Manufacturing processes are fundamental to creating everything from small components to large-scale machinery. These processes are the methods by which raw materials are turned into final products. Understanding these techniques is not only vital for those directly involved in fabrication but also for anyone curious about where everyday items come from.
With an ever-evolving market landscape, the importance of efficient and innovative manufacturing cannot be overstated. The government plays a vital role in ensuring that these processes continue to improve, providing schemes and incentives to encourage advancements in technology and efficiency. This ensures that industries remain competitive and environmentally conscious, balancing profit with sustainable practices.
- Introduction to Manufacturing Processes
- Casting and Molding
- Machining Techniques
- Joining Processes
- Shearing and Forming
- Government Schemes and Support
Introduction to Manufacturing Processes
Manufacturing has been the cornerstone of human advancement, bridging the gap between conceptual ideas and real-world products. Quite simply, it is the process of turning raw materials into useful items. From ancient hand-crafted skills to today’s automated and complex systems, manufacturing processes have evolved alongside technology. Each process involves a distinct set of activities, tools, and techniques tailored to produce items efficiently and sustainably. With the rise of globalization, the methods employed in manufacturing processes have become crucial not only for individual companies, but for entire economies around the world.
The modern manufacturing landscape is diverse, encompassing a wide range of techniques. These can be broadly categorized into six main types, each with its own unique application and significance. This categorization helps industries to standardize and optimize production. The interaction between these processes and technological advancements has been profound, enabling a higher degree of precision, reducing waste, and minimizing operational costs. Interestingly, a fact from Deloitte indicates that the manufacturing sector has contributed about 16% to the global GDP, underscoring its importance in the world's economic fabric.
"Manufacturing is more than just putting parts together. It's coming up with ideas, testing principles, and perfecting the engineering, as well as final assembly." - James Dyson, British Inventor and Industrial Designer
Understanding these processes also involves grasping the principles behind each technique. For instance, casting and molding allow molten materials to take shape in a mold, while machining removes material to achieve a precise shape. Each process is selected based on factors such as material properties, required precision, and economic considerations. Efficient control over these processes leads to better quality and reduced production time. This echoes the central theme in many government schemes aimed at bolstering industrial progress and innovation.
With the advancement of Industry 4.0, manufacturing is now closely intertwined with digital technology. Smart factories and manufacturing techniques using IoT (Internet of Things) and AI (Artificial Intelligence) are becoming the norm. This digital transformation not only enhances productivity but also facilitates seamless adaptability to market demands. More industries are adopting flexible and integrated processes to remain competitive, which is crucial as customer expectations continue to rise. Embracing these techniques ensures the sustainability and scalability of manufacturing operations in today’s fast-paced environment. Understanding the foundation and continued evolution of manufacturing processes is indispensable for anyone interested in the industrial domain.
Casting and Molding
Casting and molding are two of the oldest yet most essential manufacturing processes in the industry, forming the very basis of how we create and shape a multitude of objects. These methods have been honed over centuries, evolving from simple sand casting techniques to the high-tech precision molding processes we rely on today. The essence of casting involves pouring molten material into a hollow cavity of a desired shape and allowing it to solidify. This versatile technique can be used with various metals such as steel, iron, and aluminum, and is critical for making parts with complex shapes that would be otherwise too challenging to achieve through machining.
The intricate process of molding, on the other hand, usually deals with plastics. Injection molding is a popular method where melted plastic is injected into a mold, solidifying into a specific form. Industries worldwide leverage this process due to its cost efficiency and ability to produce consistent, high-quality products. From the automotive sector to consumer electronics, the applications are vast and varied. One fascinating fact is that around 32% of all plastic products are made via injection molding, showcasing the process's significance in modern manufacturing.
Despite their long history, casting and molding have not stagnated. Technological advancements have enhanced the precision and scale of these processes, notably when using computer-aided design (CAD) software. This allows intricate details to be built into molds with minimal error, drastically improving efficiency and reducing production time. Statistically, 3D printing technologies, which are a form of additive manufacturing, are also transforming traditional methods by allowing for faster prototype development and adjustments.
In fact, according to a recent analysis by the International Journal of Advanced Manufacturing Technology, the integration of 3D printing with casting processes can reduce production costs by up to 25%. This synergy demonstrates how traditional expertise blends with cutting-edge innovation. A critical component of successful casting and molding is the quality of the mold itself. Mahatma Gandhi's famous words,
"The best way to find yourself is to lose yourself in the service of others,"reminds us of the unseen efforts of mold makers who ensure precision in every cast object.
In considering government policies and schemes, several programs offer financial assistance and tax benefits for those investing in modern molding technologies. Entrepreneurs focusing on environmentally friendly practices see even more support, as seen in various sustainable manufacturing initiatives. The constant evolution in casting and molding not only reveals the extensive reliance on these processes but also highlights the opportunities for innovation, aligning with government motives to promote sustainable and efficient manufacturing practices. By understanding and investing in these core methods, businesses can maintain a competitive edge while adhering to environmental and economic objectives.
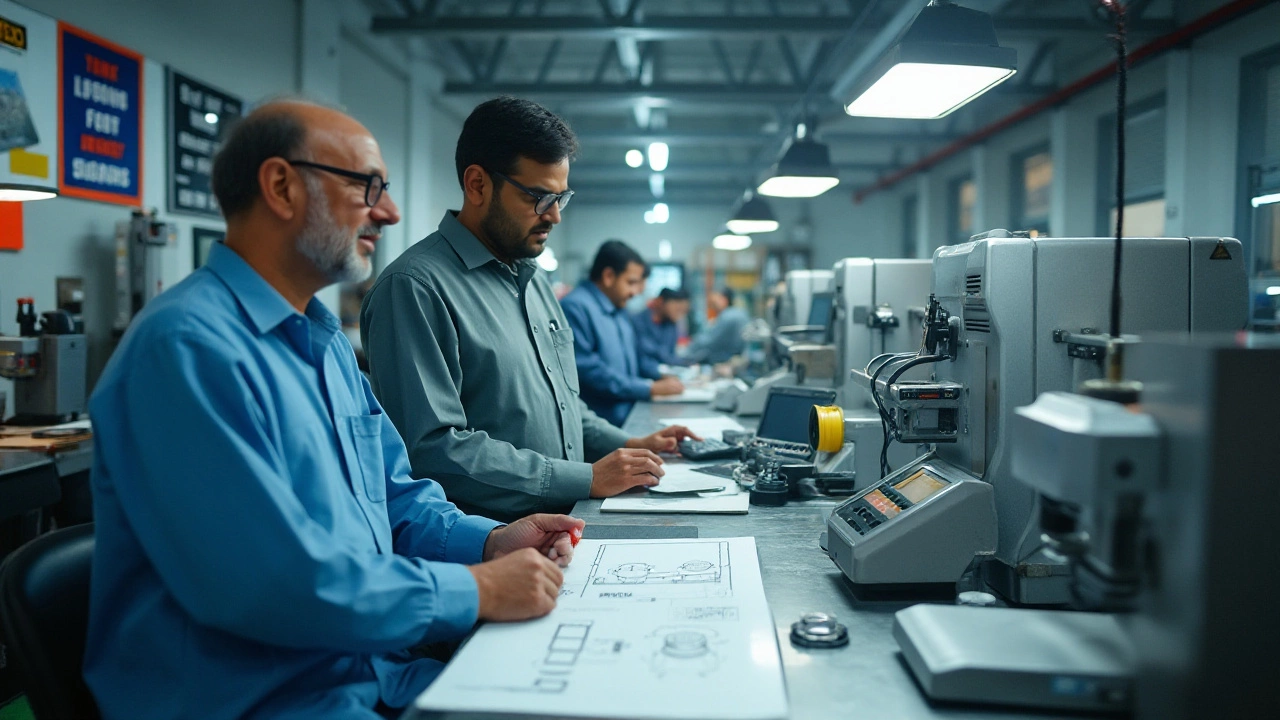
Machining Techniques
Machining techniques have been the cornerstone of precision manufacturing for centuries, shaping raw materials into finely crafted components that power industries worldwide. Whether it's a small pin for a watch or a massive gear for an industrial machine, the relevance of these techniques is indispensable. The scope of machining techniques encompasses various methods—including turning, milling, drilling, and grinding—each with its unique applications and strengths. The evolution of CNC (Computer Numerical Control) machines has transformed traditional machining, providing a level of precision that manual methods simply cannot match. With these systems, operators can create intricate patterns and complex parts, pushing the boundaries of what's possible in manufacturing.
Historically, machining has required a skilled hand and a nuanced understanding of the materials being worked with. Today, this expertise is complemented by digital technology, which has made the process more accessible yet no less specialized. Yet, challenges remain; machinists must often consider factors such as material hardness, heat resistance, and tool wear to ensure that components not only fit but function properly under demanding conditions.
The relationship between machining techniques and government schemes is also worth noting. Recognizing the importance of precision engineering in the economy, many countries offer grants and subsidies to encourage technological upgrades and workforce training within the machining sector. This support ensures that manufacturers can afford state-of-the-art equipment and skilled workers, translating into high-quality outputs and competitive exports. A report from the National Institute for Metalworking Skills illustrates this by noting that investments in machining technologies have led to a 25% increase in production efficiency across industries.
An esteemed industry source once stated, "In the realm of manufacturing, precision is not a luxury but a necessity. Machining techniques allow us to achieve the precision our era demands."
Another critical aspect of machining techniques is the implementation of lean manufacturing principles. Lean methodologies aim to minimize waste without sacrificing productivity, creating a more sustainable manufacturing process. In practice, this involves streamlining workflows, reducing idle time, and optimizing tool utilization. Many workshops adopting lean manufacturing techniques report significantly reduced production times and material wastage, emphasizing how critical these strategies are to modern manufacturing.
Innovations such as additive manufacturing, often seen as the future of the industry, are complementing traditional machining techniques. While traditional machining is subtractive—removing material to shape an object—additive processes build objects layer by layer. This combination of traditional and modern methodologies opens up myriad possibilities for designers and engineers alike, who can now explore complex geometries that would have been impossible to machine directly.
A closer look at machining's economic impact reveals impressive figures, bolstered by government support. It's estimated that this sector alone contributes billions to national economies across the globe, supported by advanced machinery and expert craftsmanship. The investment in these technologies underlines a commitment to maintaining a competitive edge in the rapidly evolving global market.
Joining Processes
Joining processes are essential manufacturing steps that help in creating complex assemblies from simpler individual parts. These processes are crucial because they allow manufacturers to construct larger and more intricate products through the combination of smaller components. The ability to accurately and effectively create these assemblies is incredibly important, especially in industries such as automotive, aerospace, and construction. Various techniques fall under the category of joining, each with its own characteristics, benefits, and applications. Machining Techniques often lead into joining processes, connecting intricate machined parts.
One of the most prevalent joining processes is welding, which utilizes heat to fuse materials together, typically metals or thermoplastics. From traditional methods such as arc welding and gas metal arc welding (GMAW) to advanced techniques like laser welding, the diversity in welding is wide. Precision and skill are crucial, as the strength and integrity of the joint largely determine the overall quality of the product. Welding isn't the only form of joining, though. Soldering and brazing serve similar functions, particularly in electronics and small-scale assemblies, by using a filler metal to bond parts without melting the base materials.
Beyond thermal methods, mechanical fastening remains a vital option, using components like screws, bolts, rivets, and clips. It's favored for its ability to be undone, making repairs and adjustments feasible. Techniques like adhesive bonding have also gained popularity, especially in sectors requiring even weight distribution and a clean finish. Here, specialized industrial adhesives are employed, which can offer advantages in terms of flexibility and vibration resistance. Each of these methods can complement production techniques, enhancing the durability and reliability of the final product.
Key Considerations and Advancements
Key considerations in joining processes include the choice of materials, environmental conditions, and desired outcomes, as each method brings its own set of challenges. Advanced techniques like friction stir welding have emerged, which operate under relatively low temperatures to ensure minimal distortion, especially when working with lightweight alloys and composites. This process has been crucial in aerospace manufacturing, contributing significantly to efficiency and safety.
"The significance of efficient joining processes cannot be understated. With innovation, industries can push the boundaries of what is possible." — Manufacturing Tomorrow Magazine
Furthermore, automation is increasingly prevalent in joining processes. Robots are adept at performing repetitive and precise tasks, reducing human error and improving consistency. Vision systems now guide robotic arms to ensure perfect placement. This level of automation not only enhances productivity but also ensures that human workers can focus on more complex tasks, integrating human creativity with mechanical precision.
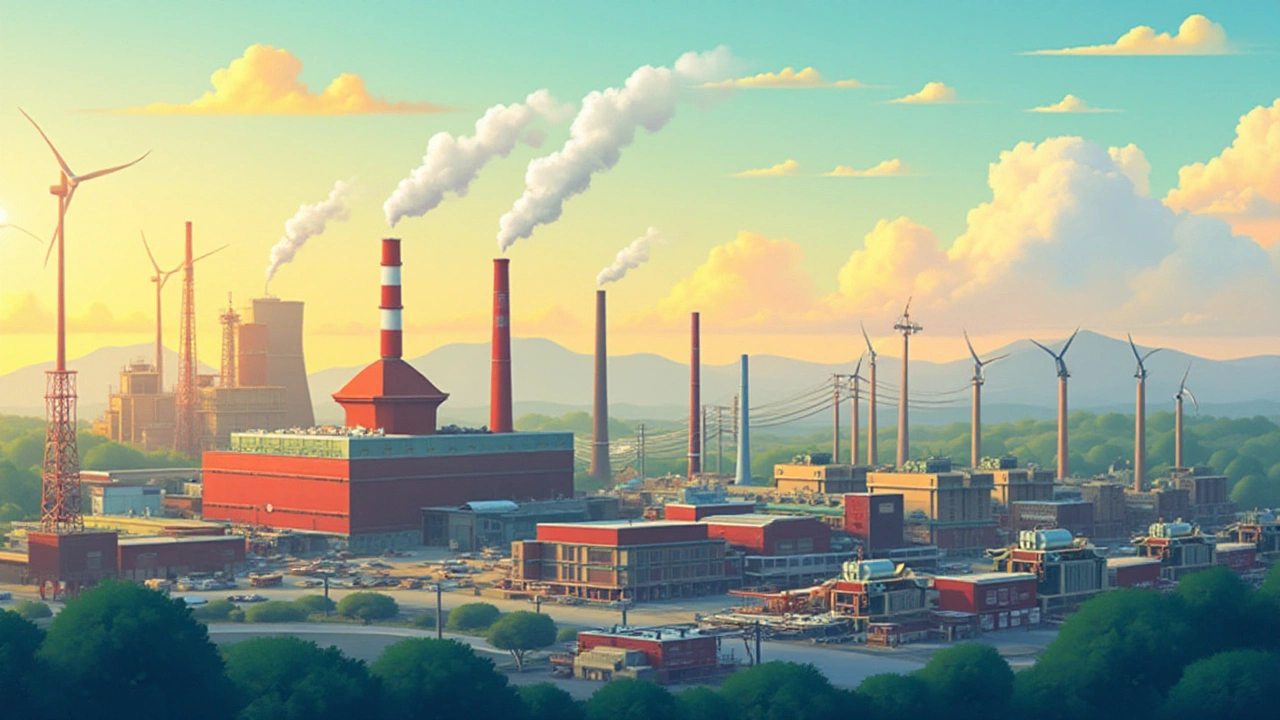
Shearing and Forming
Shearing and forming are pivotal in the world of manufacturing processes, instituting the transformation of materials into serviceable parts with remarkable precision and efficiency. The shearing process involves cutting materials, usually metal, without forming chips, using burning or melting techniques. The beauty of shearing lies in its simplicity—blade against blade, shearing is akin to cutting paper with scissors, where the blades are the tools, and the paper is the material being processed. This method is often employed in situations requiring straight cuts in sheet metal. A well-known advantage of shearing is the clean edge finish it delivers, minimizing the need for additional processing.
Forming, on the other hand, is all about shaping metal without any removal of material. This process can include multiple techniques such as bending, drawing, or stretching. The aim is to deform the material plastically and into the desired shape while maintaining its integrity. It is involved in creating everything from simple brackets to complex automotive bodies. The diversity of forming processes allows for a wide application across different industries, each requiring specifications tailored to their needs. A compelling aspect of forming processes is the ability to batch produce identical components, thus enhancing efficiency and consistency. It's fascinating to note that forming processes date back thousands of years, evolving remarkably alongside technological advancements.
"Effective shearing and forming processes are both the cornerstone of modern manufacturing and the continuous pursuit of efficiency." - Manufacturing Today
To delve deeper, shearing is a crucial step in preparing metal sheets for further fabrication, offering capacities that can range from thin foil to hefty plate thicknesses. The intricacies of the shearing process demand particular attention to blade sharpness and the clearance between them. Proper maintenance and adjustment ensure that the edges remain smooth and require little to no extra finishing. In contrast, forming demands a careful orchestration of force and geometry. The springback effect, a challenge in forming, occurs when metal tries to return to its original shape after being bent. Engineers have to meticulously calculate and sometimes overbend materials to achieve the precise angles required. This careful balance underscores the sophistication required in forming techniques.
The Role of Technology in Shearing and Forming
In recent years, technology has turbocharged these traditional techniques, introducing automated systems and precision instruments. CNC machines have revolutionized how forming is perceived, allowing operators to input designs digitally and produce outcomes with minimal manual intervention. The sure-handedness and uniformity provided by such technologies are unmatched, reducing error margins substantially. These advancements tie into the broader government schemes promoting innovation within the manufacturing sector. Initiatives aimed at integrating smart technologies into traditional processes receive special attention, primarily because of the potential to increase productivity and reduce wastage, aligning with sustainability goals. Importantly, knowing methods like shearing and forming are not just technological feats—they are integral to understanding modern production techniques, modified continually to improve output and product quality.
Government Schemes and Support
In the dynamic world of manufacturing processes, government schemes provide invaluable support. These schemes are designed not only to foster innovation but also to maintain the viability of numerous industries. It's crucial to appreciate the role these programs play in shaping industrial sectors, helping them stay competitive amidst ever-evolving global standards.
One notable scheme is the "Make in India" initiative. Launched by the Indian government, it is a powerful campaign aimed to encourage companies to manufacture their products in India. The focus is to create a conducive environment for investment and transform India into a global manufacturing hub. This initiative significantly impacts production techniques by providing financial assistance, tax benefits, and skill development programs. As Prime Minister Narendra Modi once emphasized,
"Make in India is not a slogan. It is a commitment for India to become the world’s most preferred manufacturing destination."
Similarly, in the United States, the Advanced Manufacturing Partnership was an initiative embraced by both the public and private sectors. It brought together industry leaders, universities, and federal agencies to accelerate innovation in manufacturing through technology development. By fostering collaboration between major stakeholders, such programs enhance capabilities across various industrial support networks. Increased investment in research and development ensures that industries adopt cutting-edge and sustainable manufacturing techniques.
In addition to direct financial policies, governments have enacted legislations that impact manufacturing processes. For instance, environmental regulations ensure compliance with sustainable practices, encouraging eco-friendly innovations. Many governments offer tax credits or grants to businesses that implement green technologies in their production lines. This approach not only improves environmental footprint but also aligns with consumer demand for responsible manufacturing.
Such governmental measures underscore how policies balance economic growth with sustainability. In regions like the European Union, initiatives such as the Ecodesign Directive enforce minimum environmental criteria for products. These laws stimulate industrial support, as industries constantly seek to innovate and differentiate in a market that values sustainability.
New programs continue to emerge, aiming to prepare industries for future challenges. With the rise of digital manufacturing and Industry 4.0, governments globally are investing in smart technologies. They support initiatives for automation and Artificial Intelligence, crucial for modernizing production techniques to meet demands efficiently and effectively.
While traditional grants continue, a shift towards fostering a well-skilled workforce is evident. Education and training programs stand at the core of numerous ongoing and upcoming government schemes. By investing in human capital, these programs not only bridge skills gaps but also ensure industries have the ability to adapt new technologies and remain competitive in the global market.