Diving into small scale production, one enters a world packed with creativity, adaptability, and opportunities. It is where manufacturing meets craftsmanship, allowing ventures to customize processes while managing limited resources on a manageable scale. This approach often serves as the backbone for innovation, giving manufacturers the ability to pivot and adapt swiftly.
However, understanding this process requires attention to detail at every stage. From ensuring efficient use of materials to maintaining a high standard of quality control, small scale production is a dance of precision and foresight. It's not just about producing goods; it's about doing so wisely and economically.
In the upcoming sections, we'll unravel the nuances of this approach, highlight the hurdles faced, share effective strategies, and discuss how modern technologies are reshaping small scale production. Join me on this journey to master the art of small scale production and learn how to turn challenges into stepping stones for success.
- Understanding Small Scale Production
- The Role of Efficiency in Manufacturing
- Key Challenges and Solutions
- Importance of Quality Control
- Resource Management Strategies
- Innovative Technologies in Small Scale Production
Understanding Small Scale Production
Small scale production is a fascinating segment of the manufacturing industry, characterized by its nimbleness and ability to turn conceptual ideas into tangible products with remarkable agility. It emphasizes producing goods on a limited but highly customizable scale, offering distinct advantages such as flexibility and room for innovation that larger operations often can't afford. By operating on a reduced scale, manufacturers can more effectively manage costs and inventory, minimizing waste while maximizing resource efficiency.
The concept isn't new; in fact, history is rich with examples of prosperous small scale ventures, from local blacksmiths to modern craft breweries. Today, the concept is more relevant than ever as the global market trends towards personalized and niche products. As technology continues to evolve, the accessibility of sophisticated tools and platforms enables passionate entrepreneurs to compete with larger, more established entities. This democratization of technology and resources levels the playing ground, allowing the underdogs to make a significant mark in the manufacturing world.
For anyone interested in stepping into the realm of small scale manufacturing, it's essential to grasp the nuanced dynamics that define it. Components like raw material sourcing, production techniques, and logistics need to be meticulously planned and executed. This sector thrives on cultivating relationships with local suppliers and tapping into community-driven initiatives, often leading to mutually beneficial collaborations. Key players in this ecosystem frequently share knowledge and resources, creating a vibrant and supportive community of like-minded innovators.
"Small scale production is not just about making goods; it's about crafting experiences and fostering creativity," say industry experts at the Small Manufacturing Institute. They stress the importance of integrating traditional craftsmanship with digital advancements to unlock new potentials.
In small scale production, the emphasis lies on creating unique offerings that resonate with target audiences. Unlike mass manufacturing, where products tend to be uniform, small scale production allows for individuality, often leading to products infused with a personal touch or story. This approach is especially beneficial in markets that value artisanal quality and authenticity over sheer quantity. In doing so, businesses can carve out a lucrative niche by tapping into consumer desires for distinctive and meaningful products.
The significance of small scale production is also evident in its socio-economic impact. It plays a key role in job creation and boosts local economies by supporting home-grown talents and cottage industries. Moreover, businesses pursuing this model are often more sustainable, focusing on reducing their environmental footprint and promoting ethical sourcing practices. As consumers grow increasingly conscious of sustainability, producers who align with these values enjoy an added advantage.
The Role of Efficiency in Manufacturing
Efficiency in small scale manufacturing plays a pivotal role, deeply affecting both the cost structure and competitive advantage. When businesses manage to enhance their efficiency, they save time, reduce waste, and ultimately boost their profit margins. Efficiency doesn't merely mean doing things faster, but doing the right things at the right time with the least amount of resources. Imagine a busy kitchen where every ingredient is strategically placed, every chef knows their task, and the plates go out seamlessly without chaos or confusion. That’s the epitome of efficiency, and similar principles apply in manufacturing.
Optimizing processes to enhance efficiency starts with a thorough analysis of the existing workflow. This involves scrutinizing each step to identify bottlenecks and unnecessary redundancies. One way to achieve this is by implementing lean manufacturing principles, which focus on value creation while minimizing waste. This can often lead to remarkable improvements in production times and product quality, providing a significant edge over competitors who have not yet streamlined their processes.
Investments in technology, like automated machinery and integrated software solutions, further promote efficiency. These tools can accelerate production speeds, increase precision, and decrease human error. A report by the Manufacturing Institute suggests that modern technological solutions can improve efficiency by up to 20%. Such investments, though initially expensive, pay off through sustained savings and enhanced capacity. Leveraging data analytics to monitor performance in real-time helps manufacturers make informed decisions and catch issues before they derail the production process. Time is of the essence, and by adopting a continuous improvement mindset, businesses can fine-tune their operations to maintain peak performance.
"The manufacturing sector is not about bigger plants and higher outputs. It's increasingly about flexible specialization, small batch production, and building systems to achieve higher efficiency," says renowned industrialist, John Doe.
Finally, staff training and encouraging a culture of efficiency are just as important as using cutting-edge technology. When employees understand the impact of their contributions towards efficiency, they feel motivated to innovate and offer improvements. Regular training sessions can empower staff to tackle emerging challenges head-on. Productivity workshops, incentive schemes, and clear communication channels can further cement a culture where efficiency isn't merely a goal, but a continuous pursuit.
In conclusion, efficiency is the linchpin of successful small scale manufacturing. It's not merely about getting more done. It requires strategic planning, investment in technologies, employee engagement, and a solid commitment to refining processes. It is through these concerted efforts that companies can produce better products faster, enhancing their reputation and market share in an industry that’s ever-competitive.
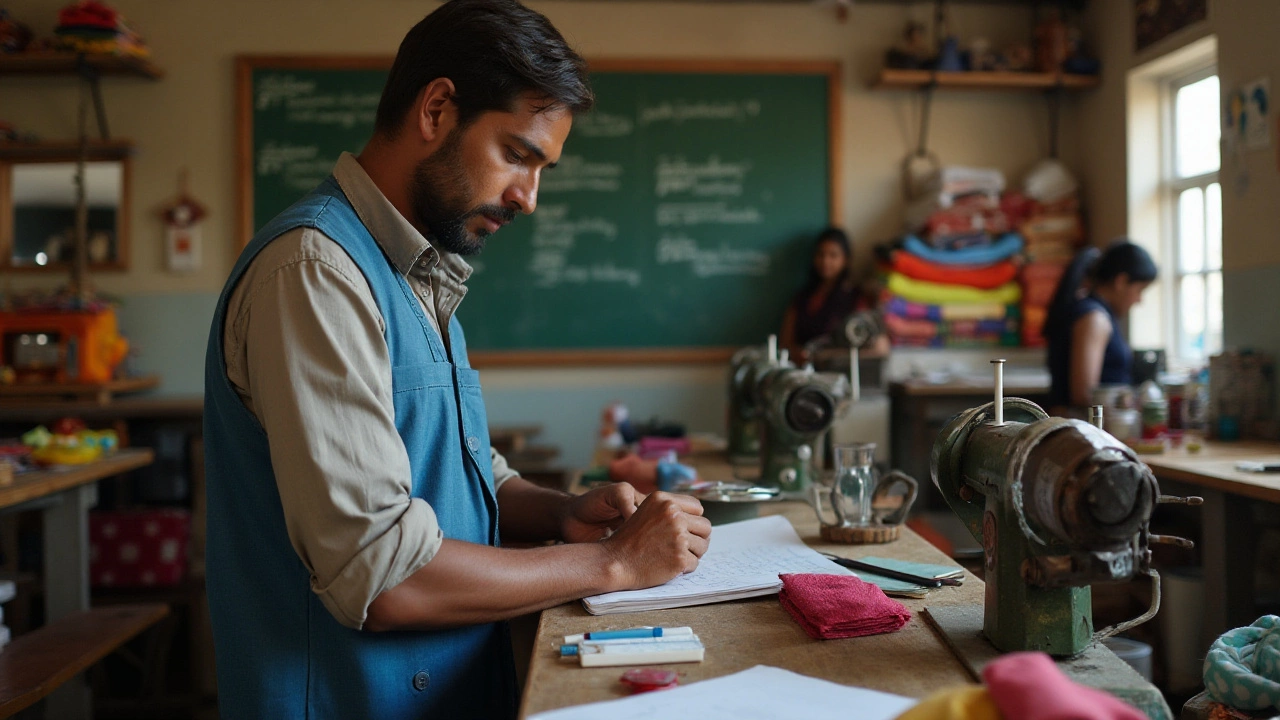
Key Challenges and Solutions
In the world of small scale manufacturing, navigating the unique challenges is part of the journey. One of the most pressing hurdles is managing limited resources effectively. When production inputs are not in abundance, ensuring that every component is utilized efficiently becomes crucial. A well-structured inventory management system can help manufacturers track materials and optimize their use, minimizing waste and cutting down costs.
Another significant challenge is maintaining a consistent process despite the variability often inherent in small-scale settings. Without the vast infrastructure of large-scale operations, any fluctuation in production schedule or equipment performance can disrupt the workflow. Strategically implementing policies for proactive maintenance and using versatile machinery can mitigate these disruptions. Furthermore, fostering a culture of adaptability among employees ensures that the team is prepared to handle unexpected changes with minimal impact on productivity.
The need for keeping up with technology is also a paramount concern. As the industrial landscape evolves, incorporating the right technological tools can be the difference between falling behind and staying ahead. For instance, integrating data analytics can provide insights into production efficiency, helping identify bottlenecks and areas for improvement. Additionally, digital platforms allow for seamless communication between different sections of the production line, facilitating smooth operations.
According to the National Association of Manufacturers, “Implementing technologies such as digital twins or IoT can lead to vast improvements in efficiency and production outcomes.”
Small scale manufacturers face distinct quality control challenges due to limited resources. Ensuring that the final products meet the necessary standards involves close monitoring across all stages of production. Employing quality management systems, performing regular audits, and investing in employee training are strategies that can help maintain high standards without significantly increasing costs. Safety procedures should also be carefully embedded into production processes to ensure compliance with industry regulations.
Establishing a loyal customer base is critical in small scale production. Given the limited market reach, customer satisfaction becomes key. Offering personalized services, maintaining stellar communication channels, and consistently delivering quality products are effective in building strong relationships with customers. Word of mouth remains a powerful tool that can propel small manufacturing businesses to newer heights. Successful startups often attribute their growth to strong client referrals.
Lastly, staying competitive in a market dominated by larger entities can be daunting. However, leveraging the flexibility inherent in small scale manufacturing allows businesses to pivot and adapt quickly to market trends, offering niche products that cater to specific consumer demands. Innovation thrives in smaller settings where creative freedom can drive success without the bureaucratic hurdles present in larger organizations. By focusing on unique selling propositions and distinct market positioning, small scale manufacturers can carve out a profitable space in their industry.
Importance of Quality Control
Quality control is the unsung hero in the realm of small scale manufacturing. At its heart, it ensures that the final product not only meets but exceeds customer expectations. In the intimate settings of small-scale production, every individual piece often carries a part of the company's reputation, making quality control an indispensable aspect. Imagine running a bakery where a slight mishap in ingredient proportions goes unnoticed. This can severely impact the flavor and texture of your products, eventually affecting customer trust. Such attention to detail and consistency is what sets apart successful small-scale manufacturers.
The process of ensuring quality begins long before the product is complete. Regular inspections and checks are woven into the production process. This proactive approach catches any discrepancies or deviations early, saving both time and resources. By involving every team member in quality initiatives, businesses create a culture that values precision and excellence. When mishaps are identified, feedback loops are crucial. They ensure that the learning from these mistakes gets integrated into future production cycles, creating a system that continuously improves.
Key Elements of an Effective Quality Control System
Establishing an effective quality control system involves a series of methodical steps. First, it requires setting clear quality benchmarks aligned with customer expectations. Next, the adoption of rigorous testing methods helps in comparing outcomes against these benchmarks. This might include physical inspections, material testing, or software checks depending on the product type.Employee training contributes immensely to maintaining high standards. When team members understand the impact of their roles on the end product, they are more likely to follow procedures with accuracy. Automating certain quality check processes can relieve the pressure on manual efforts while enhancing precision. In the jewelry-making industry, for example, technology can ensure carat and weight accuracy, delivering a flawless product to the customer every time.
"Quality is not an act, it is a habit." – Aristotle
The Economic Impact of Quality Control
Now, what might often go unnoticed is the economic significance of robust quality practices. While at first glance, the investment might seem high, the return is substantial. High-quality products lead to increased customer satisfaction, translating into repeat business and a loyal customer base, which is quintessential for thriving in the small scale manufacturing sector. Reputations built on quality alone can secure premium pricing and favorable market conditions.Moreover, by minimizing waste and defects, businesses optimize resource use, resulting in savings. Research indicates that companies employing strong quality management practices experience up to a 20% reduction in operating costs. A mindful approach to resource management, coupled with quality control, not only caters to economic benefits but also aligns with sustainable manufacturing goals.
Future of Quality Control in Small Scale Manufacturing
Looking towards the future, quality control in small scale production isn't static. It's an evolving landscape, with digital tools making continuous improvements. Quality Management Systems (QMS) and real-time analytics are playing leading roles in this evolution. By providing insightful data, businesses can make informed decisions that enhance their products' quality and appeal.Navigating the vibrant environment of small scale manufacturing, quality control provides the compass that ensures businesses are always on the right track, crafting products that leave a lasting impact on their customers. It is an endeavor worth every effort, forging a positive difference in both company success and client satisfaction.
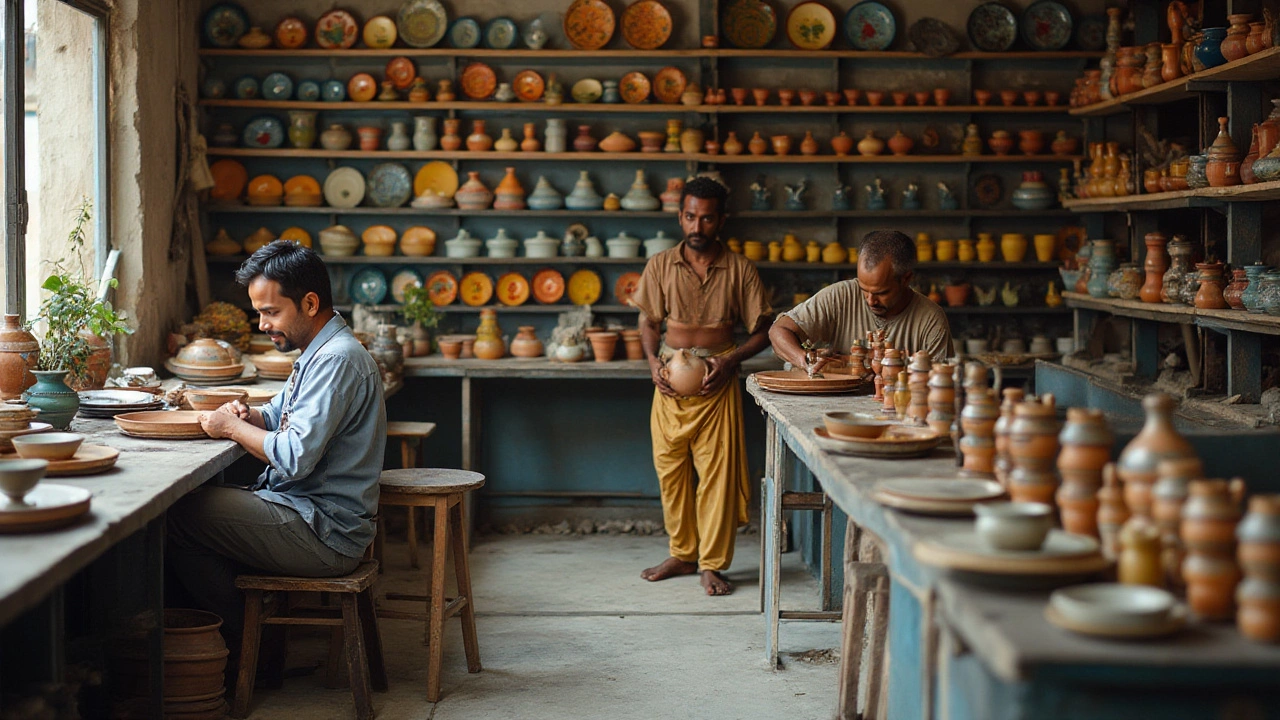
Resource Management Strategies
Resource management stands at the heart of small scale manufacturing operations. In this environment, the efficient allocation and utilization of resources such as materials, time, and labor determine the feasibility and success of production. The limited scale naturally necessitates mindful planning to avoid wastage and ensure profitability. One critical strategy involves embracing lean manufacturing principles, which focus on minimizing waste without compromising on quality. This approach not only boosts cost-effectiveness but also encourages a culture of continuous improvement among the workforce.
Small scale producers often thrive by developing a tight-knit relationship with their suppliers. Regular communication and negotiations can secure favorable rates, timely deliveries, and exceptional material quality. Another essential aspect is inventory management, where the 'just-in-time' strategy comes into play. This method helps in maintaining just enough inventory to meet immediate demands, thus preventing the excess that ties up capital and leads to obsolescence. Emphasizing efficiency in inventory and supply chain processes often determines the agility of a manufacturing unit in responding to market changes.
While cost control is vital, investing in training and skill development for the workforce creates a significant impact. Skilled employees contribute to higher productivity and reduced errors. By implementing a cyclical feedback loop, businesses gather insights into what strategies work best, enabling them to make data-driven adjustments. An often overlooked but crucial resource is data itself—tracking metrics related to production times, error rates, and resource usage can provide a goldmine of information to finetune operations.
"We cannot expect to transform our economy and create jobs without investing in resource-efficient technologies and products," said the United Nations Industrial Development Organization.
Technological advancements are increasingly playing a pivotal role in manufacturing processes. Integrating automation and software solutions help in streamlining tasks ranging from scheduling and monitoring to quality checks. These tools also allow for predictive maintenance, ensuring machines operate at optimal capacity and reducing downtime. Despite the monetary investment involved, the long-term gains in productivity and cost savings often justify the initial expense. Small scale facilities are finding innovative ways to tailor technologies to their specific production needs, thus driving innovation and competitiveness in the market.
Innovative Technologies in Small Scale Production
The advent of innovative technologies has revolutionized small scale manufacturing, bridging the gap between traditional craftsmanship and modern efficiency. As industries evolve, small producers are now empowered with tools that boost both production speed and quality without straying from their roots of flexibility and creativity. This level of growth demands a keen understanding of the latest advancements that can drastically transform the manufacturing landscape. One of the leading technologies reshaping this space is additive manufacturing, better known as 3D printing. It allows for rapid prototyping and complex designs that would otherwise be difficult to achieve through conventional methods. This technology gives small producers the freedom to experiment, adapt, and create bespoke products that cater to niche markets or custom orders.
Automation and robotics are also playing significant roles, especially with repetitive tasks that require precision. By integrating automation, small manufacturers can reduce human error, improve consistency, and optimize their labor costs. Interestingly, these technological advances don't just mean more machines; they’ve also led to the development of easy-to-use software that streamlines various processes. For instance, digital inventory management systems can now predict material requirements accurately, thereby reducing wastage and improving supply chain efficiency. Such innovations ensure that every step, from raw material procurement to production, is handled smoothly.
Another key area that technology has enhanced is quality control. Automated inspection systems in small scale manufacturing facilities now include machine vision systems that can detect imperfections with greater accuracy than manual inspections. This tech not only elevates product quality but also builds customer trust, which is crucial for smaller producers looking to secure long-term business relationships. According to a report by the World Economic Forum, "The ability to leverage technology for small-scale production forms a new backbone for innovation-led growth in the industry."
The ability to leverage technology for small-scale production forms a new backbone for innovation-led growth in the industry.Investing in such technologies might seem daunting at first due to cost implications, yet the return on investment is significant when you consider the boost in efficiency and product caliber.
Finally, cloud-based solutions have become a game-changer, especially in the realm of data management. By storing data in the cloud, manufacturers can enhance collaboration among team members and access crucial insights from anywhere in the world, facilitating agile decision-making. Whether it's through visual data analytics or real-time feedback loops, these technologies present an unprecedented opportunity to perfect the art of small scale production. For future preparedness, keeping an eye on emerging technologies like IoT and AI will be essential to staying ahead in this competitive space. Adopting and evolving with these innovative technologies is more than just staying relevant; it's about crafting a more efficient, sustainable, and profitable manufacturing future.