Grab any gadget or household item nearby—there’s a good chance it’s traveled halfway around the world, touched a few robots, and exchanged hands between dozens of companies before it landed with you. But manufacturing, which fuels nearly everything in our lives, is experiencing some major headaches lately. It’s not just about factories humming in the background. The deeper you look, the more you see a system creaking under its own weight, facing challenges from broken supply chains to angry environmentalists to anxious factory owners glued to economic news. Why does this matter? Because these manufacturing problems aren’t staying in the background. They lead to empty store shelves, higher prices, and even layoffs. Every time I drive by the old factory in our town that’s now an abandoned shell, I can’t help but think—something’s gone seriously wrong.
Squeezed by Supply Chains and Global Chaos
Remember when toilet paper vanished from stores or when car dealerships had more colorful balloons than vehicles? Supply chain mess is at the root of that. Manufacturing doesn’t happen in a vacuum. Parts and materials often come from one country, get assembled in another, then shipped halfway across the planet for you to use. Throw in a global pandemic, geo-political flare-ups like the Russia-Ukraine conflict, and wars in trade tariffs, and suddenly shipments go missing, factories run out of parts, and production slams to a halt.
Look at semiconductors—the tiny chips inside everything from your phone to your dishwasher. Due to pandemic factory shutdowns in Asia and booming demand, wait times for chips jumped from a healthy 12 weeks in 2020 to nearly 26 weeks by mid-2022, based on data from Susquehanna Financial Group. Ford and Toyota literally parked unfinished cars in empty lots for months, waiting for chips. Every time something jams up in one part of the chain, the pain spreads everywhere. Even shoe companies like Adidas faced delays of over three months for Vietnamese-made sneakers in 2021—taking a direct hit to their bottom line.
It’s not just missing parts. Shipping costs also soared wildly. Before 2020, it cost about $2,000 to ship a 40-foot container from Asia to the U.S. West Coast. After the chaos hit, prices spiked to almost $20,000 per container in September 2021, according to the Freightos Baltic Index. Small manufacturers got squeezed out and unexpected winners (like shipping giants) made record profits. But for businesses hoping for stability? Not happening.
So what's the lesson here? Manufacturing works great when everything is smooth. But with global supplies so tangled up, one little hiccup in a distant country can snowball into a full-blown crisis thousands of miles away. This fragility sits at the heart of why manufacturing is such a problem right now.
Item | Pre-COVID Cost/Lead Time | Pandemic Peak |
---|---|---|
Shipping 40-ft container Asia-USA | $2,000 | $20,000 |
Semiconductor chips (delivery time) | 12 weeks | 26 weeks |
Sneaker delivery delay (Adidas) | 4 weeks | 3+ months |
The Human Factor: Labor Shortages and Skills Gaps
Manufacturing used to be the ultimate dependable job. My uncle worked at the same auto plant in Chennai for 25 years. Folks like him kept the world moving. But now? Many factories can’t even find people willing to work, or lack workers trained for modern demands. It’s not just a local thing—it’s everywhere.
Here’s a reality check: In 2023, the U.S. National Association of Manufacturers reported some 800,000 manufacturing roles were unfilled. McKinsey predicts that by 2030, up to 2.1 million manufacturing jobs in the U.S. might remain open due to a lack of skilled workers. In India, a survey by the India Skills Report 2024 found only about 45% of job seekers had the skills that modern manufacturers require. Older workers retire, new tech arrives, and companies struggle teaching digital skills to existing employees. Who’s lining up to work on the factory line? Not as many as before.
Young people, too, look elsewhere—chasing IT or service jobs. Many see manufacturing as back-breaking or unsafe (some old images still stick, even if automation has made a difference). In places like Germany, which has long prized technical skills, they’re feeling the crunch as Baby Boomers retire and fewer people take up trades. Meanwhile, rising automation demands tech-savvy workers, but retraining doesn’t always keep up. It’s not unusual for smaller factories to use machines costing crores, but still rely on ‘Mukesh bhaiya’ who learned the ropes in the 1980s and is now months from retiring.
When manufacturers struggle to find skilled talent, production slows, mistakes rise, and companies delay new products. The ripple effect reaches all the way to consumers in the form of delays and higher prices. Solutions? Some put faith in automation and AI, but even robots need people to program, maintain, and repair them—more tech, less muscle. Until the training gap closes, don't expect this problem to vanish.
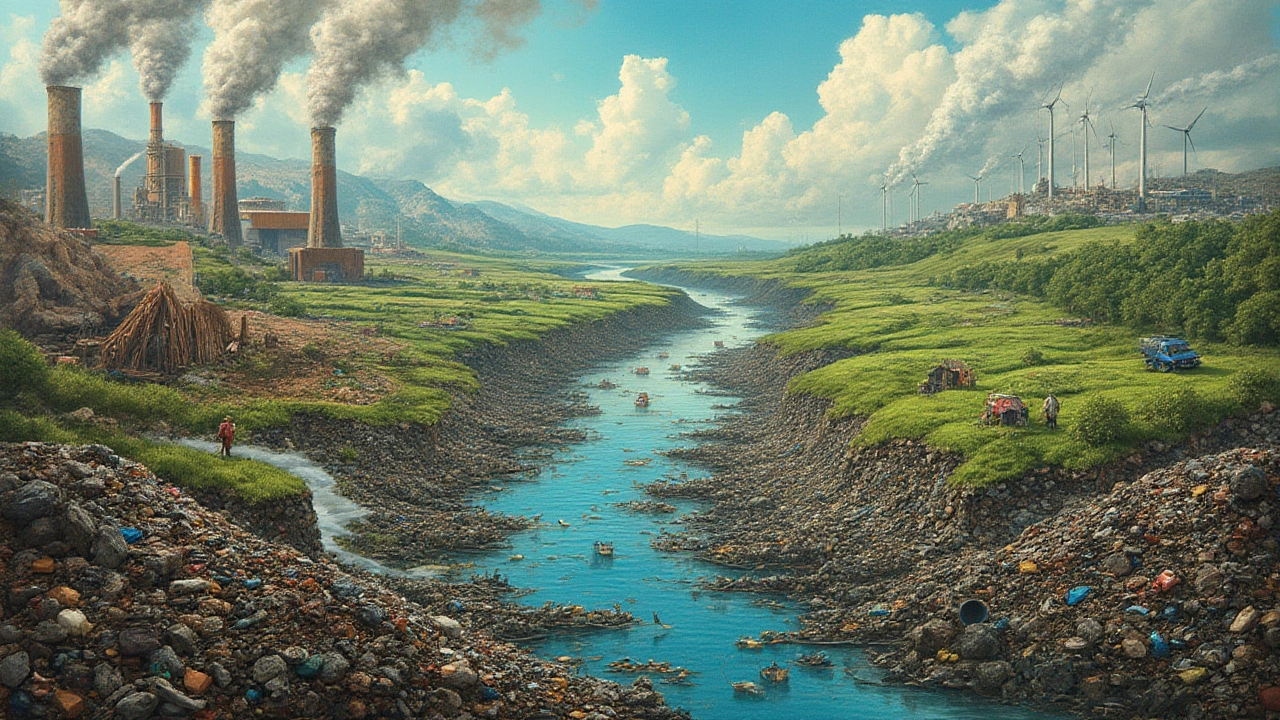
The Big Environmental Headache
If you think manufacturing just makes stuff, think again—it also makes mountains of waste, gulps down scary amounts of electricity, and pumps out carbon emissions like few other sectors. Big factories may look clean outside, but inside, the environmental impact is difficult to ignore.
Here’s a dirty secret: Manufacturing is responsible for nearly 30% of global greenhouse gas emissions, according to the International Energy Agency (IEA). Steel plants, cement factories, plastic manufacturing—these are massive polluters. One steel mill gives off as much CO2 as several million cars. Textile manufacturing, especially in places like Bangladesh and China, is notorious for dumping dye into rivers. In 2024, Greenpeace found that India’s textile clusters contributed heavy metals to half the major rivers studied in Gujarat. Even the phones in our pockets leave a toxic trail—mining rare minerals destroys land and pollutes water.
Regulations are toughening up. The European Union’s Carbon Border Adjustment Mechanism (CBAM), which started in 2023, slaps import taxes on high-carbon products like cement and steel. Suddenly, polluting factories lose their price edge. At the same time, brands face public pressure—watchdogs love posting viral photos of polluted rivers or sweatshops.
And yet, many manufacturers struggle to go green. Cleaner technologies can be expensive to install. Solar panels, waste treatment plants, or pollution controls take years to pay for themselves, and smaller companies don’t always have the cash. Some countries lack basic waste collection or have weak enforcement, so shortcuts continue.
How to fix this? Some companies are turning waste into cash—selling scrap plastic to recyclers, or capturing heat to power their offices. A few big names have achieved “zero landfill” status, but for most, it’s a work in progress. The tension is real: manufacturers have to weigh “going green” with staying profitable, and sometimes that balance is tricky.
The Price Burden and the Push for Change
If you wonder why your favorite sneakers cost a little more this year, or why some gadgets are backordered for months, it all comes down to the cost burdens on manufacturers. Prices for raw materials like steel, copper, plastic, and even packaging paper have shot up since 2020. S&P Global’s price index showed an average 34% increase in raw material costs for manufacturers in 2021-2023. Add in the expensive shipping, tougher environmental rules, and higher wages needed to attract rare skilled labor, and margins get thinner than ever.
Manufacturers walk a tightrope here. Raise prices too much, and you scare off customers or lose out to cheaper imports. Don’t raise enough, and you risk bankruptcy. In China, more than 15,000 small manufacturing firms closed doors between 2020 and 2024, as per China National Bureau of Statistics data. Small players have it worse—big names can negotiate better deals or hedge their bets, but the little guys struggle to survive.
So manufacturers are forced to innovate. They digitalize: installing smart robots that only use power when needed, tracking material usage with AI, or even 3D-printing parts on demand to reduce waste. Some shift production closer to customers—a U.S. maker might build in Mexico instead of China, for instance, to dodge shipping risks and tariffs. But even these solutions don't erase all the hurdles, and the upfront investment is huge. Some manufacturers collaborate, sharing warehouses or pooling supply chain resources to keep costs down—something unheard of two decades ago. Even Mira, my electronics-engineer spouse, says her company started buying chips together with competitors, just to score a bulk discount in the shortage chaos.
Need a quick tip? If you run a manufacturing business, don't ignore data. Start with a simple spreadsheet. Track your material costs, shipping times, and wages every month. This isn’t glamorous, but it catches cost spikes early—before you land in trouble. Find local suppliers if you can, as homegrown options proved more reliable during border shutdowns. And if you think green tech will bankrupt you, check out new government grants or private investor programs that fund cleaner production. Staying still is no longer an option. Manufacturers need to keep their eyes open and adapt, or they risk being left behind.