If you think making stuff is just assembling parts with fancy machines, think again. Some manufacturing processes push the limits of technology, science, and human patience. Among them, one stands out for mind-bending complexity: semiconductor fabrication—the process behind your phone’s brain and just about every modern device. Just how tough is it? Let’s break down what makes certain manufacturing processes a true nightmare for engineers and why no other industry comes close to matching the chaos and precision of chipmaking.
Why Semiconductor Fabrication Takes the Crown
Let’s be blunt: semiconductor manufacturing isn’t just hard—it's on a whole different planet. Imagine trying to arrange atoms within nanometers of precision, in a massive dust-free lab where even a stray skin cell can wipe out millions of dollars in microchips. A modern chip plant, called a fab, costs over $15 billion to build and can take years before it spits out a single working wafer. For reference, Taiwan’s TSMC spends more on a new plant than some countries spend on their entire defense budget.
The challenge starts with the size. Silicon chips today—like the Apple M4 or Intel’s “Meteor Lake”—are built with features that are just a few atoms thick. We’re talking about stuff smaller than viruses. Everything happens at 3 or even 2 nanometers (that’s about 1/40,000th the width of a human hair). In a fab, every particle of dust is the enemy. Operators wear full-body suits—think ‘astronaut meets surgeon on a sci-fi set’—to avoid contaminating the product. Most of the manufacturing is automated, but even robots can’t move too fast, or they’ll vibrate the delicate wafers and ruin months of work.
Here’s a wild fact: making one chip can involve over 1,000 individual steps, all of which must happen in a carefully controlled sequence. If a single step goes wrong—say, a laser misfires, a chemical gets too warm, or a heater is one degree off—the result is a useless chip. Failures routinely cost tens of millions. Imagine the frustration of baking the world’s smallest, most expensive cake, and then someone sneezes in the kitchen.
The process relies on precision engineering and tools that sound more like science fiction: extreme ultraviolet (EUV) lithography machines made by ASML in the Netherlands, for example, use lasers to create patterns at the atomic scale. Each EUV machine can cost $200 million. Scientists need to mix chemicals with accuracy reaching a fraction of a drop and maintain cleanrooms up to 10,000 times cleaner than a hospital surgical suite. If one machine breaks—a single faulty laser or a contaminated chemical line—entire batches worth millions can be lost.
According to a recent IEEE Spectrum report, “The biggest challenge isn’t building a chip. It’s building every chip exactly the same, hundreds of billions of times, with no defects.”
“Semiconductor fabrication is the most complex manufacturing process engineered by humans,”says Mark Liu, chairman of TSMC.
It’s no wonder that so few companies worldwide can pull this off: TSMC, Samsung, and Intel are the titans, and they’re all constantly at war with physics. There are about two dozen truly state-of-the-art fabs worldwide, and the know-how needed to manage one cannot be bought—it has to be built up over decades, one microscopic breakthrough at a time.
Other Contenders for Toughest Manufacturing Job
While semiconductors hog the spotlight, other industries also dance on the edge of the impossible. Aerospace manufacturing (think rocket engines or jet turbines), advanced pharmaceuticals, and synthetic diamonds all deserve a nod for being almost comically hard.
Let’s talk aerospace. Building a rocket engine means dealing with materials that will operate at thousands of degrees, withstand wild vibrations, and survive the violence of launch. Every single piece, no matter how small, has to meet crazy tolerances. Quality checks can involve everything from X-ray scans to destructive testing where an engine is blown up on purpose—just to see where it fails. For jet turbines, manufacturers grind fan blades so precisely that even a fingerprint’s worth of imbalance can cause a whole plane to shake itself to pieces.
In precision optics—think those gigantic mirrors for James Webb Space Telescope—engineers work with glass so flawless that anything less than “absolute zero defects” ruins a billion-dollar mission. And then there’s biotech manufacturing, where making a vaccine can be derailed by a single stray bacteria. Just one contamination, and years of research can get axed.
If you measure “difficult” by how few places on earth can do it—and how deep the expertise goes—these industries come close. But even here, computers and robots do a lot of heavy lifting. Semiconductor fabs, however, require a level of precision and risk management found nowhere else. “If you’re not sweating the small stuff, you’re already failing,” a veteran NASA engineer once joked at a conference, comparing space manufacturing to chipmaking: “At least rockets are big enough to see.”
And have you seen those videos of people making bespoke watch movements? Sure, artisanal watchmaking is fiddly and requires nerves of steel, but it’s playing a different sport from semiconductor fabs. Even the best mechanical watches use centuries-old techniques, while microchip manufacturing reinvents itself every two to three years.
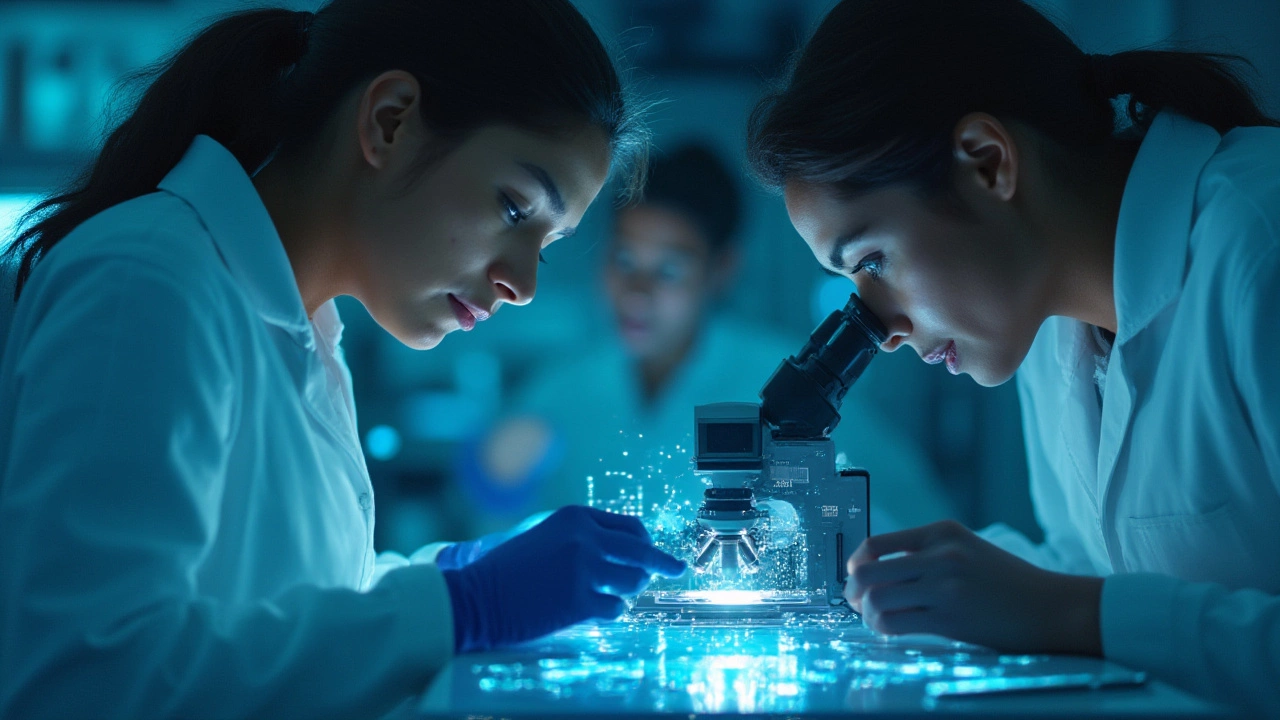
The Fragile Dance of Nanotechnology
If you want to grasp why some manufacturing processes are so brutal, you have to look at the scale. In nanotechnology, where the action happens at the atomic or molecular level, the laws of nature act differently. Gravity barely registers; instead, chemistry and quantum mechanics call the shots. Even basic problems—like moving one atom from A to B—require equipment more expensive than a fleet of Ferraris.
Semiconductor fabs ride this nanotech wave daily. To draw a circuit only a few atoms wide, fabs use bizarre stuff like high-energy plasma, rare noble gases, and electromagnetic fields strong enough to propel particles across labs at hundreds of kilometers an hour. Calibrating these machines is a back-and-forth between human techs, ultra-precise sensors, and AI-driven software that constantly tries to keep things going straight.
What really messes with the process is the sheer unpredictability. Silicon wafers can warp with the tiniest changes in temperature or humidity. The chemicals used—called photoresists—can be ruined if exposed to invisible levels of UV light. Even cosmic rays, zipping in from space, can leave tiny “holes” in a finished chip, rendering it defective. Some engineers put it bluntly: “Mother Nature hates perfect chips.”
Last year, a Dutch semiconductor fab halted production for days when an overhead light panel started flickering. That sent vibrations through a cleanroom, which shifted a laser by just a micron—about 1/100th the width of a hair. The result? Ten thousand chips were trashed. The lessons: every detail matters, and chaos comes from unthinkable places. The more advanced the process, the more even tiny errors can snowball into disaster.
Modern manufacturing at the nanoscale is a war with randomness. That’s why only a handful of firms can approach 3-nanometer chip making, and why start-up dreams of building a new fab usually die when founders see the price tag—billions upfront, zero guarantee of success for years.
Toughest Jobs: What It Takes to Survive
If you want into the world of elite manufacturing, you need nerves of steel, endless patience, and an appetite for stress. The teams inside a semiconductor fab have dozens of subspecialties—electrical engineers, chemical specialists, metrology gurus, even data scientists who crunch numbers in real time to spot a single defective wafer in millions.
You can’t fake experience here. Training a top-level process engineer takes a decade, and most never master more than a single tool or part of the process. Japanese fabs are famous for their apprenticeship culture: new hires start with years of cleaning and basic handling before they even touch a machine. And all the while, the machines change every few years, so constant learning is the only way in.
Tips for anyone crazy enough to try: Cultivate a sense of paranoia about details. Question every assumption, no matter how small. Build teams who can spot a deviation before it even happens. Learn from failure, because the best lessons come from the most costly mistakes. Consider building strong partnerships with equipment suppliers, too—the experts on their machines can save you millions in downtime.
If you’re aiming for a less intense challenge, other precision manufacturing jobs—like aerospace assembly or artisan watchmaking—offer plenty of satisfaction without the same level of existential risk. Each has its own rituals, tools, and history. But none quite combine the risk, the money, and the physics-pushing tech like making chips at the atomic scale.
At the end of the day, the hardest manufacturing process isn’t just a matter of complexity—it's doing impossible things, perfectly, day after day, while knowing that a sneeze, a drop of sweat, or even a particle from outer space can blow up a billion-dollar factory. No wonder only a handful of companies on the planet even try.