In the world of manufacturing, success lies in mastering a series of essential steps that transform an idea into a tangible product. For aspiring entrepreneurs in this field, understanding these stages can be a game-changer. Whether you're entering the market with an innovative gadget or a classic consumer product, each phase in the manufacturing process holds its own significance and challenges.
It's not just about great ideas; it's equally about precise planning, smart sourcing, and meticulous production. From that first spark of creativity to seeing your product on store shelves, the manufacturing journey is a complex dance of design, production, and delivery. So, as you ponder stepping into this exciting field, let's delve into these seven fundamental steps that build the backbone of any successful manufacturing startup.
- Ideation and Concept Development
- Design and Prototyping
- Sourcing and Material Procurement
- Production and Assembly
- Quality Control and Testing
- Packaging and Distribution
Ideation and Concept Development
The journey of manufacturing begins with a spark of creativity, often referred to as the ideation phase. It's during this stage that inventors and entrepreneurs imagine possibilities and let their minds roam in search of innovative solutions. This phase is crucial as it sets the foundation for the entire manufacturing process. It's where the impossible becomes possible in the mind of a visionary. Ideas may come from identifying a gap in the market or from a novel insight into an existing product. Startups must focus on aligning their ideas with market needs and demands, which can be identified through comprehensive research and trend analysis.
Once an idea is conceived, the concept development phase takes over. This is where the idea is fine-tuned and transformed into a viable product concept. Entrepreneurs delve deeper, challenging themselves to think about the product's functionality, design, and user experience. During concept development, it's essential to create a clear vision of what the product aims to achieve and how it stands out among competitors. Market research, competitive analysis, and identifying target demographics play pivotal roles. A well-defined concept serves as the roadmap that guides the following steps in the manufacturing process, ensuring every detail is considered before moving forward.
At this stage, working with a team of skilled individuals who can contribute diverse perspectives is often beneficial. Prototype models and sketches can be created to visualize the idea more tangibly. This creative collaboration can lead to unexpected innovations and improved concepts. It's not uncommon for ideas to undergo significant transformations during this period, refining and honing them to perfection. As Thomas Edison, a master inventor, once remarked,
“The value of an idea lies in the using of it.”This quote encapsulates the essence of this early stage, emphasizing the importance of practical and actionable ideas.
Engaging with potential users or gathering insights from focus groups can provide critical feedback and validate the idea's feasibility. Feedback is instrumental in identifying potential flaws or areas for enhancement before significant resources are committed. The ability to adapt and iterate at this stage is essential for long-term success. Moreover, open dialogues with industry experts and mentors can offer valuable counsel and avoid common pitfalls. It's all about crafting a product concept that not only meets consumer expectations but exceeds them, leveraging the unique advantages offered by the startup's vision and capabilities.
The ideation and concept development phase culminates in the creation of a detailed product blueprint or plan. This document serves as a comprehensive guide outlining every critical aspect of the product, including features, specifications, and intended use. By this point, the startup should have a clear understanding of the project's scope and the resources needed to bring the concept to life. The brilliance of ideation and concept development lies in its ability to transform abstract thoughts into concrete plans that pave the way for the next steps in the manufacturing process.
Design and Prototyping
Diving into the design and prototyping phase is where the raw excitement of turning ideas into reality begins to unfurl. This stage stands as a pivotal point in the manufacturing process, bridging the gap between your conceptual vision and its tangible form. At its core, successful design involves more than just aesthetic allure; it must harmonize function, form, and manufacturability. An evolution from sketches to 3D models, this process establishes the foundation upon which all subsequent manufacturing steps are built, making it crucial for budding manufacturing startups.
Before you move forward with production, creating a prototype allows for practical assessment in a real-world context. Think of it as a sneak peek into the future of your product. It lets you test different materials and processes to evaluate the efficiency of the design, offering insights that might not be apparent during initial design stages. Circling back to design adjustments post-prototyping can often save considerable time and costs, preventing later stage mishaps. Visiting companies frequently iterate numerous prototypes before settling on a final design. This validates one brilliant concept: if the design isn't working, be ready to pivot.
As creativity flourishes in the design lab, software plays an indispensable role. CAD software, such as SolidWorks or AutoCAD, has revolutionized the way prototypes are envisioned. With these tools, teams can simulate and analyze designs against a comprehensive set of parameters before any physical resources are expended. Moreover, rapid prototyping technologies like 3D printing have accelerated the prototyping phase by offering a cheaper, faster means of converting digital models into physical forms. According to a survey by Siemens, such technologies can reduce prototyping time by nearly 90% in some industries.
Understanding the customer's perspective during the prototyping phase can also drive significant improvements. Feedback from potential users leads to better-designed products. Open channels for consumer insights can be invaluable, sometimes highlighting unexpected design flaws or opportunities. An industry leader once aptly stated,
"Good design should never be a monologue; it must be a conversation."This iterative feedback loop ensures that consumer needs and expectations align harmoniously with design objectives.
The investment in thorough design and prototyping work is an investment in your startup's resilience. Addressing issues at this phase, whether related to materials, functionality, or user interaction, fortifies the product's viability. Skimping here could lead to costly revisions later in the manufacturing process or, worse, a failed product launch. As you mold your concept into a prototype, keep the end goal in mind: a functional and appealing product ready for the production phase and eventual market success.
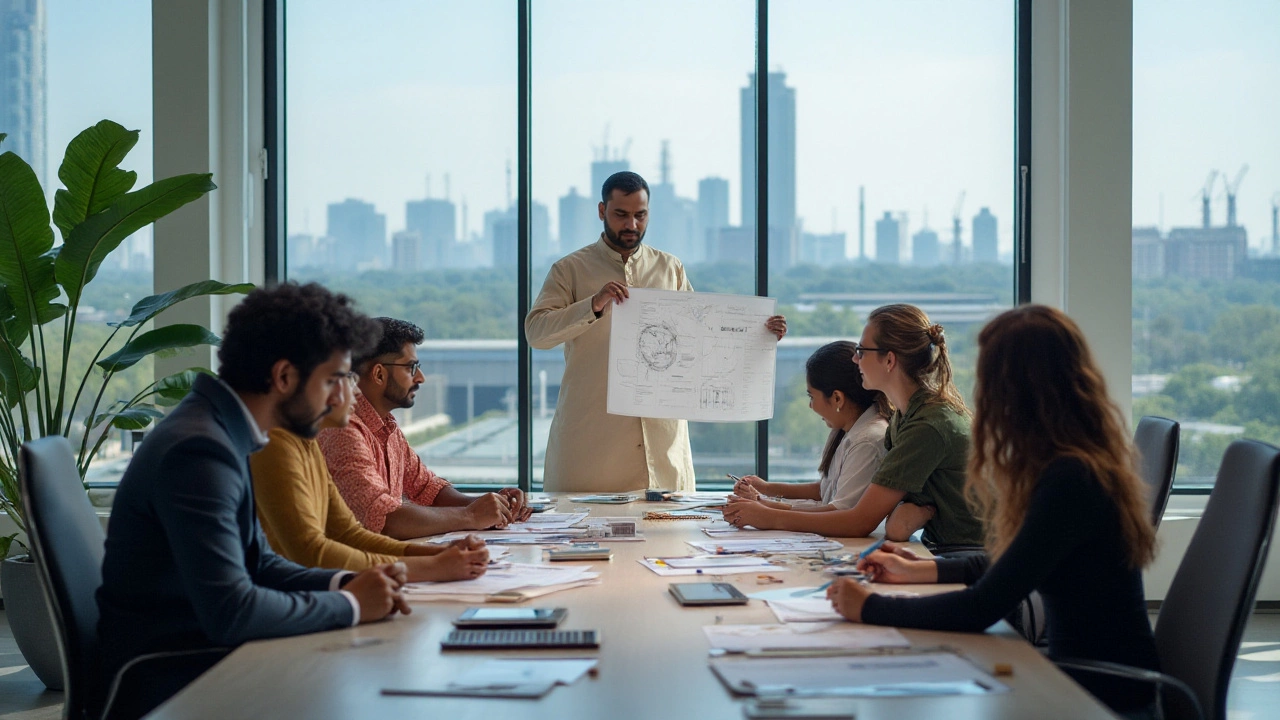
Sourcing and Material Procurement
In the dynamic landscape of manufacturing, the step of sourcing and material procurement often sets the tone for the rest of the production process. Ensuring that you get top-quality materials at competitive prices while maintaining ethical standards is often the backbone of any thriving manufacturing business. Selecting the right vendors and partners can markedly influence not just the cost, but also the reputation of your brand. A critical and strategic first step is crafting a comprehensive procurement strategy. Knowing exactly what materials are needed, the potential suppliers, pricing structures, quality control measures, and delivery timelines can significantly streamline operations and save up on unforeseen expenses down the line. Often grounded in research, this involves an exhaustive study about available suppliers, both local and international, as well as understanding the market demand and supply volatilities.
Once you’ve listed potential suppliers, moving on to vendor assessment is key. This evaluation should focus on quality, reliability, consistency, and the supplier's ability to meet deadlines. Several manufacturers, like the well-respected Robert Bosch GmbH, emphasize a balanced scorecard approach. This method allows you to rate suppliers not only on financial aspects but also, on quality, trustworthiness, and innovation. Establishing strong relationships with suppliers can lead to long-term partnerships, yielding benefits such as preferable terms, early product updates, and sometimes an open line for constructive feedback. Furthermore, pondering the source of materials raises ethical considerations. The rising trend in consumer awareness about environmentally friendly and ethically produced products might influence your decision in favor of suppliers who align with these values. A noted industry shift towards sustainability and social responsibility has prompted many in the sector to reevaluate their supply chains, ensuring transparency and adherence to fair trade practices.
With global supply chains becoming more intricate, businesses should aim to diversify to mitigate risks. This can mean maintaining a roster of backup suppliers or even considering dual sourcing strategies - procuring the same material from different geographical sources. While this approach might come with its own complexities, it can be a lifesaver in times of geopolitical tensions or unexpected natural events that affect worldwide logistics. Furthermore, technology today offers powerful tools for procurement. With advancements such as AI-driven forecasting and supply chain management software, manufacturers can better predict material demands and streamline procurement processes. Tools like SAP Ariba enable businesses to manage everything from source to settlement, thus reducing manual workload and minimizing human error.
"Technology plays a pivotal role in transforming procurement. Efficient data management can be the difference maker," suggests Thomas W. Derry, CEO of the Institute for Supply Management.
Finally, it's crucial to emphasize that while securing the right materials might appear daunting, it's at heart an evolving dance of maintaining quality and ensuring cost-effectiveness. As market dynamics shift unabatedly, evolving procurement strategies can usher in substantial benefits, positioning manufacturing startups not just as players, but as leaders in their field. Whether you're new to this avenue or an experienced manufacturer, embracing the complexities of sourcing with innovative thinking and a strategic mindset can propel your venture far beyond its starting blocks.
Production and Assembly
Production and assembly are the bustling heart of manufacturing, where all planning comes to fruition as raw materials are transformed into finished products ready to meet the demands of the market. This stage is both a science and an art, involving precision engineering and a deep understanding of the production line's subtleties. The rhythm of the assembly line depends greatly on efficiency, with small errors having the potential to lead to significant downtime or defects. Manufacturers aiming for success recognize the value of a well-organized production process. A smoothly running operation not only saves time and money but also contributes to delivering high-quality products consistently.
For startups, setting up a production line can be daunting. It's not just about having the right machinery; it's equally about training a skilled workforce capable of operating and maintaining those machines effectively. Many seasoned manufacturers suggest starting small, investing in scalable technologies that can grow alongside your business. As Henry Ford, a pioneer of modern manufacturing, once said, "Coming together is a beginning, staying together is progress, and working together is success."
Efficiency in production is not just about machines but also how seamlessly humans and technology can work together.
Another critical aspect of this process is maintaining strict quality standards. During assembly, checks and balances must be in place to catch defects before they move further down the line. Statistical Process Control (SPC) is a widely-used method, where real-time data is collected to monitor production performance closely. According to the American Society for Quality, implementing SPC can reduce production defects by up to 50%. This data-driven approach ensures that deviations from the norm are detected early, preventing costly mistakes and maintaining a reputation for quality.
Modern manufacturing also increasingly embraces automation, adding robots and AI to the mix. The International Federation of Robotics reported that the global stock of industrial robots reached approximately 3 million operational units by 2022, demonstrating a growing trend towards automated processes. Companies that leverage automation can achieve higher throughput rates and consistent product quality. However, the introduction of such technology requires careful strategic planning. It's not always about replacing human labor; instead, it's about augmenting human capabilities to enhance productivity and reduce errors.
The assembly part of production is where individual parts come together to form a complete product. For many, this involves implementing lean manufacturing principles, where waste is minimized, and every step in the process adds value. Lean techniques such as the 5S methodology or Just-In-Time (JIT) production help remove inefficiencies, streamline production, and respond swiftly to changing consumer demands. Embracing lean practices can drastically reduce lead times, enabling quicker response to market trends and customer requests.
In conclusion, the production and assembly stage is not just a mechanical process; it's a complex interplay of strategy, human skill, machinery, and technology. Mastering this stage sets a solid foundation for creating reliable, high-quality products. By balancing efficiency, quality control, and adaptability, manufacturers can thrive in the competitive landscape of modern industry. Ultimately, successful production isn't marked by the absence of challenges but by the ability to address them effectively and persistently source innovative solutions.
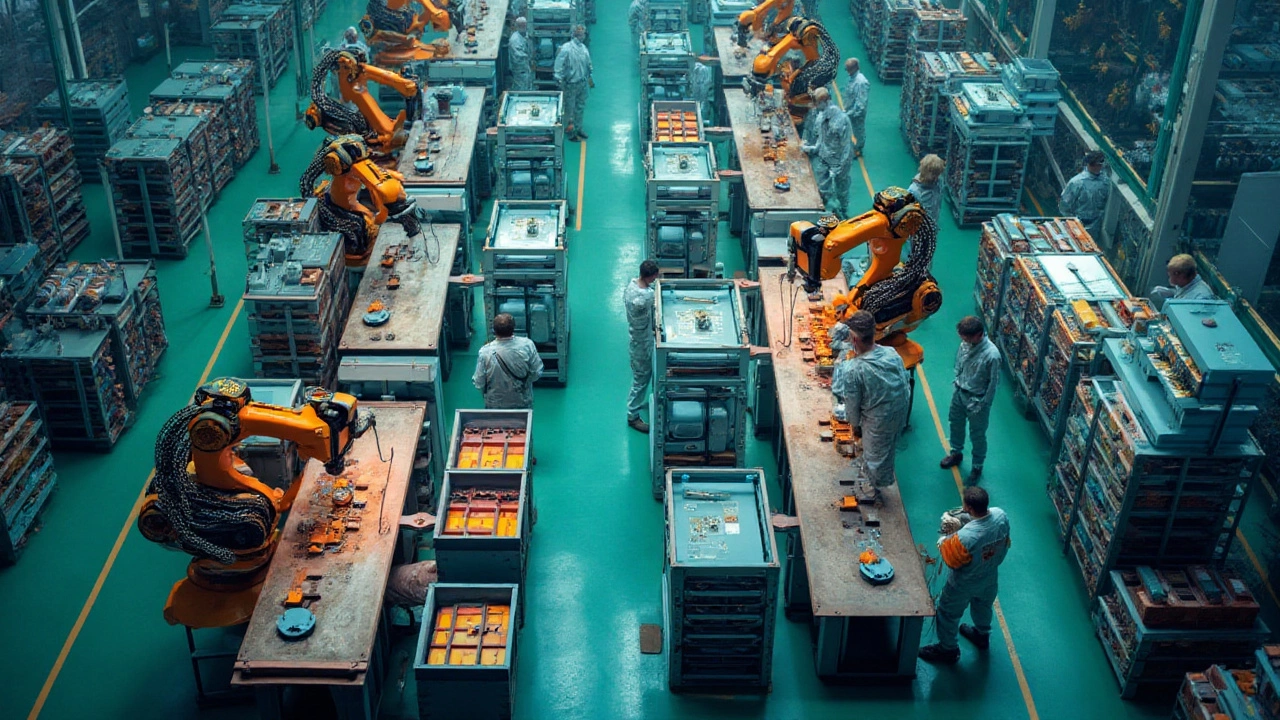
Quality Control and Testing
Quality control and testing are critical components in the manufacturing process, responsible for ensuring that every product meets established standards and functions as intended. The aim is to deliver a defect-free product that delights the customer and builds a reputation for reliability and excellence. Implementing effective quality control starts with setting clear quality benchmarks derived from customer expectations and industry standards. Collecting feedback and studying competitors can also offer insights into these benchmarks. Once standards are set, it's crucial to develop robust testing procedures that systematically evaluate product quality at various stages of production.
Testing methods vary depending on the product. Mechanical products, for example, may require stress testing to ensure durability under different conditions, while electronics need electrical testing to confirm operational functionality. Employing various tests like visual inspections, simulations, or using specialized equipment can help identify defects early, saving time and cost. Inspection checkpoints should be positioned strategically within the production process to catch issues as early as possible, preventing defective products from reaching later stages where cost and waste increase significantly.
To guide the quality control staff and streamline the process, maintaining detailed documentation of procedures is essential. This not only ensures consistency in quality checks across production batches but also helps in refining processes based on past performance. It’s often said that "Quality is not an act, it is a habit," as famously quoted by Aristotle. This habit becomes ingrained in manufacturing culture through rigorous training and continuous improvement programs aimed at education and motivation. These programs equip employees with the knowledge and skills necessary to uphold quality standards and effectively use testing equipment and technology.
In today’s data-driven world, the integration of technology such as AI and IoT in quality control can significantly enhance the precision and efficiency of testing. With IoT-enabled devices, real-time monitoring can be conducted remotely, allowing instant detection of deviations from specified standards. Doing so not only ensures consistency but also significantly reduces the manual labor associated with quality assurance, optimizing the entire production workflow. Such advancements encourage a proactive approach, identifying anomalies even before they cause bigger issues.
"Quality means doing it right when no one is looking," said Henry Ford. This mindset entails a commitment to excellence at every phase, demanding accountability and encouraging innovation. Quality control is not merely about catching flaws; it involves a continuous review cycle aimed at product improvement. Engaging in regular audits and adopting feedback loops from consumers as well as internal teams creates a dynamic framework where each iteration leads to betterment in product quality.
Companies dedicated to excellence often invest in certifications and audits to demonstrate their adherence to industry standards. Certifications such as ISO 9001 provide a structured approach to quality management and can bolster a startup's credibility in a competitive market. With the increasing emphasis on sustainability, quality control now also considers environmental impacts, ensuring that manufacturing processes are not only efficient but also environmentally responsible. Such comprehensive steps instill confidence in consumers and can differentiate a product in a crowded marketplace, ensuring the long-term success of a manufacturing startup.
Packaging and Distribution
Packaging serves as the first impression your product makes on a customer, ultimately setting the tone for their entire experience. It's where form meets function, and in many ways, dictates the perceived value of the product. For a manufacturing startup, packaging isn’t just about aesthetics; it’s about protecting the product, optimizing space for shipping, and ensuring sustainability standards are met—an increasingly important factor for environmentally-conscious consumers. A well-designed package not only safeguards the product during transit but also communicates vital information and enforces brand identity. The choice of materials, colors, and design elements such as logos and labels are crucial. It's imperative to balance cost-effectiveness with quality, making sure the packaging aligns with the brand's ethos and appeals to the target market. In fact, studies suggest that 72% of consumers purchase products based on packaging alone, underscoring its importance in the purchasing decision.
Interestingly, distribution is as vital as any other step in the manufacturing process. The journey from factory to marketplace encompasses various logistical elements that need strategic planning. Choices in distribution channels can make or break a business—selecting between direct-to-consumer, wholesalers, or e-commerce platforms, for instance, requires thoughtful analysis of the intended market and product type. Efficient distribution is about managing supply chains, minimizing delays, and controlling costs without compromising the quality and timely delivery. “Efficient distribution can reduce a company's overall logistics cost by up to 12%,” says logistics expert John Smith of the Global Logistics Institute, highlighting its significance. With the rise of technology, distribution strategies continue to evolve, embracing innovations such as drone delivery and automated warehousing systems, potentially transforming the speed and reliability of deliveries.
Once your product is packaged and ready for the consumer, the next step is to examine distribution efficiency. An emerging trend is the shift toward sustainable distribution practices. Using energy-efficient transport options or aligning with green shipping partners not only supports environmental goals but also attracts eco-conscious customers. Businesses are also leveraging technology to streamline distribution. Advanced software for inventory management, tracking systems, and AI-driven logistics planning tools are paving the way for smarter, more intuitive distribution networks. For startups, choosing the right technological partner can be a defining factor in scaling the business efficiently. Thus, while the journey of a product from creation to consumer may seem daunting, it's these strategic initiatives that ensure not only survival but success in the competitive marketplace.