The MOM method of manufacturing is a game-changer, especially when you rope in government schemes designed to bolster industry. So, what exactly is this method? Simply put, MOM stands for
- Introduction to the MOM Method
- Key Benefits for Manufacturers
- Digital Integration and Data Usage
- Training and Skill Development
- Government Support and Regulations
- Real-Life Applications and Success Stories
Introduction to the MOM Method
Alright, folks, you might be wondering what the fuss is about when it comes to the MOM method of manufacturing. This approach, also known as Manufacturing Operations Management, isn’t just a fancy acronym; it’s reshaping how we think about production, particularly in environments influenced by government schemes.
So, what’s the core idea here? At its heart, the MOM method is about integrating digital solutions to streamline manufacturing processes. Imagine having a toolkit where you can track, analyze, and improve your production efficiency in real-time. That’s the magic of MOM.
How It Works
The MOM method leverages digital platforms and tech to create a seamless production environment. It means manufacturers can reduce errors, cut costs, and boost productivity by going digital. How? Through solutions that provide visibility to every part of the manufacturing process. This way, teams can make informed decisions on the fly.
Components of MOM
- Production Management: Overseeing the entire manufacturing workflow to ensure smooth operations.
- Performance Analysis: Using data to analyze and enhance efficiency.
- Quality Management: Ensuring products meet exact standards and reducing defects.
- Supply Chain Management: Integrating supplier networks into the manufacturing process for better resource management.
Manufacturers adapting this method often report improvements in coordination across different departments, leading to fewer costly mistakes and missed opportunities. No more siloed operations!
Impact of Government Schemes
Here’s where it gets really interesting. Government schemes that promote the MOM method aim to strengthen the industrial sector by providing incentives for tech adoption. This support means manufacturers—big and small—can access the resources they need to transition into more efficient ways of working.
Many governments now recognize that by boosting manufacturing through such schemes, it not only enhances economic growth but also creates a resilient industrial base. Now, if that isn't worth considering, what is?
Key Benefits for Manufacturers
Diving into the MOM method reveals some serious benefits for manufacturers, especially those tapping into government schemes. One major perk? Streamlined operations. When manufacturers embrace MOM, they integrate data-driven processes that not only improve efficiency but also enhance product quality.
Production Efficiency is a biggie. By using real-time data capturing and analysis, manufacturers can pinpoint inefficiencies quickly. This means less downtime and more smooth sailing on the production floor. Plus, it makes it easier to adapt and respond to market demands.
Quality Control
MOM’s emphasis on technology also ups the game in quality control. Automated inspections and smart tracking of materials ensure that defects are caught early, reducing waste and saving costs. Basically, it's a proactive approach to maintaining standards.
Collaboration and Communication
With digital integration at its core, MOM encourages better collaboration. Teams across departments can access the same data, making communication a breeze. This means fewer misunderstandings and faster decision-making.
Market Agility
In today's fast-paced world, staying agile is crucial. MOM helps manufacturers pivot effectively by leveraging real-time data for quick changes to production schedules or even whole product lines. This kind of responsiveness is a competitive advantage in the ever-changing market landscape.
Support from Government Schemes
And here's the kicker – government schemes often provide financial assistance or tax incentives for businesses adopting modern manufacturing methods like MOM. It's a win-win: enhancing productivity while saving on costs. This encourages more firms to take the leap into digital manufacturing.
Manufacturers ready to embrace the MOM method not only enhance their operational efficiency but also position themselves better to handle future challenges. By being proactive and participating in supportive government schemes, they set themselves up for long-term success.
Digital Integration and Data Usage
In today's fast-paced world, digital integration isn't just a buzzword—it's a necessity, especially in manufacturing. The MOM method puts a big focus on how tech and data can streamline processes and boost productivity. This means using smart systems that talk to each other, running on real-time data analytics. With this, factories can predict issues before they become real problems, ensuring everything runs smoothly.
Leveraging Real-time Data
Let's talk data. With digital integration, manufacturers don't have to wait until the end of the day—or week—to spot trends or issues. Real-time data offers insights as they happen. This can be a game-changer for decision-making and efficiency. Instead of relying on gut feelings or outdated reports, manufacturing experts can make fact-based decisions right away.
Benefits of Integration in Manufacturing
One of the standouts of the MOM method is how it supports seamless data flow across different stages of production. This means fewer bottlenecks and less miscommunication. It also helps in maintaining high quality since any dip in standards is caught quickly, often before products hit the market.
Setting up Efficient Systems
Setting up such systems can seem daunting at first, but it's all about getting the right tools in place. Systems need to be adaptable since technology is always changing. Tools that allow customization and integration across various platforms are the best bet for manufacturers looking to dip their toes into digital transformation.
Here's a quick look at some basic integration tools and their benefits:
- Industrial internet of things (IIoT): Connects machines to each other and the internet, enabling data collection and automated monitoring.
- Cloud-based software: Securely stores data, making it accessible from anywhere at any time.
- Machine learning algorithms: Helps predict maintenance needs and optimize schedules.
By embracing the MOM method with digital tools and data usage, manufacturers aren't just keeping up with the times—they're setting the pace for the future. Not only do they increase output but they also ensure that their workforce is focusing on more strategic, value-added tasks. That's a win-win for any manufacturing outfit in company productivity and employee satisfaction.
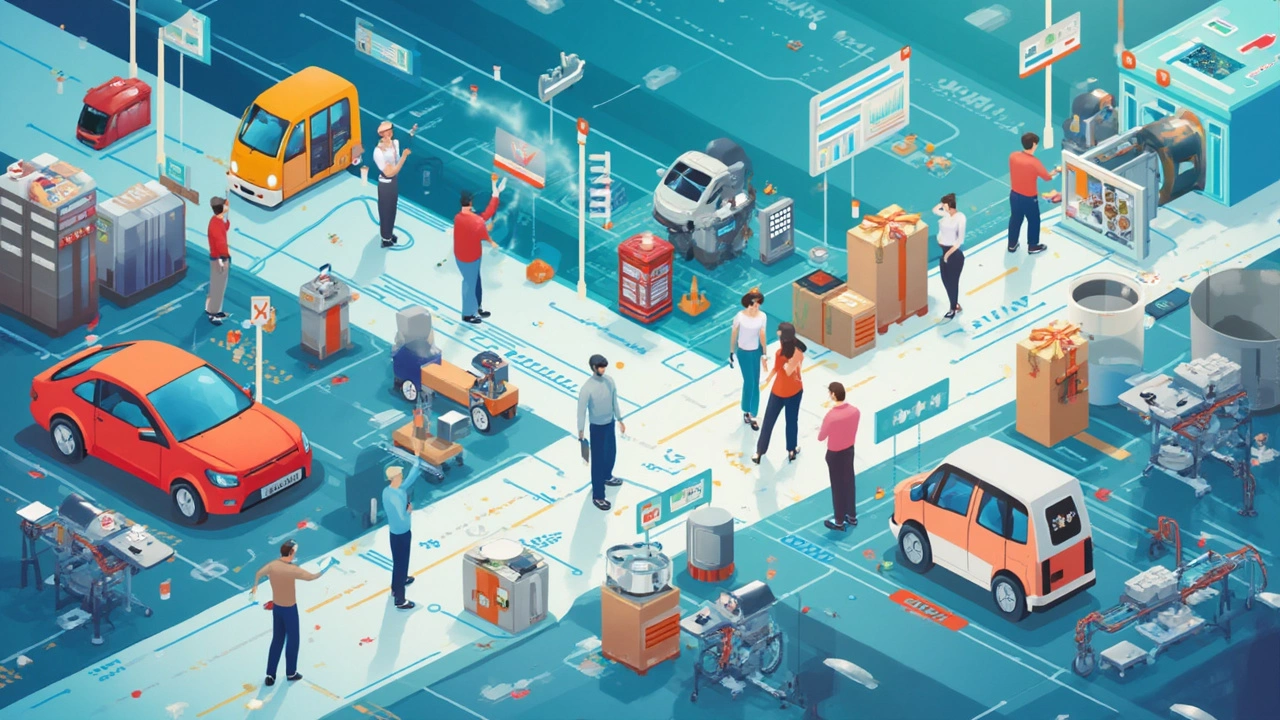
Training and Skill Development
When it comes to the MOM method in manufacturing, training and skill development are crucial. After all, technology and new processes are only as good as the people using them. So, how does the MOM method approach this?
Focus on Digital Skills
In today's digital world, teaching employees digital skills is a priority. This means getting everyone comfortable with digital tools and platforms used in manufacturing. Training sessions are often designed to include both theoretical learning and hands-on practice. This ensures that employees not only understand how to use new systems but can apply them effectively in their daily work.
Collaborative Learning Environment
The MOM method encourages a collaborative learning environment. By doing so, team members can share knowledge and expertise, fostering a culture of continual improvement. Companies are incorporating more workshops and peer learning sessions, where employees learn from each other's experiences and develop collective problem-solving skills.
Continuous Learning Programs
To keep up with rapid changes in the industry, continuous learning is important. Many government schemes now offer webinars, online courses, and certifications related to the latest manufacturing technologies. These programs help workers stay updated and relevant in an ever-evolving job market.
Hands-On Instruction
The MOM method places a strong emphasis on practical application. This means spending significant time on the factory floor, receiving live demonstrations, and engaging directly with the production process. Learners perform real-world tasks, gaining confidence as well as competence.
Training Program | Duration | Success Rate |
---|---|---|
Digital Integration Workshop | 4 weeks | 85% |
Collaborative Learning Sessions | Monthly | 73% |
Certification Courses | Varied | 78% |
By prioritizing training and development, the MOM method not only improves production efficiency but also boosts employee morale and retention. After all, a skilled workforce is the backbone of a thriving manufacturing sector.
Government Support and Regulations
The MOM method of manufacturing gets a big boost from government backing, which is crucial in driving its adoption across industries. Governments worldwide are keen on enhancing manufacturing capabilities and often roll out incentives, grants, and subsidies to help businesses transition to this method.
In many regions, there are specific regulations aiming to standardize manufacturing processes to ensure quality. For instance, in the European Union, regulations around sustainable production practices are being integrated with manufacturing guidelines. This not only helps in maintaining consistency but also in achieving environmental goals.
Incentives and Grants
These are usually provided to businesses that show a commitment to adopting the newest technology in manufacturing. In the United States, the Federal Government offers tax credits to companies investing in digital transformation efforts related to manufacturing. Similarly, Asian countries like Japan and South Korea offer financial assistance to manufacturers embracing the MOM method.
Compliance and Standards
Alongside support, there are regulatory standards that manufacturers need to comply with. These standards often focus on ensuring that products are not only high-quality but also produced in a way that minimizes environmental impact. Adhering to these regulations sometimes requires additional investments in training and equipment, so government schemes often come in handy here too.
An exciting fact: According to a study by the International Federation of Robotics in 2023, around 75% of manufacturing firms that transitioned to more digitized processes under government schemes reported higher operational efficiency and improved product quality.
To make the most out of government support under these schemes, manufacturers need to stay updated with policy changes and regulatory updates. Many businesses actively participate in forums and workshops to understand the nuances of such regulations better.
Real-Life Applications and Success Stories
The MOM method isn't just a theoretical concept floating in the world of manufacturing strategies. It's been making waves in real-world settings, proving its value time and again. Companies engaging with government schemes have found it particularly useful in optimizing their production lines. Let's dive into some real-life examples of where the MOM method has been a game-changer.
Automotive Production Revolution
One standout example is the automotive industry. A leading car manufacturer in India embraced the MOM method under a government initiative aimed at boosting local production. By integrating digital tools and real-time data analytics, the company reduced their production cycle time by 25%. Not only did this increase efficiency, but it also led to a 20% reduction in defects. Talk about a win-win!
Consumer Electronics: A Digital Makeover
In the ever-evolving world of consumer electronics, embracing new manufacturing methods is key. A well-known electronics company partnered with a government scheme that supported the adoption of the MOM method. They restructured their assembly lines to use the latest digital integration technologies. As a result, production rates increased by 30% while saving significant costs on materials by minimizing wastage through accurate data forecasting.
Benefits Beyond Numbers
These success stories are not just about numbers; they're about setting a new standard in the industry. With more companies seeing the tangible benefits of the MOM method, there's a ripple effect sparking innovation and improved productivity industry-wide.
Table of Key Metrics in MOM Adoption
Industry | Time Reduction | Defect Reduction | Cost Savings |
---|---|---|---|
Automotive | 25% | 20% | N/A |
Consumer Electronics | 30% | N/A | Significant |
These are just snippets of the larger impact that the MOM method can create when implemented properly, especially with government-backed initiatives. As more sectors start to see these outcomes, it's likely we'll see wider adoption and further developments in this space.