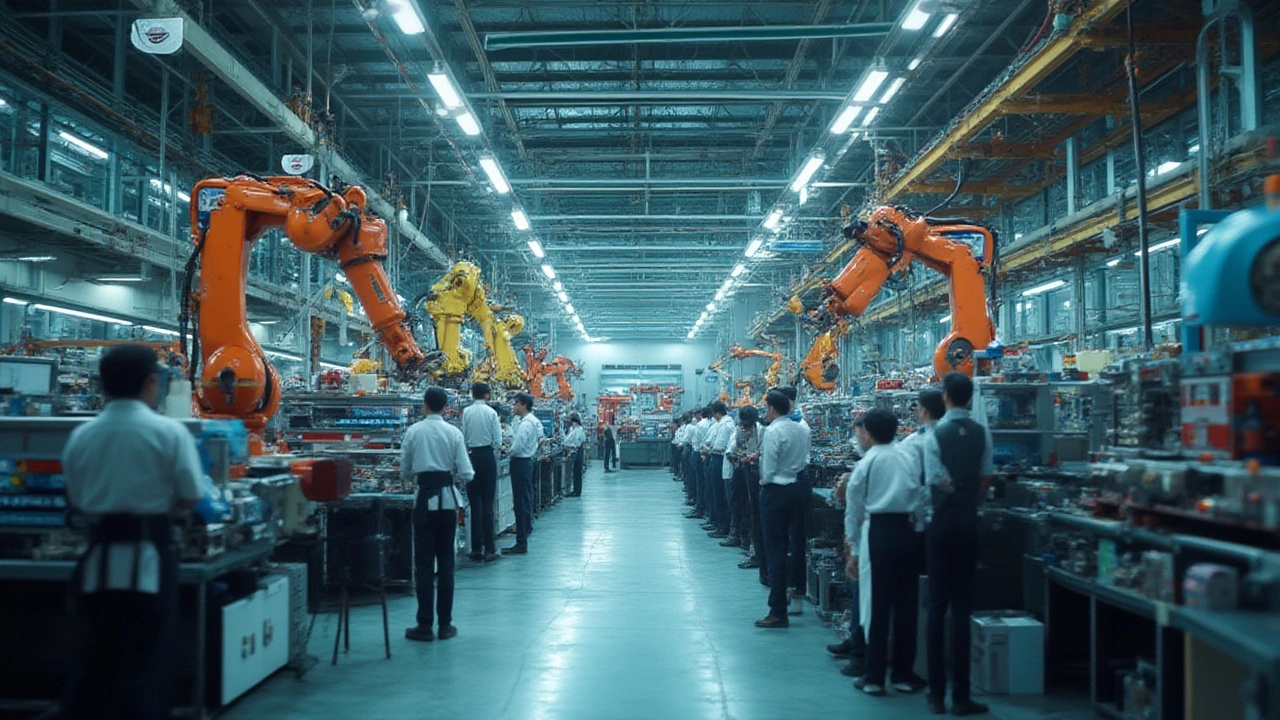
Why Suzuki Motor Gujarat Matters for Indian Manufacturing
Most car buyers never think about what happens before their vehicle shows up at the showroom. But the ripple effect from Suzuki Motor Gujarat stretches way beyond just cars rolling off the line. It’s made Gujarat a magnet for auto suppliers—companies that build steering columns, make wiring harnesses, mold bumpers, and more. The supplier park right next door houses dozens of ancillary industries, which means more jobs (over 10,000 including suppliers), more training, and upgraded skills for locals.
Suzuki has handed over the blueprints to lean production—meaning, fewer errors, faster cycles, and real-time tweaks. Quality isn’t just an afterthought. Each car goes through computerized testing at every step: laser vision systems check paint finishes, automated torque tools measure each bolt, and even the tiniest audio glitches are picked up by sensitive microphones in the test bay. SMG trained its thousands of staff extensively so that everyone—from robot operators to final inspectors—catch slip-ups before the car leaves the factory gates.
There’s a green angle, too. You can’t walk across the plant without bumping into recycling bins, solar panels, or water harvesting tanks. Factories this size historically guzzled power and spit out pollution, but SMG’s model is different. Large parts of the plant run on renewable energy; water is cleaned, reused, and replenished, and strict rules cut down on landfill waste. This factory quietly shows other Indian auto plants how to go green—and save money in the process.
Exporting from SMG is slick and high-volume—nearly 35% of production gets loaded onto trucks, then to massive ships headed for 100-plus countries. Suzuki Motor Gujarat hasn’t just doubled down on Indian demand, but it’s turned the country into a global export hub. You can spot a Baleno wearing a Kenyan license plate, or a Swift dodging potholes in Chile. That’s the reach we’re talking about.
Of course, SMG isn’t the only big fish. Hyundai’s Chennai plant and Tata’s Pune facility put out whopping numbers too, with Hyundai’s numbers close behind at roughly 700,000 units annually. Still, the sheer centralized scale and export focus of Suzuki Motor Gujarat is what keeps it at the top of the heap right now.
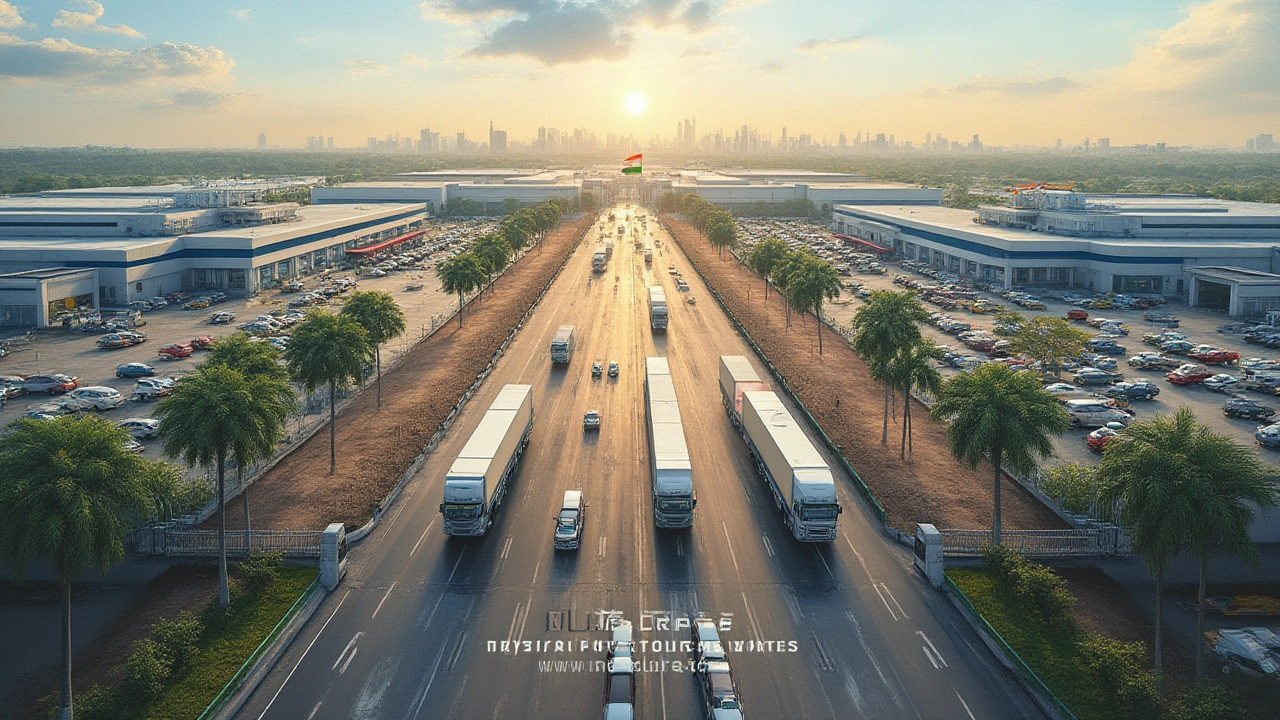
What Goes Into Making a Record-Breaking Car Plant Tick?
It’s tempting to think that size alone makes a difference, but there’s more to the largest car plant in India than just land and stockpiles of steel. What sets Suzuki Motor Gujarat apart is its deadly focus on efficiency, speed, and flexibility. It’s not just a monolithic place; each line can adapt quickly when there's a sudden demand spike for a new hatchback model or a completely fresh design. Engineers here play chess against chaos, tweaking schedules and juggling priorities almost daily. New model? They can gear up and start full production in about two months, a pace that was unheard of a decade ago.
Worker training is another crucial piece. SMG has a dedicated training center—think of it as a university inside a factory. New hires, many just out of school, practice on simulator machines and VR rigs before working live assembly. Mistakes happen in the virtual world, not on real cars. Managers pride themselves on low turnover. Skilled workers stay put, knowing they’ll get steady raises, upskilling, and even international assignments at Suzuki’s plants in Japan or Europe.
If you walk through the assembly lines, you’ll notice small but powerful improvements everywhere—ergonomic tools for less fatigue, screens showing live status, even color-coded bins so mistakes stand out instantly. The atmosphere isn’t grim and noisy as you might expect from such a large factory. There’s a sync between human and machine, a kind of rhythm that makes it feel almost choreographed.
- Tight inventory controls: Tiny on-site warehouses, with just-in-time supply arriving minutes before a part is installed.
- Vendor integration: Supplier teams have offices on plant grounds, troubleshooting issues in real-time instead of shipping back and forth.
- Digital quality tracking: Each car’s journey through the line is monitored by an ID tag, recording hundreds of checks along the way.
- Flexible export packaging: Different country regulations mean constant tweaks in badging, safety gear, and even color choices.
So if you’re standing in a showroom, wondering how that new Swift reached you so quickly, remember: it came from the largest car plant in India, a place where human skills and machinery blur, and where a near-constant ballet of parts, people, and robots is setting the standard not just for Indian, but for global car manufacturing. SMG isn’t just big—it’s smart, green, and future-proof, putting India firmly on the world automotive map. Next time you spot a convoy of brand-new Marutis on a freight train, you’ll know the mammoth story behind it.