If you look around your home or office, odds are you can count at least ten different plastic products in seconds—water bottles, phone cases, food containers, that chair you’re sitting on. But who actually makes all this plastic? It’s not just one giant company cranking out everything. The world of plastic manufacturing is packed with specialized companies, each with their own focus and process.
Understanding who’s behind the plastic in your daily life isn’t just trivia. Knowing about manufacturers can help you make better choices, especially if you run a business that depends on plastics. Want something custom made? Need to know which brand is serious about recycled materials? It all starts with knowing who the major manufacturers are, how they work, and what sets them apart.
- What Does a Plastic Manufacturer Actually Do?
- The Biggest Plastic Makers Around the Globe
- Specialty Players: Beyond the Big Names
- Plastic Production: Materials and Methods
- How Recycling and Sustainability Are Changing the Game
- Tips for Working with Plastic Manufacturers
What Does a Plastic Manufacturer Actually Do?
A plastic manufacturer isn’t just churning out random products—they’re experts at turning raw materials, usually called resins or polymers, into the plastics we use every day. There’s way more to it than just pressing a button. These companies handle a full process, often starting with granules, pellets, or powders that get melted down and shaped into thousands of things, from pipes and car parts to food wrappers and toys.
Here’s what usually goes on inside a plastic manufacturer’s facility:
- Choosing the right resin: Manufacturers pick the material based on how tough, flexible, heat-resistant, or food-safe the final product needs to be.
- Mixing additives: Sometimes color, texture, or extra strength is needed. Additives like UV protectors or flame retardants get blended in.
- Forming the plastic: This is where the magic happens—using methods like injection molding, blow molding, or extrusion. Each method is picked based on the product shape and function.
- Finishing work: Trimming, smoothing, or even printing logos onto the plastic happens next, so the item is ready to hit shelves.
- Quality checks: Before shipping, a lot of companies run tests to make sure products meet safety and quality standards.
Some plastic manufacturers run specialized lines just for certain industries—think medical-grade syringes or super-durable construction pipes. Others mass-produce more everyday stuff like bags, packaging films, or food tubs. And while some companies focus on brand-new plastic, others build their business around recycling used plastic into something new. That’s a growing trend, especially with all the talk about environmental impact.
Common Manufacturing Methods | Main Products |
---|---|
Injection Molding | Car parts, bottle caps, toys |
Blow Molding | Bottles, containers, tanks |
Extrusion | Pipes, tubes, sheets |
Thermoforming | Food trays, packaging, clamshells |
So if you see a plastic item, it’s had a whole journey—planned and shaped by manufacturers specializing in the science, art, and business of plastic production.
The Biggest Plastic Makers Around the Globe
If you’re wondering who really drives the global plastic manufacturers market, you’ll see some mega players pop up over and over. These are companies whose names might not be on your shampoo bottle, but trust me, their plastic is probably inside it.
- ExxonMobil Chemical – This U.S. giant regularly ranks at or near the top. They crank out millions of tons of polyethylene and polypropylene each year. Their plastics end up in packaging, automotive parts, and even toys.
- LyondellBasell – Headquartered in the Netherlands but with a big U.S. presence, this company is one of the world’s largest for polyolefins. They make everything from food wrappers to industrial pipes.
- SABIC – Owned by the Saudi government, SABIC is huge in the Middle East and globally. They focus on both commodity and engineered plastics and are pushing hard into more sustainable plastic products.
- INEOS – Out of the UK, INEOS supplies a ton of materials for construction, packaging, and medical uses. They’re not just about volume; they’re strong on innovation too.
- BASF – This German powerhouse is famous for its chemicals, but it’s also top-tier in plastic production, like polyamide and polyurethane products found in everything from electronics housings to sneakers.
Here’s a snapshot of what their annual plastic production looks like, just to give you a sense of scale:
Company | Estimated Annual Plastic Production (in million tons) |
---|---|
ExxonMobil Chemical | ~12 |
LyondellBasell | ~9 |
SABIC | ~8 |
INEOS | ~7 |
BASF | ~5 |
Most of these plastic manufacturers work all over the planet, with giant plants near major ports or chemical hubs. They do it this way to keep shipping costs down and to feed raw materials in as fast as possible. You’ll find their products everywhere: medical gear, cell phone covers, auto parts, food packaging, and pretty much everywhere plastic is used. Next time you toss a bottle in the recycling bin, there’s a good chance it started out at one of these companies.
Specialty Players: Beyond the Big Names
When you think about plastic manufacturers, it's easy to just picture the big corporations pumping out mountains of plastic pellets. But a lot happens outside of those giants. Specialty players focus on unique products, materials, or methods that the biggest companies just don't touch.
Some focus on advanced materials. Take Evonik Industries in Germany, known for their fancy engineering plastics used in car parts and medical devices. There are companies like Borealis AG from Austria, who make top-notch polyolefins—mostly used in pipes and power cables.
Other companies zero in on certain markets. For example, Tekni-Plex from the U.S. is big on medical and food packaging, making custom plastic films for things like blister packs and pill bottles. Meanwhile, SABIC Innovative Plastics gears their production towards industries like aerospace and cars, making materials tough enough to handle just about anything.
What really sets these plastic manufacturing companies apart?
- They can produce highly specialized compounds or resins, tuned for extreme conditions or exact customer needs.
- They're more flexible in making smaller, custom orders.
- They often do lots of research with customers, so products actually solve real-world problems.
If you're in a niche business—maybe you need a new medical device housing or lightweight but super-strong car panels—these specialty players are the ones you end up talking to. They might not produce the same sheer volume as the big players, but their expertise can make projects possible that general-purpose suppliers just can't deliver on.
Want some numbers? Check this out for some well-known names and their specialties:
Company | Specialty | Main Region |
---|---|---|
Evonik Industries | High-performance plastics, medical, automotive | Europe |
Tekni-Plex | Medical packaging, food films | USA |
Borealis AG | Polyolefins, pipe, cable insulation | Europe |
Celanese Corporation | Engineering polymers, electronics, automotive | USA |
SABIC (Specialty division) | Aerospace, automotive, electrical | Global |
Next time you pick up a specialized product—say, a medical mask or an insulated wire—there’s a decent chance it came from one of these expert plastic production teams, not just the household-name giants.
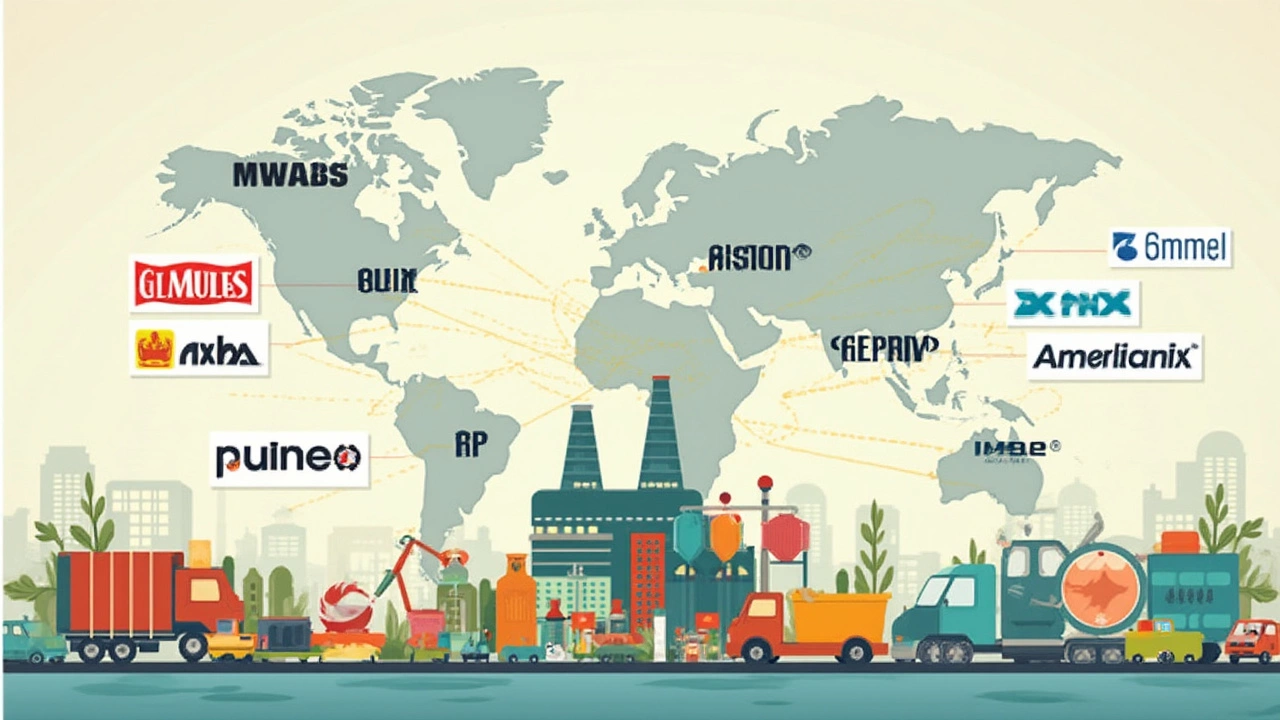
Plastic Production: Materials and Methods
Most plastic manufacturers start the process with raw ingredients like crude oil, natural gas, or even corn (for bio-based plastics). These raw materials are broken down into base chemicals and then turned into polymers, the key building blocks for plastics. Don’t let the word “polymer” trip you up—it just means chains of tiny repeating units, connected like beads on a necklace.
The two biggest families of plastics are thermoplastics and thermosets. Thermoplastics, like polyethylene and polypropylene, can be melted down and reshaped again and again. Think of how water bottles and piping are recycled. Thermosets, used in things like electrical parts and adhesives, are tougher. Once they set, there’s no melting them down and starting over.
Companies use different methods depending on the final product:
- Injection Molding: This is perfect for making lots of identical items, like cutlery, bottle caps, or phone cases. The process shoots hot, liquid plastic into a mold, then cools it down so it keeps the right shape.
- Blow Molding: Ever wonder how hollow items like bottles get made? Manufacturers shoot air into heated plastic, making it expand into a mold. Super common for drink bottles.
- Extrusion: This method pushes melted plastic through a shaped opening, kind of like squeezing toothpaste. It's used for pipes, straws, and window frames.
- Rotational Molding: Here, the mold spins while heated plastic inside sticks to the walls. Playground balls, water tanks, and storage bins are made this way.
Here's a quick look at which plastics dominate the industry and what they're made into:
Plastic Type | Main Use | Common Production Method |
---|---|---|
Polyethylene (PE) | Packaging, bottles | Blow/Injection Molding |
Polypropylene (PP) | Automotive parts, containers | Injection Molding |
Polyvinyl Chloride (PVC) | Pipes, window frames | Extrusion |
Polystyrene (PS) | Food packaging, insulation | Injection/Extrusion |
It’s not all about mass production, though. Some plastic companies are pushing boundaries with bioplastics, using plants or even recycled plastic waste instead of fossil fuels. That means the world of plastic production is always changing, with both big chemical suppliers and small startups trying new materials and smarter, greener methods.
How Recycling and Sustainability Are Changing the Game
Plastic manufacturers aren’t just thinking about making products cheaper and faster anymore. Now, there's real pressure to shrink their environmental footprint. Across the plastic industry, big names like Dow, BASF, and SABIC are tweaking how they do things because businesses and regular folks want greener solutions. They’re testing new materials and changing where plastics come from – not just oil, but more from recycled content or plants.
Check this: according to the Plastics Industry Association, in 2023 about 9% of all plastic produced worldwide was made from recycled stuff. That might sound small, but it’s much higher than it was ten years ago. Some specialty players, like Loop Industries and TerraCycle, focus entirely on taking used plastics and giving them new lives in packaging, clothes, and more.
Here’s what’s actually changing on the ground:
- Plastic manufacturers are rolling out more products made from recycled plastics (sometimes labeled rPET, rHDPE, etc.).
- Companies are using less packaging and making plastics that break down faster or are easier to recycle.
- Big customers, like Coca-Cola and Unilever, now demand their suppliers use more recycled or plant-based content.
- New methods, like chemical recycling, are popping up, breaking plastics down at the molecular level so they can be rebuilt like new.
Here’s a quick look at some 2023 numbers for the world's top recycled plastic producers:
Company | Tons of Recycled Plastic Produced (2023) |
---|---|
Veolia | 420,000 |
Borealis | 130,000 |
Indorama Ventures | 350,000 |
This push is about more than looking good. Governments in the U.S., Europe, and Asia are actually making laws that force plastic manufacturing companies to use less virgin material and stick to tougher recycling rules.
“Sustainability isn’t a side project anymore—it’s now a big part of every strategy discussion,” said Mark Nikolich, CEO of Braskem America, in a 2024 industry panel.
If you want to work with a manufacturer who really cares about recycling and sustainability, ask questions: How much recycled content do they use? Do they take back scrap or old parts? Some companies even have environmental reports online you can check before signing a deal.
Tips for Working with Plastic Manufacturers
If you’re planning to partner with plastic manufacturers, you’ll want a smooth, hassle-free experience. It's not as simple as just placing an order—what you ask, how you plan, and even the manufacturer you pick can make or break your project. Here’s how you can make the most out of your relationship with these companies.
- Be clear with your requirements: Always give detailed info on what you want. Specify the size, color, type of plastic, and if you need any certifications (like FDA approval for food contact or RoHS for electronics).
- Understand the company’s core strengths: Some plastic companies are experts in packaging, others focus on automotive parts, toys, or medical gear. Check their portfolio, ask what materials they’re best with—polyethylene, polypropylene, PVC, or something specialized like medical-grade resins.
- Check minimum order quantities (MOQs): Big names like SABIC or LyondellBasell often handle huge volumes. If you’re a small business, look for manufacturers that take smaller runs to save money and reduce waste.
- Ask about turnaround time and delivery: The global plastic production scene can face delays, especially with supply chain hiccups. Get a realistic delivery timeline and ask about shipping options. Some companies can ship directly to your warehouse or distribution partner.
- Discuss sustainability: More manufacturers now deal with recycled or biodegradable plastics. Ask what options they offer if you want to use eco-friendly materials. In 2024, over 30% of major plastic industry players worldwide reported they offer recycled-content products.
If you want a deeper look, here’s a quick comparison table showing what questions to ask different types of manufacturers:
Type of Manufacturer | Key Question | Why It Matters |
---|---|---|
Mass-Production Company | What’s the MOQ & bulk discount? | Keeps costs down for huge orders |
Custom Plastic Maker | Can you handle custom molds/designs? | Good for unique or non-standard parts |
Eco-Friendly Producer | Do you offer recycled or compostable plastics? | Supports a greener supply chain |
Region-Specific Supplier | How do you handle export and logistics? | Reduces shipping issues, faster delivery |
One last thing—build a long-term relationship. Good communication, honest feedback, and quick problem-solving will always pay off when you’re working with any plastic manufacturer.