Ever wondered why your T-shirt tag often says "Made in India"? It’s not just random. India’s textile industry is a beast, running wild across cotton fields, buzzing sewing lines, and swanky export hubs. Still, many folks keep asking if the sector’s real "boom" is just talk or actually starting.
The signs are everywhere, if you know where to look. Factory owners are rushing for new machines. Kids are doing internships in textile parks instead of fancy city offices. My own son Vihaan joked last year, “Dad, are socks from India taking over the world?” Not a crazy question, actually. India supplies yarn, fabric, and ready-made clothes to dozens of countries. Prices are competitive, and Indian brands are popping up in stores from Dubai to Berlin. But it’s not just about low costs anymore—quality and quick turnarounds are catching up.
If you’re scouting for trustworthy info—whether for investment, career moves, or you simply want to know why your jeans might soon say "By India," there’s a lot to unpack. The world wants more eco-friendly fabric and fresh designs, and India’s steps today could decide if it leads the global textile game tomorrow.
- What Makes India’s Textile Industry Special?
- How Government Moves Are Shaping Growth
- Tech Upgrades: From Cotton Fields to Smart Factories
- Why Exports Matter More Than You Think
- Bumps in the Road: Real Challenges for Manufacturers
- Tips for Riding the Boom and Not Missing Out
What Makes India’s Textile Industry Special?
It’s crazy how deep the roots of textiles run in India. Seriously, we’re talking thousands of years—think cotton spinning in villages before most countries even thought about fabric beyond wool. Today, India is second only to China when it comes to textile and garment production. That’s not just a history lesson; it’s why the country has such a crazy edge in this game.
First off, let’s talk raw materials. India is the world’s biggest cotton-producing country and holds a strong place in jute and silk too. This homegrown advantage saves money and gives local textile manufacturers India an automatic leg up on global costs. You can see it directly in export numbers. According to the Ministry of Textiles, India shipped textiles worth around $44 billion in 2023—a record!
Plus, you’ll find every kind of textile manufacturing here: yarn spinning, weaving, dyeing, or making ready-made garments. No need to ship things out halfway through. Everything stays under one roof—or at least, one country. This “farm-to-fashion” pipeline means faster delivery and stronger quality control.
Indian textiles are super flexible too. Designers in Ludhiana might be crunching out sportswear while workshops in Surat do mass production of saris. You want custom prints or big export batches? There’s a factory that fits. And, let’s not leave out the massive labor force—45 million people work in textiles, one of the biggest workforces in the country. For a lot of families, this is the backbone that pays for schooling and groceries (trust me, my daughter Kaia literally wore her brother’s hand-me-downs from a local mill).
- Access to raw materials: Massive cotton and jute output keeps costs low.
- All-in-one supply chain: Saves time and boosts quality control.
- Big, skilled workforce: Keeps things running no matter the scale—small or huge.
- Diversity: Traditional handlooms to modern machines all exist together.
Now if you’re into numbers, here’s a cheat sheet:
Stat | Figure |
---|---|
India's global rank in textiles | 2nd |
Textile exports (2023) | $44 billion |
Cotton production (2023) | ~6.1 million tons |
People employed | 45 million+ |
So, why is India so special for textiles? Simple: resources, know-how, variety, and the never-ending hustle from folks who’ve spun, woven, and stitched for generations.
How Government Moves Are Shaping Growth
The government in India isn’t just sitting and watching the textile scene—they’re rolling out new rules and pouring cash into the sector to shake things up. If you look at numbers, you’ll notice the Indian government pledged around ₹10,683 crore (that’s about $1.4 billion) for the Production Linked Incentive (PLI) scheme for textiles alone in 2021. The point? Get manufacturers to step up, export more, and use top-quality materials.
These funds aren’t just for anything. The PLI scheme mostly backs high-value fabrics and advanced material like man-made fiber and technical textiles. It gives makers a bigger reason to modernize factories, invest in better machines, and hire people with the right skills.
- State governments are making their own moves. Places like Gujarat, Tamil Nadu, and Maharashtra are fighting for new investment by offering land at low cost, easier paperwork, and electricity discounts for textile units.
- Policies like TUFS (Technology Upgradation Fund Scheme) have helped thousands of small and medium-sized firms buy modern looms and dyeing units.
- The government also runs the SITP (Scheme for Integrated Textile Parks), funding new textile parks so companies can work together, share equipment, and lower costs.
Here’s a quick look at how some recent moves are making a difference:
Initiative | Focus | Result So Far |
---|---|---|
PLI Scheme | Advanced fabrics, manufacturing scale | 64 new textile projects approved |
TUFS | Modern machinery funding | Helped upgrade over 38,000 units |
SITP | Textile parks with shared infra | 59 parks funded, jobs for 400,000+ |
Not everything is smooth, though. Speed bumps crop up: delays in clearances, uneven state-level incentives, and sometimes the policy goals don’t match ground reality. But the overall push from the government is clear—they want India to be seen as a global textile manufacturers India hub, not just a low-cost player. If the plans work, expect more local brands, smarter factories, and more jobs in your own city—maybe even for your own kids.
Tech Upgrades: From Cotton Fields to Smart Factories
It’s not just about spinning wheels and handlooms anymore. India’s textile industry is pumping serious money into tech at every stage—from how cotton is picked all the way to how your hoodie gets boxed for shipping. Trust me, this stuff is a big deal, not just for saving time but for getting sharper quality and beating global competition.
Let’s start on the farm. Traditional cotton picking? Super slow and honestly, back-breaking. Now, more farmers are using mechanical pickers, drip irrigation, and even sensor systems to monitor soil and weather. These upgrades mean more cotton per acre and less wastage. The Indian Council of Agricultural Research claims that modern tech can boost cotton yield by up to 20% while saving water. Not bad, right?
Jump to the factories and you’ll see plenty of changes there too. Old-school power looms are giving way to automated weaving machines that barely need any human touch. Digital fabric printers are speeding things up, ditching the mess and delay of traditional dyeing. And here’s something cool—some big mills use AI and IoT sensors to track each step in real time, catching faults on the fly. That’s how smaller companies can offer reliable stuff to buyers in the US and Europe, even if they’re not as big as China yet.
Here are some real-life upgrades happening now:
- Robot arms stacking finished fabric rolls—fewer injuries, fewer mistakes.
- Massive spinning machines that detect broken yarn instantly, cutting down waste.
- Cloud software tracking orders and supply chains to reduce delays and mix-ups.
- Solar panels on factory rooftops, bringing down electricity bills and pollution.
This turbocharged tech isn’t just fancy. It’s driving down costs, raising quality, and letting India hit export deadlines that used to be out of reach. More manufacturers are realizing if they don’t level up, they’ll lose buyers.
Check out this quick comparison of old vs new ways:
Stage | Old Method | New Tech | Result |
---|---|---|---|
Cotton Harvesting | Manual Picking | Mechanical Pickers | Higher yield & speed |
Fabric Weaving | Power Looms | Automated Weaving | Better quality, less labor |
Dyeing/Printing | Traditional Dyers | Digital Printers | Fast, eco-friendly |
Quality Control | Manual Checks | AI Sensor Systems | Early error detection |
Energy Supply | Grid/Electricity | Solar Installations | Lower costs, greener |
If you ever hear a textile manufacturers India executive talking about "Industry 4.0," this is what they mean. No room for guesswork anymore—the winners are those who put smart systems ahead of old habits.
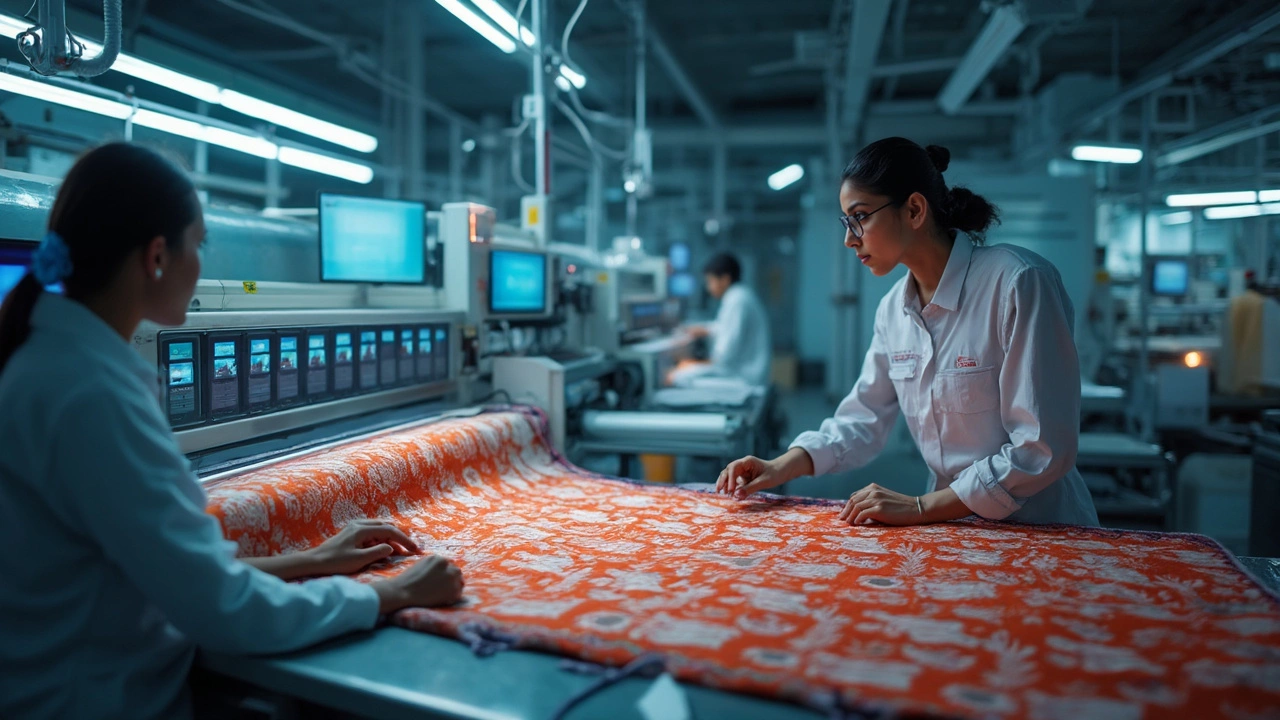
Why Exports Matter More Than You Think
Exports are the big deal that keep the Indian textile industry on its toes. Here’s something wild: India sends out textiles and apparel worth over $44 billion a year. That’s not just a random stat—these shipments keep factories running, families earning, and entire small towns buzzing from Punjab to Tamil Nadu. Without this export muscle, the local market alone wouldn’t come close to offering so many jobs or growth.
Now, why is this so important right now? There’s a global tug-of-war on cotton shirts and synthetic fibers. Countries like Bangladesh and Vietnam are also pushing hard in textiles, but Indian manufacturers have a leg up because they control the whole setup—from raw cotton to finished T-shirt. That’s called vertical integration, and it makes India faster and more reliable on big orders.
Exporting also pushes Indian companies to step up their game. Firms invest in better machines, adopt cleaner practices, and get smarter with logistics, just to keep up with international standards and delivery deadlines. The pressure to please international buyers has pushed India to boost its quality and speed at levels you just don’t see in markets that stay local.
Thanks to exports, India’s actually one of the top textile suppliers to heavyweights like the US and the UK. For example, the US alone imported over $8 billion worth of Indian textiles last year, which meant real sales, sure, but also kept a lot of looms and sewing lines moving when domestic demand slumped.
Here’s the kicker: when export markets grow, even local businesses benefit. Lots of small cities—think Tiruppur and Surat—boomed because global buyers poured cash into their mills. Indian firms also get quicker access to the latest global styles and production tricks, which explains why your favorite fashion app is now loaded with Indian-made outfits.
- If you want the TL;DR: Exports pretty much decide how big and strong Indian textile manufacturers get, and smart players never underestimate this link.
Missing out on exports means missing out on global money and new business ideas. For anyone tracking the textile manufacturers India scene, watching export trends is like watching the heart rate on a fitness tracker—it tells you if the industry’s really alive and kicking.
Bumps in the Road: Real Challenges for Manufacturers
If you think running a textile business in India is easy, think again. Being part of this industry comes with real headaches that can trip up even seasoned players. It's not just about weaving fabric and waiting for orders to roll in. There are hurdles at every stage, and these aren’t things you can ignore.
First up, there’s stiff competition from countries like Bangladesh and Vietnam. These guys often pay lower wages and run leaner shops. That means Indian manufacturers sometimes lose big overseas orders just because they can’t match rock-bottom costs. The global game is ruthless, making life tough for even the best-run mills here.
Let’s also talk about the never-ending dance with rules and paperwork. Red tape is still a monster in India. Whether it’s getting export clearances, GST hiccups, or labor compliance—it eats time and money. Many small factories just don’t have the resources to keep up with all this bureaucracy.
Another pain is the supply chain. Cotton prices are famous for jumping up and down with the weather, politics, and even global demand for T-shirts. When Cyclone Micha struck Gujarat in late 2023, cotton prices spiked overnight. One month you’re making a profit, the next you’re barely breaking even.
Modern tech is another double-edged sword. Sure, the fancy machines churn out fabric faster and better. But most small-to-medium textile units still use old, clunky looms. Updating all that gear costs a bomb. If you can’t invest, you get left behind. This is why massive mills in Tiruppur or Surat outpace others by a mile.
Here’s a quick glance at some problems and how often they hurt businesses—check out the table below for real numbers:
Challenge | Percent of Manufacturers Affected (2024 stat) |
---|---|
Supply chain issues | 68% |
Rising raw material prices | 73% |
Labor shortages | 49% |
Tech upgrade costs | 55% |
Compliance/paperwork troubles | 64% |
Don’t forget power cuts, unpredictable water supply, and finding skilled staff. For every big factory with solar panels and in-house training, you’ve got dozens still struggling to keep the lights on and meet deadlines. Even with a clear export order, a random blackout or shortage of dyers can stall a shipment cold.
Navigating these roadblocks isn’t optional. For textile manufacturers India has become both a dream and a test. The ones who make it are those who solve problems faster than their rivals—whether it’s by finding new suppliers, automating a tricky part of the process, or training workers for new tech.
Tips for Riding the Boom and Not Missing Out
If you want a slice of the textile manufacturers India story, there are some moves you really don’t want to miss. This isn’t about just guessing trends—it’s about knowing what works by looking at the habits of big winners in the industry.
- Go Digital Fast: Factories using smart sensors and cloud-based software cut 10–15% costs on average, according to a 2024 McKinsey industry report. Better inventory, fewer errors, and on-time deliveries win clients fast.
- Lean Into Sustainability: In 2023, over 35% of buyers from the US and Europe said they’d pay more for ethically made and eco-certified textiles. If you move now, you’ll stand out, plus local government grants are easier to snag for green projects.
- Up Your Exports Game: Indian exporters that attend global textile fairs see up to 25% jump in overseas orders. Make sure your business has an export license and a partner overseas to help with customs drama—it saves major headaches later on.
- Build Real Skills: It’s not just about machines. Skilled workers using modern looms or digital design tools can boost output by 20% per shift. Companies offering training get better staff retention and fewer production mistakes.
- Watch the Supply Chain: With global shipping delays still messing things up post-pandemic, factories that lock down reliable raw material sources and plan for backups see fewer shutdowns and lost sales.
Here’s a quick look at what’s making waves right now:
Trend | Impact in 2024-25 |
---|---|
Smart Manufacturing | Factories using automation report 15% higher output |
Eco-Friendly Production | Up to 40% increase in orders from EU buyers |
Skilled Workforce | Companies see 12% less product defects |
Global Trade Shows | Average order value jumps by 30% after event participation |
If you’re serious, move now, not later. Waiting for the perfect moment means you’ll just be buying the trend from someone else already ahead of you.